Addition of alloying elements to metal
Metals are not used in aerospace applications in their pure (unalloyed) condition. Pure metals are too soft to use in aircraft structures and engines, and must be alloyed with other elements to produce high-strength materials. For instance, the addition of a few percent of copper to aluminium increases the strength by 500–600%: about 80 MPa for pure Al to 450–500 MPa for the Al–Cu alloy. As another example, adding just 0.8% carbon to iron makes high-strength steel more than 1000% stronger than the pure metal.
There are many important reasons for alloying. The most common reason is to increase the mechanical properties of the base metal, such as higher strength, hardness, impact toughness, creep resistance and fatigue life. Alloying can also affect the other properties of metals: magnetic properties, electrical conductivity and corrosion resistance. In a few cases, alloying has the benefit of lowering the density of the metal, such as the addition of lithium to reduce the weight of aluminium alloys. In the majority of cases, however, alloying has little or no major effect on density unless a high concentration is added to the base metal. Another reason for alloying is to increase the maximum working temperature of metals or improve their toughness at very low temperatures. Certain metals are alloyed to improve their corrosion resistance and durability in harsh environments. Alloying may also reduce the material cost when a cheap alloying element is added to an expensive base metal, although this should be considered a side benefit rather than the main reason for alloying.
The process of adding alloy elements to a base metal is relatively simple, although aerospace alloys are subject to stringent quality control that requires their production under carefully regulated conditions. The base metal is melted inside a large crucible within a temperature-controlled furnace. The metal is usually in a pure form (> 99% purity), although it often contains trace amounts of impurity elements that were not fully removed during the smelting and refining of the ore. All the base metals used in aircraft structures and engines, aluminium, magnesium, titanium, iron and nickel, contain impurities. For example, aluminium alloys used in aircraft structures contain low concentrations of silicon and iron impurities from the bauxite ore. In general, the effect of impurities is deleterious whereas the effect of alloying elements on properties is beneficial. Provided the concentration of impurity elements is kept low then they do not pose a problem and, in some materials, may be beneficial to the processing or mechanical properties. For example, small amounts of silicon increase the fluidity of molten aluminium, which makes it easier to cast without the formation of pores and cavities. As another example, low concentrations of iron and atomic oxygen impurities in titanium increases the yield stress by solid solution strengthening.
The base metal is heated inside the furnace to a temperature sufficient to melt and dissolve the alloying elements into the melt. The furnace environment is controlled during the melting of reactive base metals, such as titanium, nickel or magnesium, to stop oxidation and contamination from the air. The melting of reactive metals is performed under vacuum or inert gas (e.g. argon). Vacuum induction melting (VIM) is one of the most common methods, whereby melting of the base metal and alloying elements is performed under high vacuum to minimise oxidation and remove dissolved gases (such as hydrogen and nitrogen) from the melt. Alloying elements are added to the molten base metal in measured amounts to produce the metal alloy melt. The elements are usually added as powder or small pellets, which are dissolved into the liquid metal and distributed through the melt by stirring and mixing. Once the alloying elements have dissolved in the molten metal it is ready for casting.
Solubility of alloying elements
Alloying is based on the principle that the alloying elements are soluble in the base metal. That is, the alloying element can dissolve as individual atoms when added to the molten base metal, and may remain dissolved when the material solidifies and cools to room temperature. There are two types of solubility: unlimited solubility and limited solubility.
Unlimited solubility means that the alloying element completely dissolves in the base metal, regardless of its concentration. For example, nickel has unlimited solubility in copper in concentrations less than 30% by weight. After solidification, the copper and nickel atoms do not separate but instead are dispersed throughout the material (Fig. 6.1). The structure, properties and composition are uniform throughout the metal alloy, and there is no interface between the copper and nickel atoms. When this occurs the alloy is called a single-phase material.
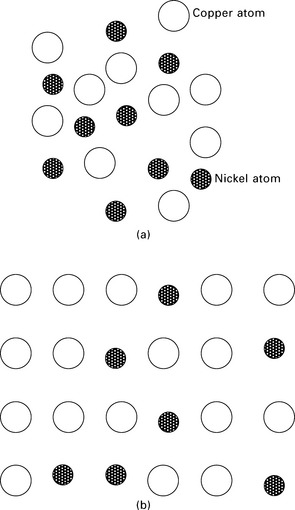
6.1 Unlimited solubility of nickel in copper: (a) molten alloy; (b) solid alloy.
Unlimited solubility occurs when several conditions, known as the Hume–Rothery rules, are met:
• Size factor: The atomic sizes of the base metal and alloying element must be similar, with no more than a 15% difference to minimise the lattice strain.
• Crystal structure: The base metal and alloy element must have the same crystal structure.
• Electronegativity: The atoms of the base metal and alloying element must have approximately the same electronegativity.
The Hume–Rothery conditions must be met for two elements to have unlimited solid solubility. Even when these conditions are met, however, there can be instances when unlimited solubility still does not occur.
Limited solubility means that an alloying element can dissolve into the base metal up to a concentration limit, but beyond this limit it forms another phase. The phase which is formed has a different composition, properties and (in some cases) crystal structure to the base metal. Most of the alloying elements used in aerospace base metals have low solubility. For example, when copper is present in aluminium it is soluble at room temperature up to about 0.2% by weight. At higher concentrations the excess of copper reacts with the aluminium to form another phase (CuAl2). As another common example, when carbon is added to iron in the production of steel it has a solubility limit of under 0.005% by weight at 20 °C. In higher concentrations, the excess of carbon atoms form carbide particles (e.g. Fe3C) which are physically, mechanically and chemically different to the iron.
The limited solubility of alloying elements is an important means of increasing the strength of aerospace metals by precipitation hardening. The concentration of alloying elements used in the main types of base metals for aircraft are often well above their solubility limit to promote strengthening by precipitation and other hardening mechanisms. However, there is a practical limit to the amount of nonsoluble alloying elements that can be added to a base metal. When there is too much of the alloying element then the metal can become brittle and not useful for structural applications.
Selection of alloying elements
The alloy produced is determined by the types and concentrations of alloying elements used in the base metal. For example, the aluminium alloy known as 2124 Al, commonly used in aircraft structures, contains 3.8–4.0% (by weight) copper and 1.2–1.8% magnesium together with smaller amounts of other alloying elements (e.g. zinc) and impurities (e.g. iron, silicon). The amount of alloy elements added to the liquid metal is often specified over a narrow range because it is often impractical to add precise amounts. For example, the magnesium content in 2124 Al can be anywhere between 1.2 and 1.8% by weight, but when the content is outside these limits then the alloy is no longer classified as 2124 Al. After the alloying elements have fully dissolved into the melt, the metal is then solidified for processing into an aircraft component.
The types and amounts of alloying elements determine the metallurgical and mechanical properties of metals. Different alloying elements alter the properties in different ways. For example, when copper is added to aluminium it has a powerful strengthening effect but when used in titanium it has virtually no influence on the strength properties. As another example, chromium in steel promotes high corrosion resistance but has no impact on the corrosion properties of most other metals.
Certain alloying elements improve the strength properties by solid solution hardening or precipitation hardening, other elements increase the strength by refining the grain size, whereas different elements again may enhance the corrosion or oxidation resistance. For this reason, a number of alloying elements are used in the same metal rather than a single element. For instance, titanium alloys used in aircraft structures often contain two dominant alloying elements (aluminium and vanadium) with small concentrations of other elements (e.g. tin, zirconium, molybdenum). Another example is nickel superalloys that contain large amounts of many different alloying elements to increase the maximum working temperature, including iron, chromium, molybdenum, tungsten, cobalt, aluminium and niobium. Some alloying elements have several functions, such as chromium in stainless steel that increases both strength and corrosion resistance.
The concentration of alloying elements is also critical to controlling the mechanical and durability properties. The properties of metals do not necessarily increase steadily with greater additions of alloying elements; instead there is an optimum concentration. For example, the optimum copper content in aluminium for maximum strengthening is 3–5%; below this range the metal is too soft and above this range too brittle. The types, approximate concentrations and main functions of the principal alloying elements used in aerospace structural metals are given in Table 6.1.
Table 6.1
Alloying of the main types of base aerospace metals (SSS = solid solution strengthening; PH = precipitation hardening)
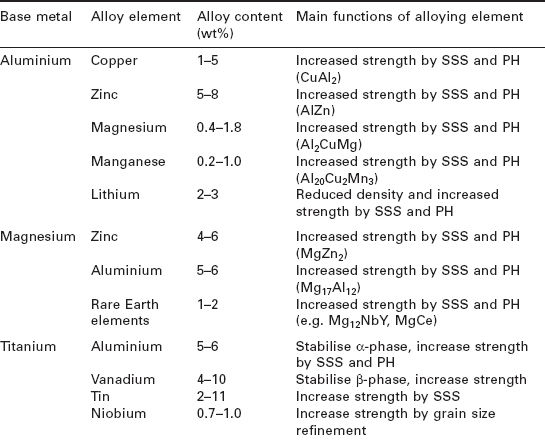
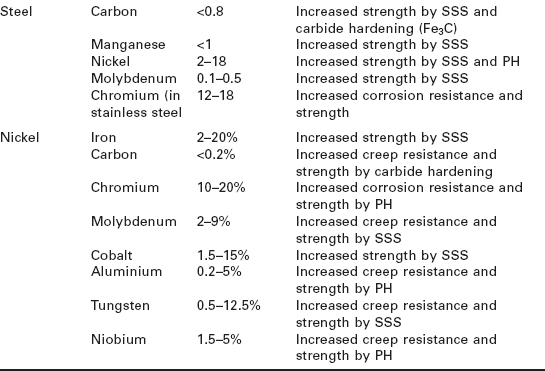
Leave a Reply