In July 1996, a paper company located on the west bank of the Mississippi River undertook a program to eliminate the discharge of industrial wastewater to the river. A wastewater recycling system consisting of pumps, surge tank, and filtration system reduced discharges by 99%. The successful pollution prevention includes the annual elimination of 562 million gal of wastewater, 149 000 lb of total suspended solids, and 57 000 lb of biochemical oxygen demand. The plant primarily manufactures colored construction‐grade paper from a mixture of secondary fiber, stone ground‐wood pulp, and kraft pulp.
The company initiated a Zero Discharge program, described in detail by Klinker (1996), having two goals:
- Eliminate the discharge of wastewater into the Mississippi River.
- Improve the efficiency of water use in manufacturing to reduce the mill’s dependence on river water.
Recycling treated wastewater into the mill’s water supply system would accomplish these goals.
Besides the regulatory motivation for reusing wastewater, the company had concerns about periodic interruptions in the flow of water to the mill. A local power company’s hydroelectric plant located immediately upstream caused these interruptions. On occasion, the utility lowered the river level by halting water flow through a canal that also feeds water from the Mississippi to the paper mill. When this occurred, the mill had to stop its manufacturing process until there was sufficient volume of water to run the mill. By reusing wastewater, the company could reduce its dependency on river water and avoid this disruption to production.
The nucleus of the Zero Discharge program, a closed‐loop wastewater recycling system in the mill, not only offers environmental benefits but also generates difficulties because of the increase in the volume of recycled wastewater used in manufacturing and the expenses associated with addressing these problems.
Closing the Loop
Figure 7.6 is a diagram of the company’s closed‐loop wastewater recycling system. Before the Zero Discharge program began, the Mississippi River supplied all the process and cooling water for the mill. Freshwater from the river entered the mill, passed over a fine mesh screen, and entered a 2700‐gal freshwater tank. The house pump directed it to process and cooling water demand points in the mill.
The resulting process wastewater underwent treatment in the company‐owned, activated sludge, wastewater treatment plant. Discharge was through a process‐wastewater outfall designated outfall 01. Cooling wastewater discharge was at outfall 02. Wastewater sludge underwent dewatering on a belt filter press followed by land application on company owned agricultural land.
Before the Zero Discharge program, the plant discharged an average of 607 000 gal of process wastewater and 1.14 million gal of cooling wastewater into the river each day. By using the closed‐loop system to pump increased amounts of treated wastewater into the freshwater tank, the mill was able to state that its process and cooling water consisted of nearly 100% recycled wastewater. The total volume of wastewater discharged to the river decreased by 82% (Klinker 1996).
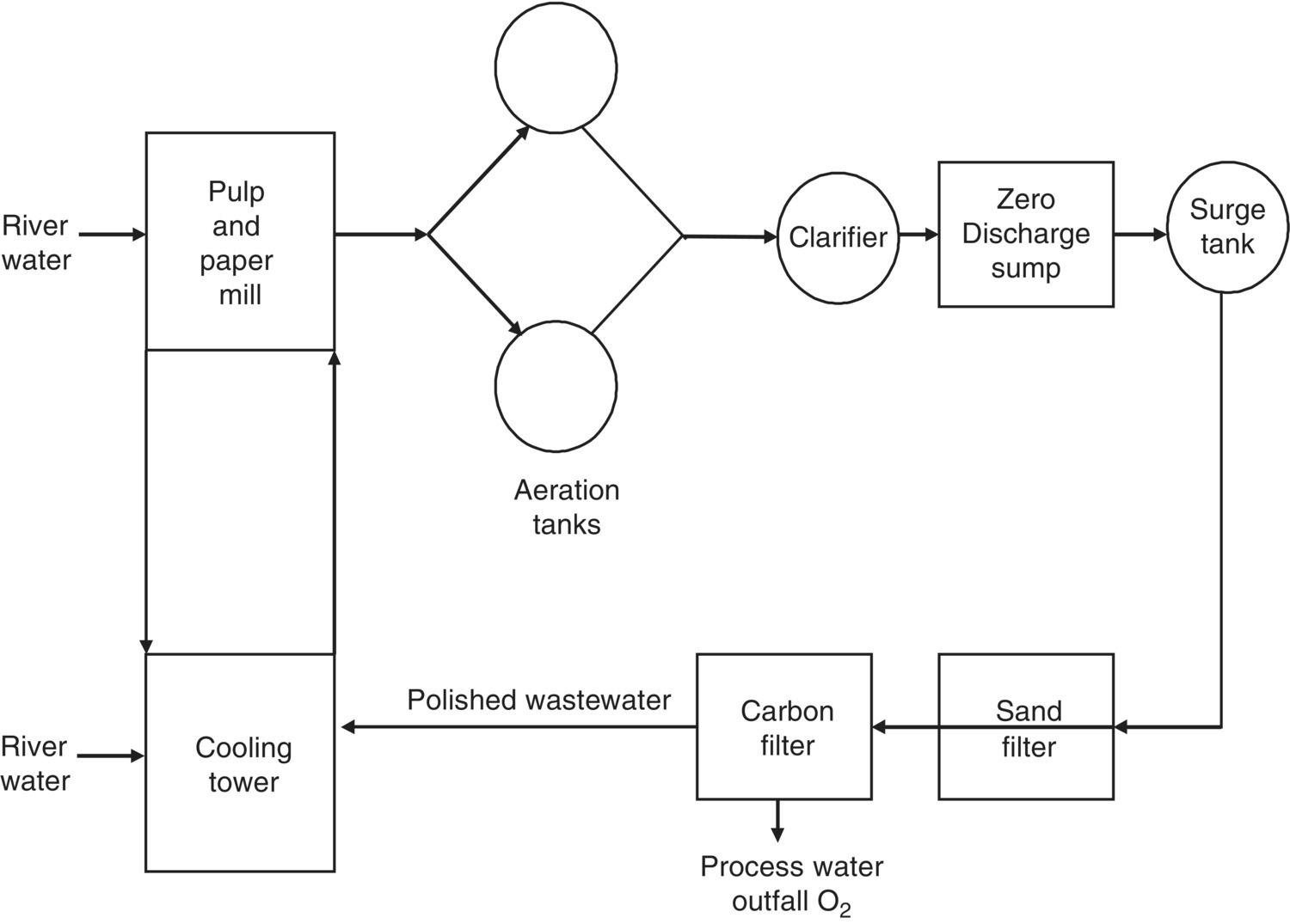
Conclusions
The US pulp and paper industry has made significant progress towards reducing water consumption and increased water recycling and reuse through innovative technologies and process modification. Some mills have implemented processes that “close the loop” and proved to be successful Zero Discharge bleach plant systems. The effects of the EPA’s Cluster Rule, which became applicable on 15 April 2001, have yet to be fully felt. It is reasonable to expect, however, that the new linkage of federal regulations aimed at reducing air and water pollution will result in an even higher level of processed water recycling, reuse within the mills, as well as greater pollution prevention and Zero Discharge in water, air, and solid waste areas the next decade or two. As technologies to reduce facility water, chemical, and energy use have advanced, other chemical industries, like pulp and paper and power generating industry, have increasingly embraced the use of reclaimed water for a wide‐ranging suite of purposes: from process water, boiler feedwater, and cooling tower use to finishing toilets and site irrigation. Current technologies produce reclaimed water that can provide the same performance as more‐expensive potable water. As water resources become increasingly valued around the world, industrial water reuse is expected to expand (DaSilva and Goodman 2014).
Leave a Reply