The global climate destabilization underway is primarily due to human combustion of fossil fuels for energy and the resultant greenhouse gas (GHG) emissions (IPCC 2007). There is a large consensus among scientists that if current trends continue in climate destabilization, the earth will reach a point of no return. The challenge of reducing atmospheric GHG like carbon dioxide (CO2) emissions is significant – with the Kyoto Protocol and the recent Paris Agreement, an entire order of magnitude below those values necessary to stabilize the global climate. To obtain a stable climate, GHG emissions would have to be reduced to a point equal to the natural absorption of CO2. After this stabilization occurs, the level of natural absorption will gradually fall as the vegetation sink is exhausted so GHG emissions would need to fall to the level of ocean uptake alone. This level is not well quantified, but it may demand emissions reductions to 5 Gt CO2 equiv/year (more than 80% below current levels) by the second half of the next century (Hansen and Sato 2004; Prentice et al. 2001).
In order to increase both the economic and environmental performance of the manufacturing sector, the government could introduce a second set of policies with the large‐scale PV (photovoltaic) manufacturing in order to facilitate the widespread adoption of industrial symbiosis. In industrial symbiosis, traditionally separate industries are considered collectively to gain competitive advantage by instituting the mutually beneficial physical exchange of materials, energy, water, and/or by‐products. Such a system collectively optimizes material and energy use at efficiencies beyond those achievable by any individual process alone. The key benefits of industrial symbiosis are collaboration and the synergies offered by geographic proximity (Chertow 2000). Industrial symbiotic systems such as the now‐classic network of companies in Kalundborg, Denmark, have spontaneously evolved from a series of micro‐innovations over a long time scale. In order to accelerate the process and demonstrate the possibilities for mutually beneficial collaboration, the government could engineer the design of the new solar PV manufacturing plant using industrial symbiosis.
The multi‐GW PV factory could sit at the center of a next generation EIP. The EIP would be made up of at least eight symbiotic factories as seen in Figure 9.5. These could be located outside of a major population center to provide raw materials, labor, and a ready market. The first factory would be a conventional recycling facility (1). In this way, the glass and aluminum needed to fabricate the solar cell could be recovered from recycled materials and thus have a lower embodied energy (95% lower for aluminum and 20% for glass) (Milne and Readon 2005).
The raw glass from the recycling plant will be fed to a sheet glass factory (2) and melted using natural gas. Generally, the high‐quality requirements of flat glass prohibit the use of post‐consumer waste glass. However, the glass industry is exploring a method to eliminate problems with color contamination by using thin plastic coatings, which can be made with a variety of colors and that would vaporize during remelting without affecting the quality of the new glass. This would benefit the industry considerably because using recycled glass, called cullet, has several important benefits that include (i) lowering the consumption of raw materials, (ii) reducing the release of CO2 formed in the chemical reaction of raw materials, (iii) increasing the life of the furnace by up to 30% due to lower melting temperatures, (iv) reducing energy use during the melting stage of production and thus reducing additional GHGs and operating costs, and (v) reducing the costs associated with pollution abatement due to lower emissions of NOx, SO2, and particulates (Pearce 2008). The factory will output cut sheets of 3 mm thick glass with seamed edges and low‐iron content in order to obtain a high‐solar transparency. Finally, the glass will be tempered for mechanical strength and coated with a transparent conductor such as tin oxide, zinc oxide, or indium tin oxide to be used as the substrates.
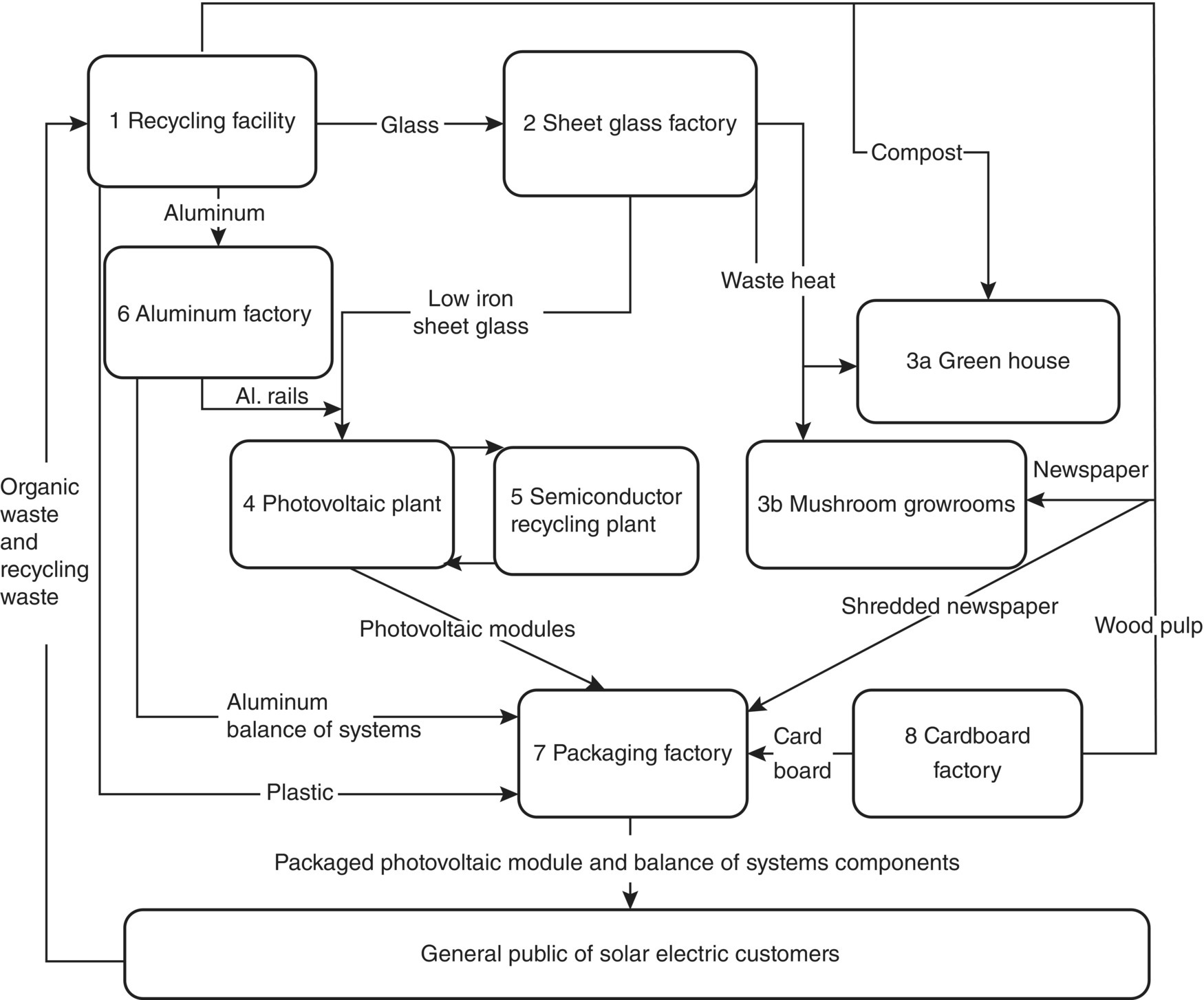
The production stages in the glass factory that utilize large amounts of heat will have integrated thermal recovery to provide lower grade heat for the other facilities and a greenhouse complex (3a). In the greenhouse complex, exotic plants can be grown year round in even northern climates utilizing the waste heat from the manufacturing plants in the EIP. Similarly, waste heat could be utilized to provide grow rooms for mushrooms (3b). In both agricultural plants, the food or other agricultural products will be sold outside of the park and the growing medium will be provided by the recycling facility (1), compost for the greenhouse (3a), and wood pulp or compost for the mushroom‐growing facility (3b). In warmer climates, the waste heat could be used to drive absorption chillers perhaps providing cooling for an office park.
The substrates will then be fed directly into the PV module plant (4). Then a group of semiconductor and metal thin‐film deposition systems will create and pattern the active layers of the solar cells. All waste semiconductors and metals will be captured and returned to a semiconductor recycling plant (5) to supplement the incoming and generally expensive high‐purity materials going into the deposition systems. The output of the PV deposition and patterning lines will be PV solar panels ready for protective coatings and packaging.
The aluminum extracted from common drinking cans in the recycling center (1) will be fed to an aluminum fabrication factory (6) that will produce coated aluminum rails for holding the glass solar panels. The aluminum rails will be extruded and used to provide a simple and inexpensive means of attachment to rooftops, ground mounted systems, or building integrated PV. In addition, the extruded aluminum rails could be designed into ground and flat roof mounting balance of system components. Similar to the glass manufacturing plant (2), waste heat will be recovered and used in the symbiotic collective or to heat the greenhouse (3a) or mushroom grow rooms (3b).
Next, in the packaging factory (7), the solar panels are interconnected if necessary and are sprayed with a protective polymer coating to seal them to the environment. The primary constituents of the polymer coating could again be acquired from the recycling plant (1) and common plastics. The panels would then be wired with quick connects so they can be easily installed in the field by connecting to each other an inverter or battery bank. Finally, the panels would be packaged for shipment to prevent damage in cardboard boxes and cushioned with shredded newspaper. The newspapers would again come from the recycling plant (1) and the cardboard could come from a cardboard plant (8), which would gain its raw materials from the recycling factory (1).
By co‐locating these factories in the EIP, the transportation costs and energy between them can be minimized and many of the inputs for the solar PV plant can literally come from waste products in the surrounding population centers. It should be noted that each factory will be scaled appropriately for the symbiotic system and should be individually profitable so that independent businesses can replicate this model by co‐locating and benefit from industrial symbiosis in future facilities.
Leave a Reply