The space shuttle is a complex system consisting of an external fuel tank, two solid rocket boosters and the Space Transportation System (STS) orbiter vehicle. In this section, we only examine the structure and materials of the orbiter. The orbiter resembles a conventional aircraft with double-delta wings, and uses many of the same materials. The orbiter is divided into nine major structural sections (Fig. 3.12). Most of the sections are constructed like a passenger airliner using aircraft-grade aluminium alloys. The major structural assemblies are connected and held together by rivets, bolts and other fasteners, again much like an airliner. However, some materials used in the space shuttle are unique, and are not found in fixed- or rotary-wing aircraft. One distinguishing feature of the orbiter is the reusable thermal insulation system. Over 25 000 ceramic and carbon–carbon composite tiles, that can withstand temperatures of about 1200 °C and above 2000 °C, respectively, are used to insulate the underlying structure during re-entry.
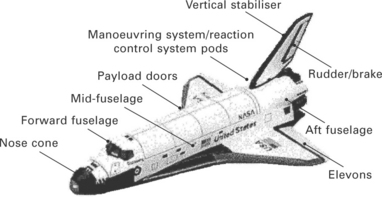
3.12 Main sections in the space shuttle orbiter.
The forward fuselage section is robustly designed to carry the high body bending loads and nose gear landing loads. The body skin panels, stringers, frames and bulkheads in the forward section are made with the same aluminium alloy (2024 Al) found in conventional aircraft structures. The windows are made using the thickest ever pieces of optical quality glass. Each window consists of three individual panes: the innermost pane is 15.9 mm (0.625 in) thick tempered aluminosilicate glass whereas the centre and outer panes are 33 mm (1.3 in) and 15.9 mm fused silica glass. This design can withstand the extreme heat and thermal shock during re-entry when temperatures reach 600–700 °C.
The mid-fuselage section is the 18.3 m (60 ft) long structure that interfaces with the forward and aft fuselage sections and the wings. The mid-fuselage includes the wing carry-through structure, which is heavily loaded during reentry, and the payload bay (including its doors). The fuselage is constructed with monolithic and honeycomb sandwich panels of aluminium, which are stiffened with load-bearing vertical and horizontal frames. The frame is constructed using 300 struts of metal matrix composite (boron fibre/aluminium tubes), which has exceptionally high stiffness and provides a weight saving of 45% compared with a conventional aluminium construction. The payload bay doors are a sandwich composite construction (carbon fibre–epoxy skins and Nomex core) with carbon-fibre composite stiffeners. This construction reduces the weight by over 400 kg (900 lb) or 23% compared with an aluminium honeycomb material.
The aft fuselage consists of an outer shell, thrust section and internal secondary structure, and it supports the manoeuvring/reaction control systems pods, main engines and vertical tail. The aft fuselage skins are made of aluminium alloy reinforced with boron fibre-epoxy composite struts. These struts transfer the main engine thrust loads to the mid-fuselage and external tanks during take-off. At take-off the two solid rocket boosters generate a combined thrust of 25 MN (5.6 million lb), which is over 200 times the twin engine thrust of a Boeing 737. Owing to the extreme thrust, titanium alloy strengthened with boron–epoxy struts is used near the engines.
The wing and vertical tail is constructed mostly with aircraft-grade aluminium alloy. The outboard wing section is made with high temperature nickel honeycomb sandwich composite and the inboard wing section of titanium honeycomb. The elevons, used for vehicle control during atmospheric flight, are constructed of aluminium honeycomb.
Leave a Reply