As a success example, consider one where a corporate group devised and adopted a growth strategy whereby a majority of the wastes from one activity were converted to feedstock for another activity.
Seshasayee’s original enterprise was a paper mill. To ensure a regular supply of raw material, the company then set up a sugar mill. Bagasse, a waste from the sugar mill, was used as a raw material for papermaking. Another waste product, molasses, was used in a distillery for the production of ethyl alcohol. To guarantee a regular supply of sugarcane, the company took interest in the cultivation of this crop by organizing the farmers in the region. Seshasayee struck long‐term agreements with the farmers to buy back their produce and, in turn, took the responsibility of supplying them with water. Part of the water for cultivation was treated wastewater from the paper manufacturing operations. The company also used bagasse pith (a waste after the papermaking) and other combustible agricultural wastes in the region as energy sources. The agro industrial eco‐complex is illustrated in Figure 9.3.
This is particularly important to the theme of a process integration and intensification work because it involves the production of a good (paper) and a human food (sugar), and the sustainable generation of energy (from bagasse – e.g. waste‐to‐energy) and sustainable use of water. In this case, the discussion of the mini‐case study shows that it is possible to combine the production of a food and the generation of energy with the efficient use of water resources. This is important because the production of a commercial food (sugar) is economically and socially important, especially if it can be produced as sustainably as possible.
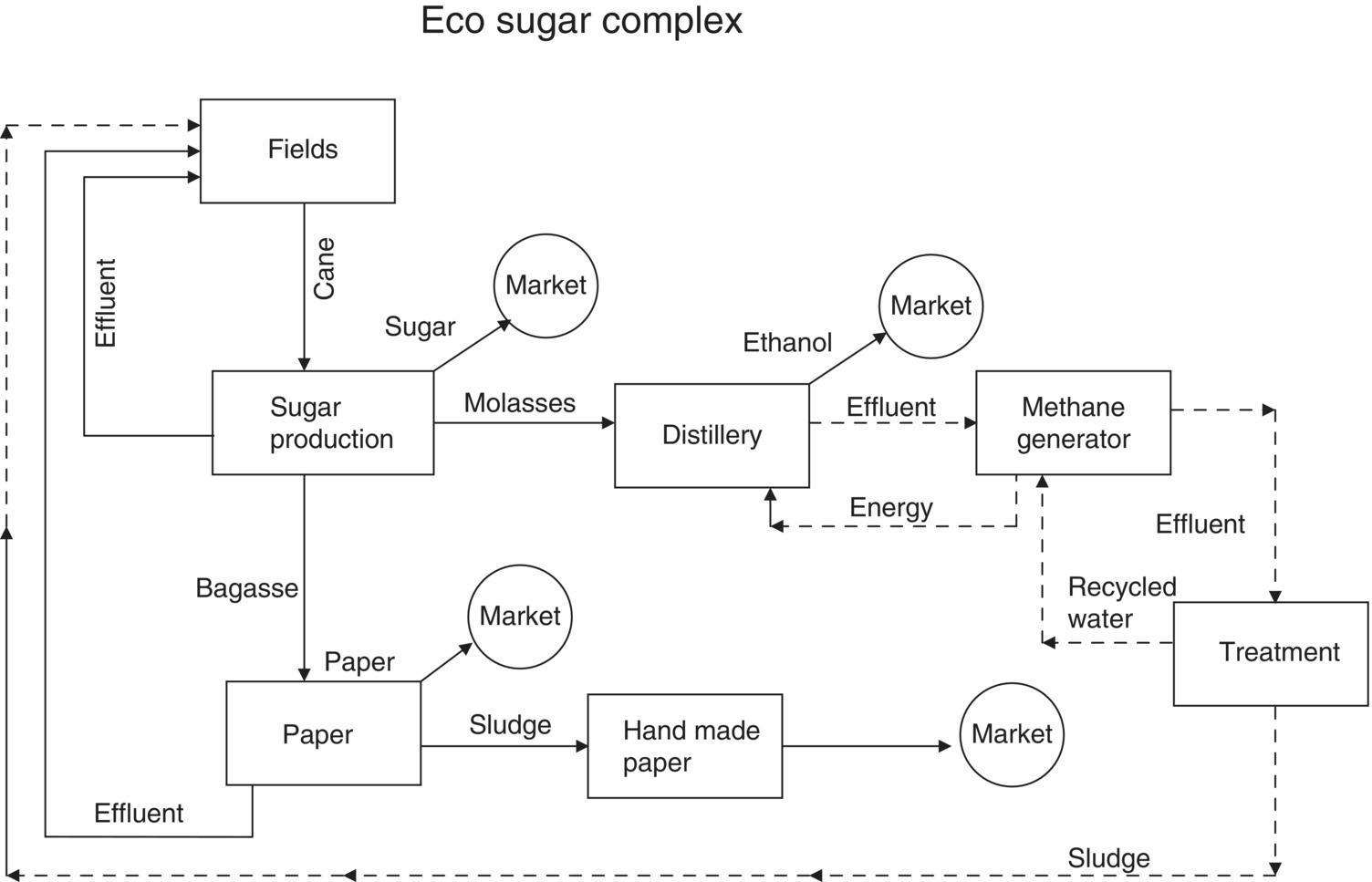
Mini‐Case Study 9.3: Materials and Energy Flow in an EIP in North Texas, USA
Consider, for example, an EIP in North Texas where the central facility is a steel mill. This facility, shown conceptually in Figure 9.4, utilizes scrap cars as the primary feed material. The steel from the vehicles goes to an electric arc furnace (EAF), producing a variety of steel products. The furnace also produces a significant quantity of EAF dust, which contains significant quantities of zinc, lead, and other metals. In the North Texas facility, the EAF dust is sent to a cement kiln where the trace metals (copper, chromium, manganese, nickel, lead, and other metals) have values. Automobile shredder residue (ASR) can be burned for energy recovery, or some of the plastics in the residue can be separated.
Another alternative for EAF dust, currently being exploited in Europe, is as a feed for zinc and lead recovery operations. The recovered zinc can then be used in producing galvanized steel products and batteries can be used as an alternative source of zinc.
These case studies illustrate the basic principle of EIP – integrating flows of materials, energy, and water in diverse industrial operations, increasing mass and energy efficiency. The three case studies examined in this section involved exchanges between facilities that are located adjacent to each other; however, co‐location of facilities in an EIP is not always necessary.
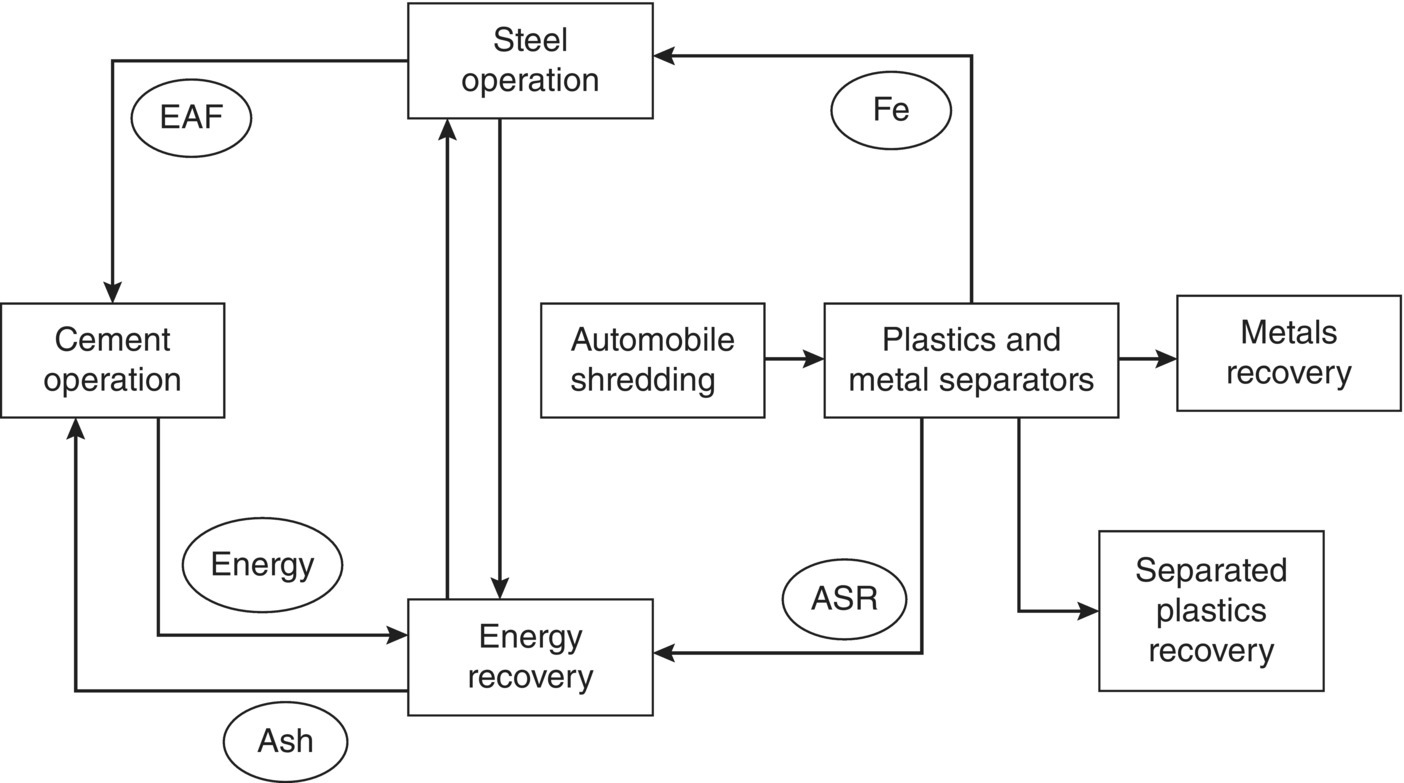
Leave a Reply