In this section, we will dwell on discussing energy and, its close compliment, the environment with respect to precision manufacturing technology. These two – energy and the environment – will drive the technology and practice of precision manufacturing in the future. For sure, the more incremental development, following Moore’s Law – higher density data storage, advanced optics, more complex medical devices, nanoscale devices, sophisticated telecommunications and IT advances, etc. – will be present and continually push us. But it is the double header of energy and environmental impacts of product design, manufacturing, use and reuse, or disposal that will dominate our future. This is expected to compel us toward:
- technology for advanced energy sources (e.g. batteries, photovoltaic/solar, hydrogen fueled motors, photosynthesis, hybrid vehicle, high‐efficiency engines, hydropower, wind power, advance bio‐fuel manufacture)
- sustainable manufacturing [e.g. green machines, green factories, green processes, and systems (including supply chain), minimizing or eliminating waste, consumables, energy, green products (zero defect and zero effect), reuse, or remanufacturing].
For sustainable manufacturing, we need to rethink our approach to product design and manufacturing. For example, how can we provide incremental solutions to the large problems of global warming, excessive energy and resource consumption, manufacturing related atmospheric contamination, etc.?
Technologies for Sustainable Manufacturing
Increasingly, concerns about the availability and cost of energy and raw materials, the impacts of industrial activity, and the efficient reuse of consumer products at the end of their life are driving efforts toward green manufacturing. This is part of a much larger international concern over the overall accomplishment of sustainability in design and manufacturing. Sustainability, as defined here, implies a level of resource utilization that is very comprehensive in its scope. It must be in accord with a level necessary to ensure that, over time, the resource will (i) not only be available, but (ii) demand is reduced to approach a level of what is naturally sustainable. That is, the “gap” between current use and sustainable use must be understood. This is a hard measure to meet but it is, ultimately, what is necessary (Dornfeld and Lee 2008).
The topic of “green business” is very popular today in the business world. Companies from GE (with its “eco‐friendly” campaign) to Ford (with its sustainable “supply chain” for some products) are finding it both profitable and responsible to promote green products and green economy. Automaker like Toyota emphasizes the need for the entire manufacturing process, including the supply chain, to be green. Others, like Cummins Engine, are engaged in “remanufacturing” for engine components that have life after first use.
A short introduction to green manufacturing is presented followed by a review of the elements and scope of the system that should logically be included in any discussion of green manufacturing. The concept of “technology wedges” and how they might be applied to identifying opportunities for environmentally benign manufacturing and integrating solutions with existing processes or supply chains is discussed.
Green Manufacturing Pipeline
Integration of green components and analysis into manufacturing systems was considered early on by Sheng et al. (1995). Some researchers have addressed specific parts of the manufacturing process in more detail with success, e.g., minimum quantity lubrication/dry machining, which is now being implemented in a number of manufacturing operations internationally (Zimmerman et al. 2003). These specific accomplishments are often referred to as “technology wedges” that form part of a comprehensive solution. The wedges are explained in more detail in the next section. Ishii has looked at incorporating end‐of‐life considerations when products are designed (1999).
A schematic of the green elements of design and manufacturing is shown in Figure 8.14. The “life cycle” of the product from design to recycling or reuse at end of life must be considered. The figure refers to life cycle analysis (LCA) tools (see Section 6.3) (Das 2002, 2005; Das and Houtman 2004), design for assembly (DFA), and design for environment (DFE). The figure distinguishes between the design of a product and the processes or systems that make the product. Of importance is that both the design of the process and how the process operates to manufacture the product are considered. Substantial opportunities exist in the design of machines that make products (Taniguchi et al. 2005), as well as in their productive operation [macro and microplanning, for example, see Srinivasan and Sheng (1999a, b)].
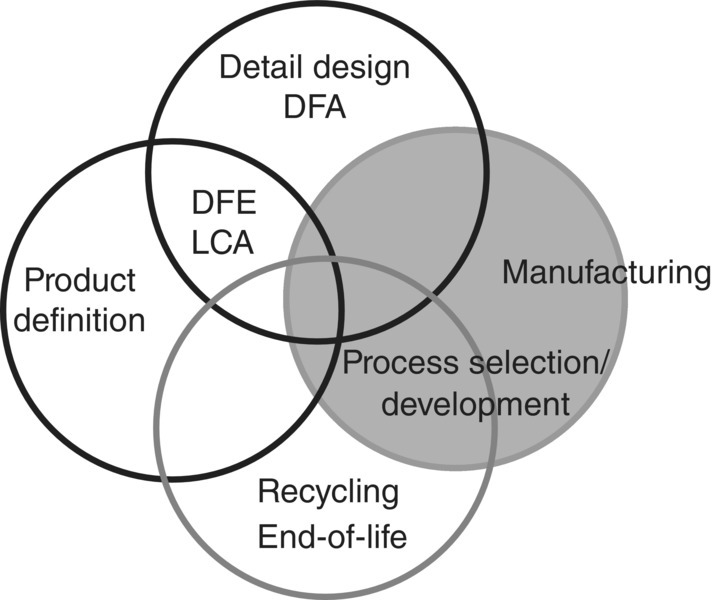
Regarding green manufacturing practices, it is necessary to consider the environmental impact of all the elements in a product’s life cycle as shown in Figure 8.15. The figure covers the broadest scope possible from the original source of raw materials (including mining costs) to eventual disposal of the used product. Each element includes waste (or non‐utilized resources and by‐product). The energy and resources consumed in each of these stages of the process, and the waste output, will “count against” any benefits of the new product or machine resulting from the process. In fact, to be complete, we could consider manufacturing to include elements of most of the stages of the product’s life cycle since mining, conversion, and transport are arguably part of manufacturing. At a more detailed level, sustainable manufacturing can be addressed by improving the individual components to manufacturing (Figure 8.16). Here we see contributors to sustainable manufacturing including power sources and processes.
To be effective, there must be a net energy, resource, or environmental impact savings over the life of any product or process produced in an “environmentally benign” manner to meet the sustainability definition. Colloquially, it can be said: “if you consume as much resources in manufacturing a product as you save in use of the product you have not succeeded!” This requires careful accounting for the impact of all the process chain elements and that is often not easy to do.
Leave a Reply