A number of defects can occur during the welding processes, some of them are shown in Figure 20.51. There are many other defects which are discussed in the following paragraphs.
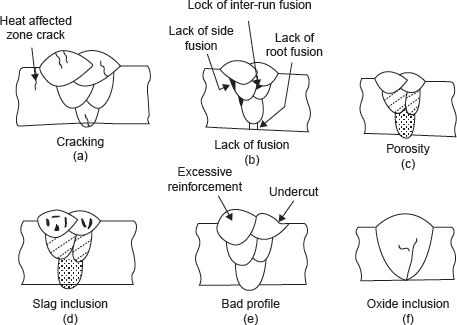
Figure 20.51 Welding Defects
Cracks: Cracks occur in the welded joint due to improper welding and solidification of different metals. Cracks may be of the following types.
- Micro cracks: Very small cracks, which can be seen with the help of microscope only.
- Macro cracks: These cracks can be seen by naked eye.
- Fissures: These cracks are wider, which occur at the surface of the metal.
There are different types of cracks. Cracks occurring in the base metal are known as cold crack because it occurs at low temperature due to improper welding, high cooling rate, wrong filler material, or high carbon and phosphorous in parent metal. Crack occurring in hot metal zone or weld metal zone is known as hot cracks, and it occurs due to improper solidification, clamping, etc.
Lack of Fusion: Wrong weld parameters, such as poor weld design, feed rate, welding speed, current, and voltage, lead to the problem of fusion and penetration. A proper arc length and good weld design may prevent the problem of poor fusion and improper penetration.
Porosity: Porosities are voids, holes, or cavities of usually spherical shapes. It is caused by gas entrapped in weld metal during solidification, and chemical reactions during welding, contaminates such as dirt, oil, grease, rust, paint, etc. Blowholes are voids of large size. Porosity and blowholes are scattered throughout the cross-section of a weld randomly. Small porosities appeared on the surface are known as pinholes. Pinholes are smaller in size. To reduce the porosity there should be proper shielding of molten metal pool, proper cleaning, i.e., free from oil, grease, paints, etc., to avoid absorption of gases like O2, N2, H2.
Slag Inclusion: Slag inclusion in the form of oxides, sulphur, and flux in the weld causes poor strength and leads to corrosion in the metal. It occurs due to inadequate cleaning of the welding areas.
Shrinkage Cavity: It occurs in the welding of thicker parts where large amount of filler metal is required. The molten metal shrinks during solidification and forms a cavity on the surface, which is known as shrinkage cavity.
Undercutting: Undercutting is a form of groove on the welding surface. It occurs due to high current and high arc voltage. Proper controlling of current and voltage can prevent it.
Spatter: Spatters are small beads thrown in all directions during welding. It occurs due to very large current and wrong electrode selection.
Distortion: Distortion is a result of improper rate of heating and cooling in the weld zone or adjacent metal leading to the generation of stresses. Proper clamping and smaller diameter electrode may reduce the problem.
Leave a Reply