The mould in this process is made up of a mixture of dried silica sand and phenolic resin formed into thin, half-mould shells, which are clamped together for pouring (Figure 20.26). The sand, free from clay, is first mixed with either urea or phenol formaldehyde; the mixture is put into a dump box or blowing machine. A metal pattern is pre-heated and sand mixture is dropped on the pattern and held for 15–30 s. After hardening the shell, mould is removed from pattern with the help of ejector pins. These mould halves are assembled together with clamps or adhesives. Thus, the prepared mould is used for casting purpose.
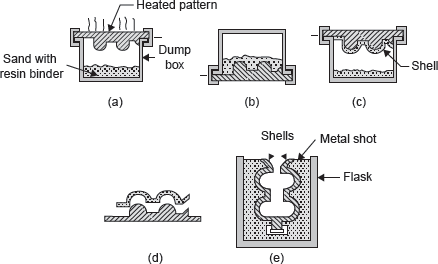
Figure 20.26 Steps in Shell Moulding
Advantages
- Castings have closer dimensional tolerance and better surface finish.
- Cleaning cost is low.
- Less skilled labour may be employed.
Disadvantages
- This process is limited for small casting.
- It involves expensive resin, expensive baking, and mould making process.
- This process is not economical for small run because of expensive equipments.
Leave a Reply