Wire drawing is a process to produce a small diameter wire from billet by applying tensile force. A leading end of a wire to be drawn is pointed in a rotary swaging machine or by some other means. The point is then inserted through the die then properly gripped and pulled sufficiently by a suitable means, so that the end can be attached to the power real as shown in Figure 21.7. Then the power reel rotates at the proper speed and pulls the entire piece through the die opening. A conical opening in a material of the die is never in contact with the wire being drawn but is filled with lubricant.
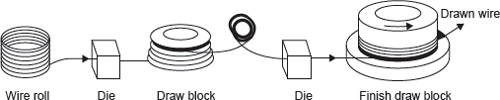
Figure 21.7 Wire Drawing Process
The die angle depends upon the metal to be drawn including its hardness from previous cold working and the reduction of area to be effected. A die angle of about 12° is average for the drawing of steels with carbide. Two lubricant methods are currently employed. The mechanism of wire drawing is shown in Figure 21.8. In one method, the wire surface is cleaned, coated with lime, and this is thoroughly dried. Before entering the die, a lubricant such as a grease or soap is applied to this surface. The dried lime coating helps to hold this lubricant to the surface as it passes through the die. In the other method, the surface of the wire is first coated with copper or tin. Then, as the metal enters the die, a water carried lubricant is applied. This method is more suitable for final drafts of fine wire.
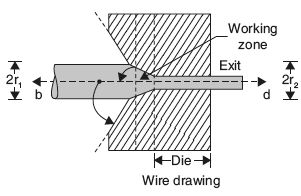
Figure 21.8 Mechanism of Wire Drawing
Considerable heat is generated during a wire drawing operation, and water may be circulated around the die to cool it. When the metal of the wire has reached its work hardening limit, annealing is necessary before additional drawing can be done.
Leave a Reply