In thread rolling there is no chips formation, i.e., the threads are produced by plastic deformation. Two types of machines are used, namely, reciprocating flat die machine and rotating cylindrical die machine.
In a flat die method (Figure 21.11a), the cylindrical blanks are automatically fed from a hopper and placed upon a stationary flat hardened steel die plate. Another flat hardened steel die plate which reciprocates and advances and rolls the blank along between them until the thread is complete.
The rotating cylindrical die method (Figure 21.11b) may involve either two or three cylindrical dies having negative impression of the threads. These dies are rotated together on parallel axes, which may be horizontal or vertical. If two cylindrical dies are used, the shafts are normally horizontal and sufficient additional support for the blank between them must be provided. After the blank has been placed on the support, two rotating dies move toward each other to impress the thread on the rotating blank. Cylindrical die machines are more suitable for larger threads, over 3/8 inch outside diameter. Thread rolling has the following advantages over thread cutting.
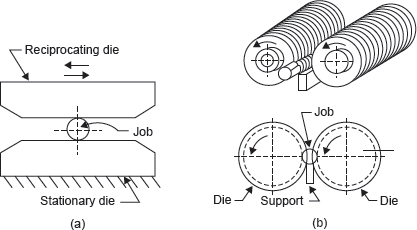
Figure 21.11 Thread Rolling Processes
- They are cheaper for producing sufficiently large quantities.
- They are stronger on a result of the cold working and favourable fibre flow line positioning.
Leave a Reply