TSDFs manage hazardous waste under RCRA Subtitle C and generally must have a permit in order to operate. While most facilities have RCRA permits, some continue to operate under what is called “interim status.” Interim status requirements appear in 40 CFR Part 265 (USEPA 2012).
The permitting requirements for TSDFs appear in 40 CFR Parts 264 and 270. TSDFs manage (treat, store, or dispose) hazardous waste in units that may include container storage areas, tanks, surface impoundments, waste piles, land treatment units, landfills, incinerators, containment buildings, and/or drip pads. The unit‐specific permitting and operational requirements are described in further detail in 40 CFR Part 264, Subparts J through DD (USEPA 1999).
Recycling
Some hazardous wastes can be recycled into new products. Examples may include lead‐acid batteries or electronic circuit boards. When heavy metals in these types of ashes go through the proper treatment, they could bind to other pollutants and convert them into easier‐to‐dispose solids, or they could be used as pavement filling. Such treatments reduce the level of threat of harmful chemicals, like fly and bottom ash while also recycling the safe product.
Portland Cement
Another commonly used treatment is cement‐based solidification and stabilization (Chaudhary and Rachana 2006). Cement is used because it can treat a range of hazardous wastes by improving physical characteristics and decreasing the toxicity and transmission of contaminants. The cement produced is categorized into five different divisions, depending on its strength and components. This process of converting sludge into cement might include the addition of pH adjustment agents, phosphates, or sulfur reagents to reduce the settling or curing time, increase the compressive strength, or reduce the leach ability of contaminants.
Incineration, Destruction, and Waste‐to‐Energy
The importance of the three T’s of incineration – temperature, time, and turbulence – has been recognized for many years. Recent general guidelines for three T’s include higher temperature (1200–2000 °F) and longer residence times (0.2–2.0 seconds) in order to promote more complete destruction of HAPs. Hazardous waste may be “destroyed.” For example, by incinerating it at a high temperature, flammable wastes can sometimes be burned as energy sources. For example, many cement kilns burn hazardous wastes like used oils or solvents. Today, incineration treatments not only reduce the amount of hazardous waste but also generate energy from the gases released in the process. It is known that this particular waste treatment releases toxic gases produced by the combustion of by‐product or other materials which can affect the environment. However, current technology has developed more efficient incinerator units that control these emissions to a point where this treatment is considered a more beneficial option (e.g. waste‐to‐energy – see Section 7.13.5 and Appendix G).
EXAMPLE 4.19
Mercury Waste
An incinerator burns mercury‐contaminated medical waste. The waste material has an ash content of 1%. The solid waste feed rate is 1 000 lb/h and the gas flow rate is 20 000 dscf. It is reported that the average mercury content of the particulates was 2.42 μg/g, when the vapor concentration was 0.3 mg/dscm (dry standard cubic meter). For the case where the incinerator emissions meet the particulate standard of 0.08 gr/dscf (0.1832 g/dscm) with a 99.5% efficient electrostatic precipitator (ESP), calculate
- the amount of mercury bound to the fly ash, which is captured in the ESP in grams/day
- the amount of mercury leaving the stack as a vapor and with the fly ash in grams/day.
SOLUTION
The amount of ash leaving the stack is:
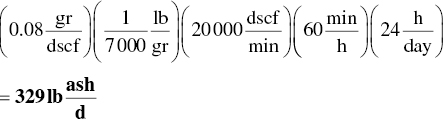
The amount of ash collected in the ESP with a 99.5% efficient ESP is
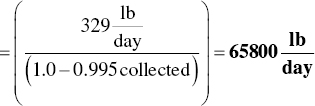
The amount of mercury leaving the stack with the fly ash is
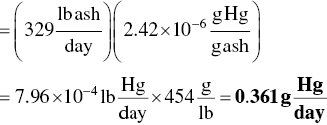
The amount of mercury leaving the stack as vapor is
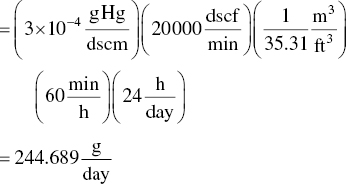
Therefore, total mercury leaving the stack = 244.689 + 0.361 = 245 g/day.
Pyrolysis
Some hazardous waste types may be eliminated using pyrolysis in an ultrahigh temperature electrical arc, in inert conditions to avoid combustion. This treatment method may be preferable to high‐temperature incineration in some circumstances such as in the destruction of concentrated organic waste types, including PCBs, POHCs, pesticides, and other persistent organic pollutants.
USEPA regulations for hazardous waste incineration (HWI) facility requires a minimum of 99.99% destruction and removal efficiency (DRE) of the principal organic hazardous constituents (e.g. PCBs, POHCs) being burned. In these cases, the final operating permits issued by the EPA almost always require a high temperature (1800 °F or higher) and minimum of 2.0 seconds residence time in the afterburner. Hospital (biomedical) waste incinerators often utilize a HWI type of facility.
The DRE is determined for each designated POHC from a mass balance of the waste introduced into the incinerator:
(4.19)
where
- DRE = destruction and removal efficiency (percent)
- W in = mass feed rate of POHC fed to an incinerator (lb/h or kg/h)
- W out = mass emission rate of POHC fed to the atmosphere (lb/h or kg/h)
EXAMPLE 4.20
During a trial burn, an incinerator was operated at a waste feed rate of 5000 lb/h and 7% O2 dry volume in the stack gases. The gas flow rate measured in the stack was 19 200 dscfm. Under these conditions, the measured concentrations of the principal organic hazardous component were
- Trichlorethylene (1) = 4.9 μg/dscf
- 1,1,1‐Trichloroethane (2) = 1.0 μg/dscf
- Methylene chloride (3) = 49 μg/dscf
- Perchloroethylene (4) = 490 μg/dscf
Each hazardous component listed here constitutes approximately 5% of the total waste feed rate. Calculate the DRE of the POHCs. Is the unit in compliance with regulations?
SOLUTION
Each hazardous component constitutes 5% of the total waste feed, therefore,

The mass flow rate of each hazardous component in the stack is given by
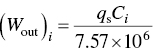
where

(Note that (454 g/h)(106 μg/g)(h/60 min) = 7.57 × 106)
Therefore,
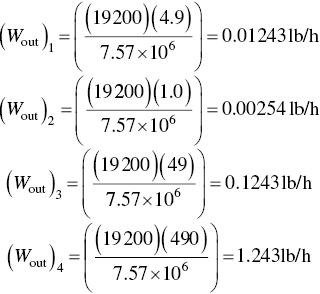
The DRE for component i, DRE i , is given by Eq. (4.16):
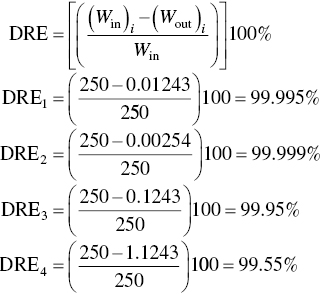
Regulations require that minimum 99.99% DRE be achieved. In this case, only two of the principal organic hazardous components (1 and 2) achieved this status. Assuming that either component 3 or 4 (or both) was a designated POHC, the unit would be out of compliance.
Leave a Reply