1. Fineness
Fineness of cement is a measure of the size of particles of the cement. It is expressed as the specific surface of cement. It is an important factor to decide the rate of gain of strength and uniformity. In general, finer the grains higher the surface area.
The rate of hydration will be higher with the increase in fineness of cement. This is because of the larger surface area available for chemical reaction. Further, this leads to earlier development of strength. The effect of fineness increases with strength as shown in Fig. 6.1. As per specification, the residue of cement should not exceed 10% when sieved through a 90-micron sieve.
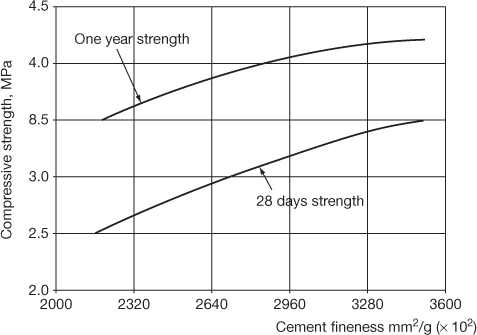
Figure 6.1 Typical cement fineness and compressive strength
2. Setting Time
When water is added to the cement and mixed, it forms a paste which gradually becomes less plastic and finally forms a hard material. The time taken for the entire process is called the setting time, which is divided into the initial setting time and the final setting time.
For convenience, the initial setting time is regarded as the time when the cement paste loses its plasticity, whereas the final setting time is the time elapsed between the time of water addition to the cement and the time when the paste has completely lost its plasticity, i.e., it has attained sufficient firmness to withstand certain pressure. For OPC the initial setting time should not be less than 30 min. and the final setting time not more than 600 min.
The initial setting time should be sufficiently long for finishing operations such as transporting and placing of concrete. The length of the setting time depends on the quantity of mixing water and the atmospheric temperature rather than on the cement.
3. Soundness
Cement which has less expansive qualities when mixed with water is termed as soundness. The soundness of cement is affected by the undesirable expansion of some of its constituents which could occur even after setting. This expansion causes disintegration and severe cracking. Mainly, the presence of free lime and magnesia in cement leads to unsoundness. The unsoundness may be controlled by:
- Limiting the MgO content to less than 0.5%
- Fine grinding
- Aerating the cement for aeration for several days
- Thorough mixing
4. Compressive Strength
It is one of the important properties of cement. The strength of cement is generally assessed from compression tests on cement-mortar cubes (1: 3) with an area of 5,000 mm2. The graded standard sand to be used for the mortar cube preparation should conform to IS: 650–1991. For OPC, the compressive strength at 3 and 7 days shall not be less than 16 and 22 MPa, respectively.
5. Heat of Hydration
The reaction of silicates and aluminates of cement with water forms a binding medium which solidifies into a hardened mass. This process is termed as hydration. During hydration, heat is generated and exists for a prolonged period. This heat of hydration is defined as the quantity of heat (in calories/gram of hydrated cement) liberated on complete hydration at a particular temperature. Different types of cement liberate different quantities of heat. The heat of hydration for OPC should not be more than 66 and 75 cal/g for 7 and 28 days, respectively. It increases with temperature at which hydration takes place. For OPC it should be between 37 cal/g at 5°C to 80 cal/g at 40°C.
6. Specific Gravity
The specific gravity of OPC is around 3.15. The value may vary based on the materials used for manufacturing cement other than limestone and clay. However, the quality of cement is not governed by the specific gravity.
Leave a Reply