Strategic team planning is a particularly important process in the aerospace application due to its complexity. The team plan forms the vital link between the corporate vision and mission and its day-to-day operations. Every company must have a strategic team plan, an important communication document. The strategic team planning process helps top management make an institution more competitive through the secondary process of assessing or benchmarking its competitors. Strategic team planning helps executives think in terms of time. As the executives scan the environment, they evaluate their strongest competitors’ use of time as a competitive tool. Team plans include the following key elements:
- 1. Documentation
- 2. Communication
- 3. Personnel/hiring/training
- 4. Procurement
- 5. Testing
- 6. System implementation
- 7. Financial: billing, payments, working capital
- 8. Termination/closeout
- 9. Contingencies
A project team plan must state the team’s objective clearly, so that everyone understands his or her mission. The principles for setting clear objectives for the team include specifying anything considered important or essential by the customer and the project team must name specific results, i.e., reports, products, etc., to be achieved. The objectives must be realistic and must account for resources available, experience of the team, time available, and any constraints and uncertainties, and they should be achievable within a reasonable margin of error.
Objectives must be observable and should specify conditions that can be readily identified to the satisfaction of the customer and the user. At project completion, everyone should be able to agree on whether objectives were accomplished. Objectives must be stated using active terms such as “will,” not passive terms such as “should” or “try.”
Each work package (shaded box in Fig. 3.1.1) should include the following:
- 1. Task definition
- 2. Deliverables (end-items)
- 3. Time estimate/schedule
- 4. Resource requirements
- 5. Cost estimate/budget
- 6. Inputs and predecessors
- 7. Responsibility
- 8. Risk
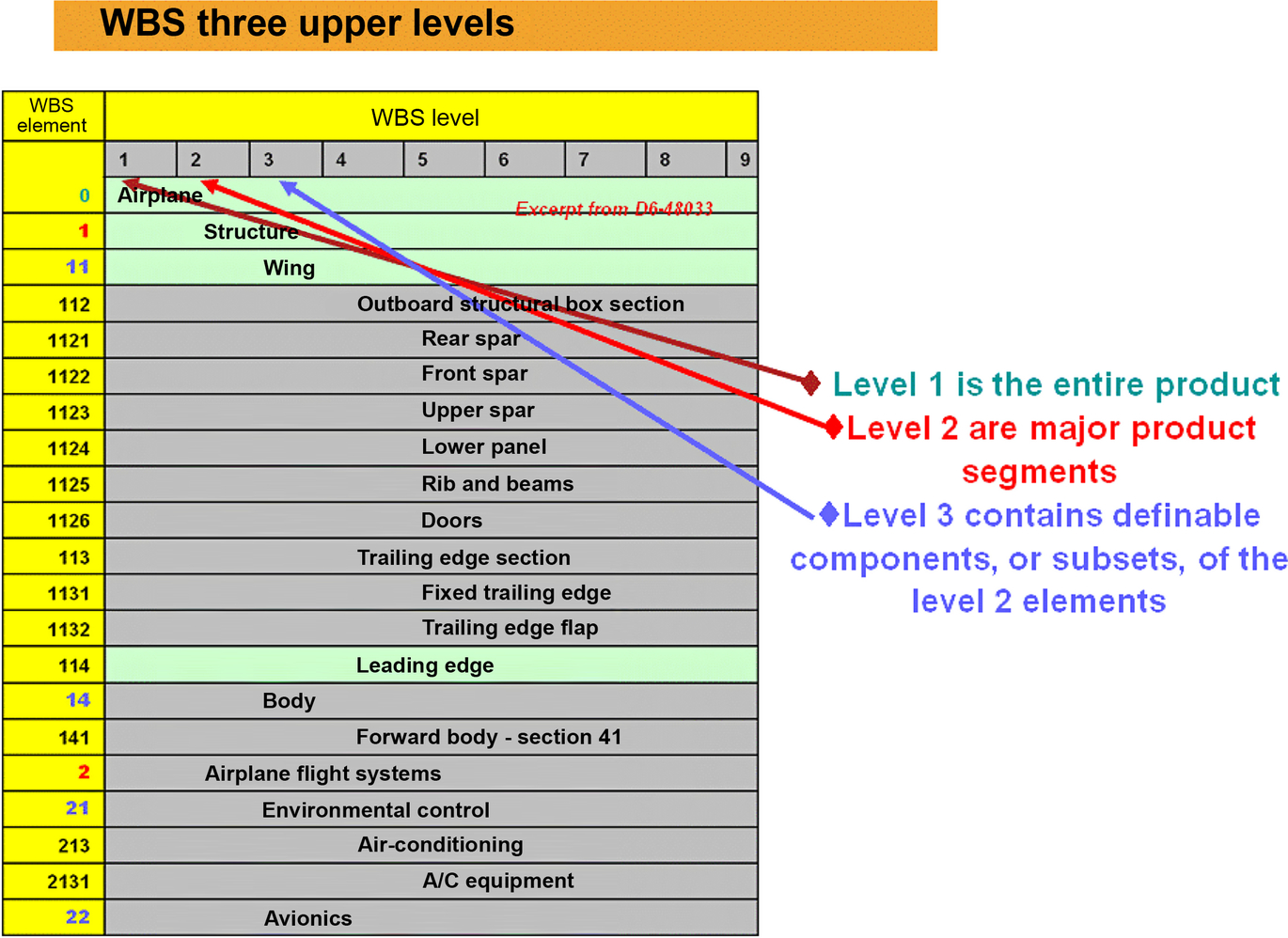
Fig. 3.1.1 shows the Work Breakdown Structure (WBS) of the first three levels of the project. Level 1 is the entire product, Level 2 is a major product part, and Level 3 contains the definable components or subsets of Level 2 elements.
Fig. 3.1.2 shows an example of a project WBS in the Microsoft Word indented format. Four levels are defined here as examples.
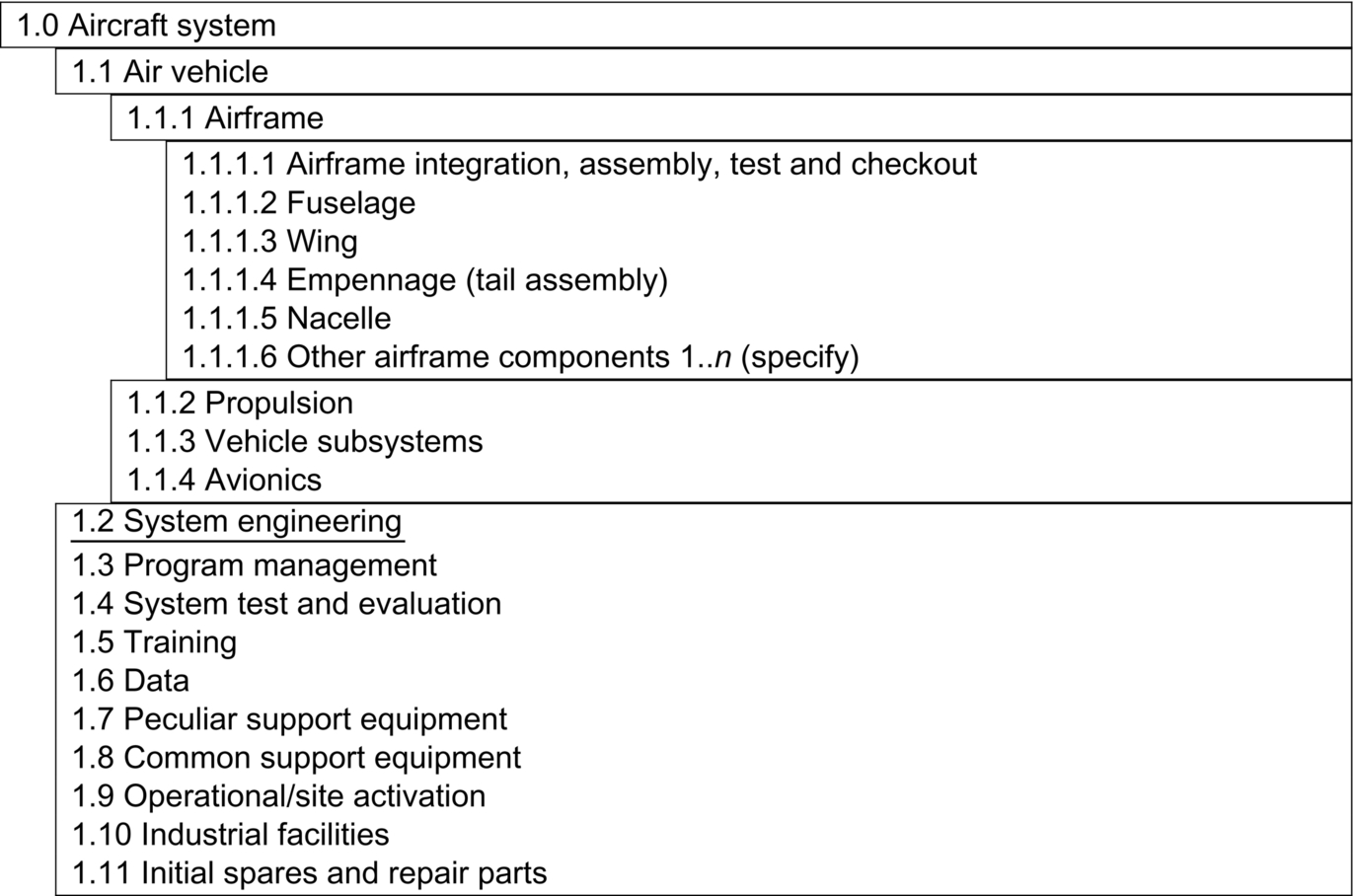
Project planning also includes a project schedule, with the purpose of planning and communicating when project activities can or must occur. A common tool for project scheduling is the Gantt chart. Microsoft Project is another popular tool used to manage a project schedule for planning purposes. See Figs. 3.1.3–3.1.5 for examples of project schedules at Level 1, Level 2, and Level 3, respectively.
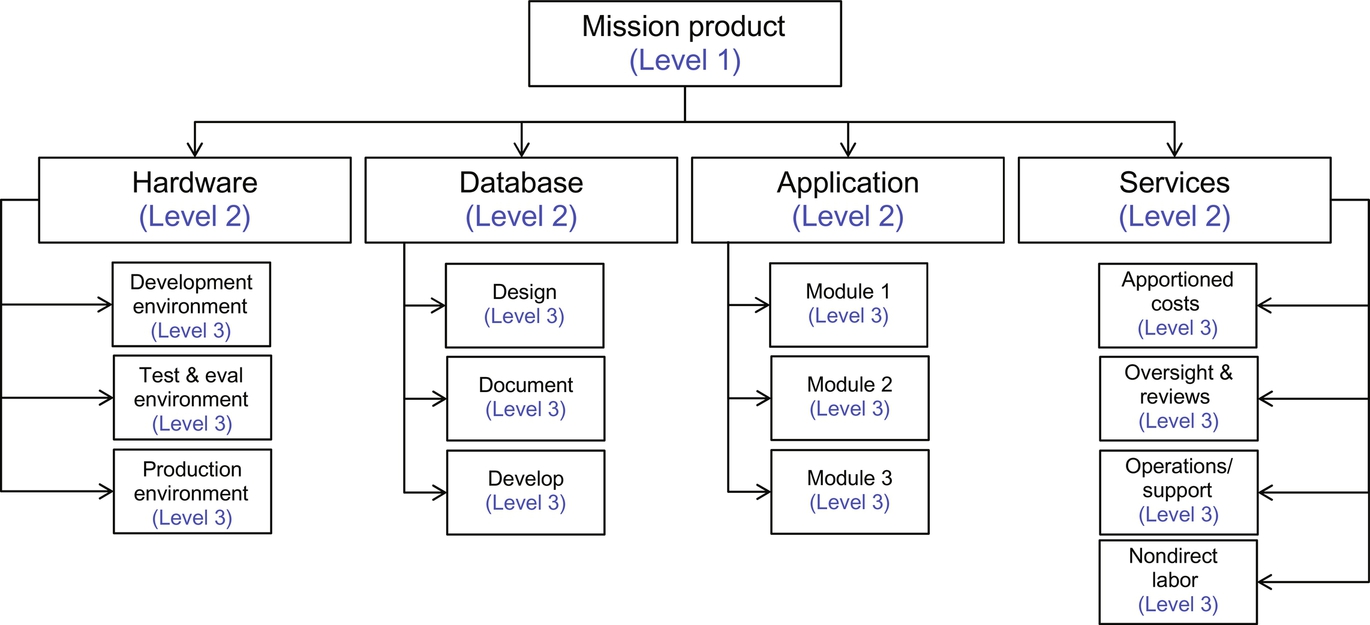
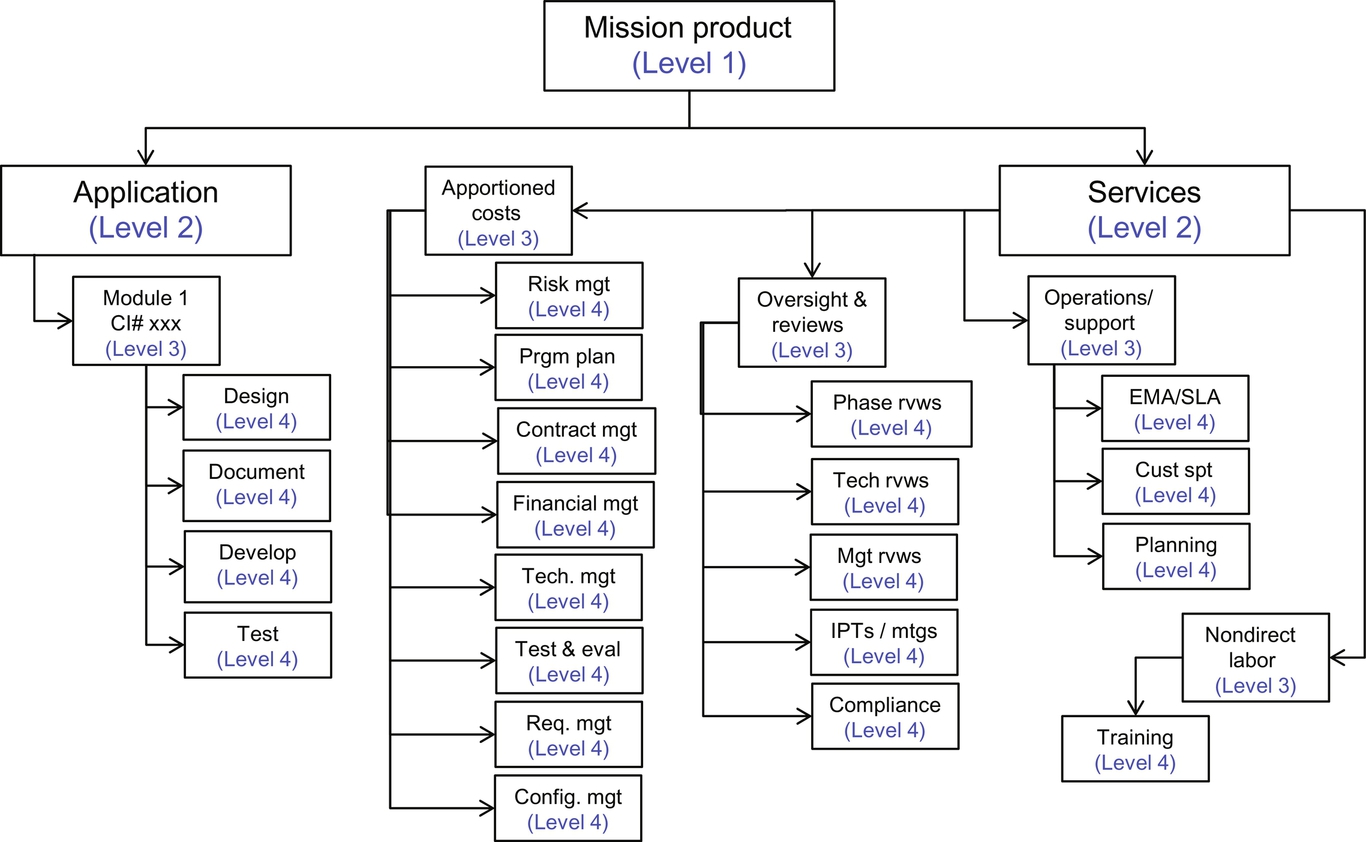
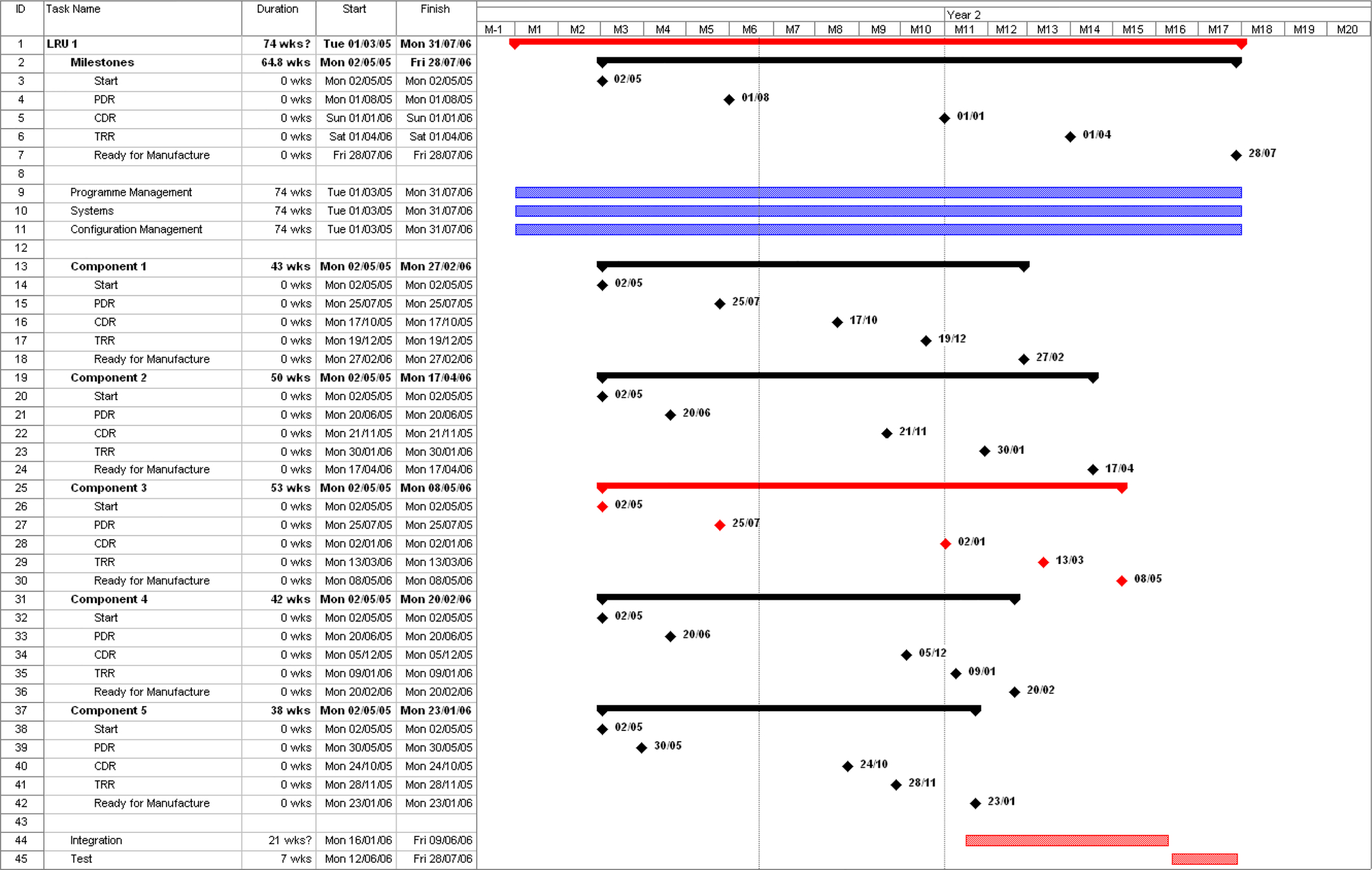
Fig. 3.1.6 shows project planning within the project lifecycle, from the concept phase to the definition phase to the execution phase.
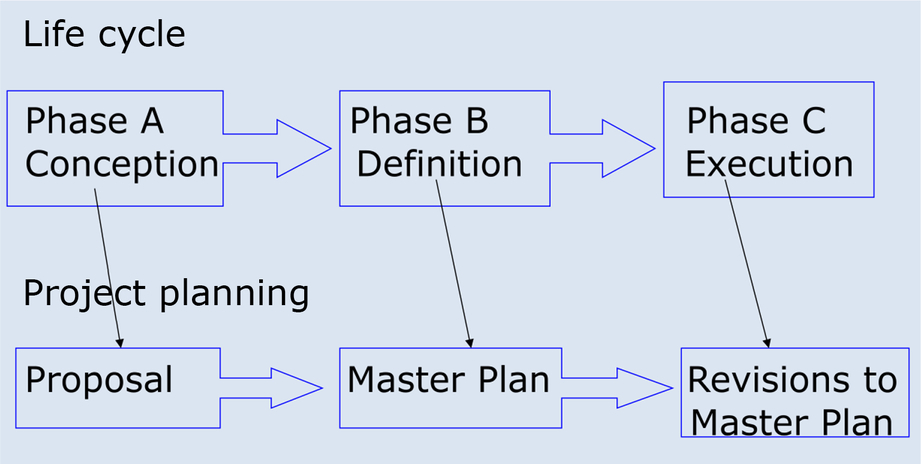
Project planning is an essential part of the project lifecycle (Fig. 3.1.7). Topics that should appear in the Team Plan are as follows:
- 1. Scope, Statement of Work (SOW), Charter
- • Objectives, user/system requirements
- 2. Work definition
- • WBS, work packages, required resources
- 3. Project organization
- • Expertise/skills, responsibilities
- 4. Project schedule
- • Timeline, milestones
- 5. Project budget
- • Breakdown by work packages/resources
- 6. Review and control
- • Work review/QA, assessment/approvals, change control, risk monitoring
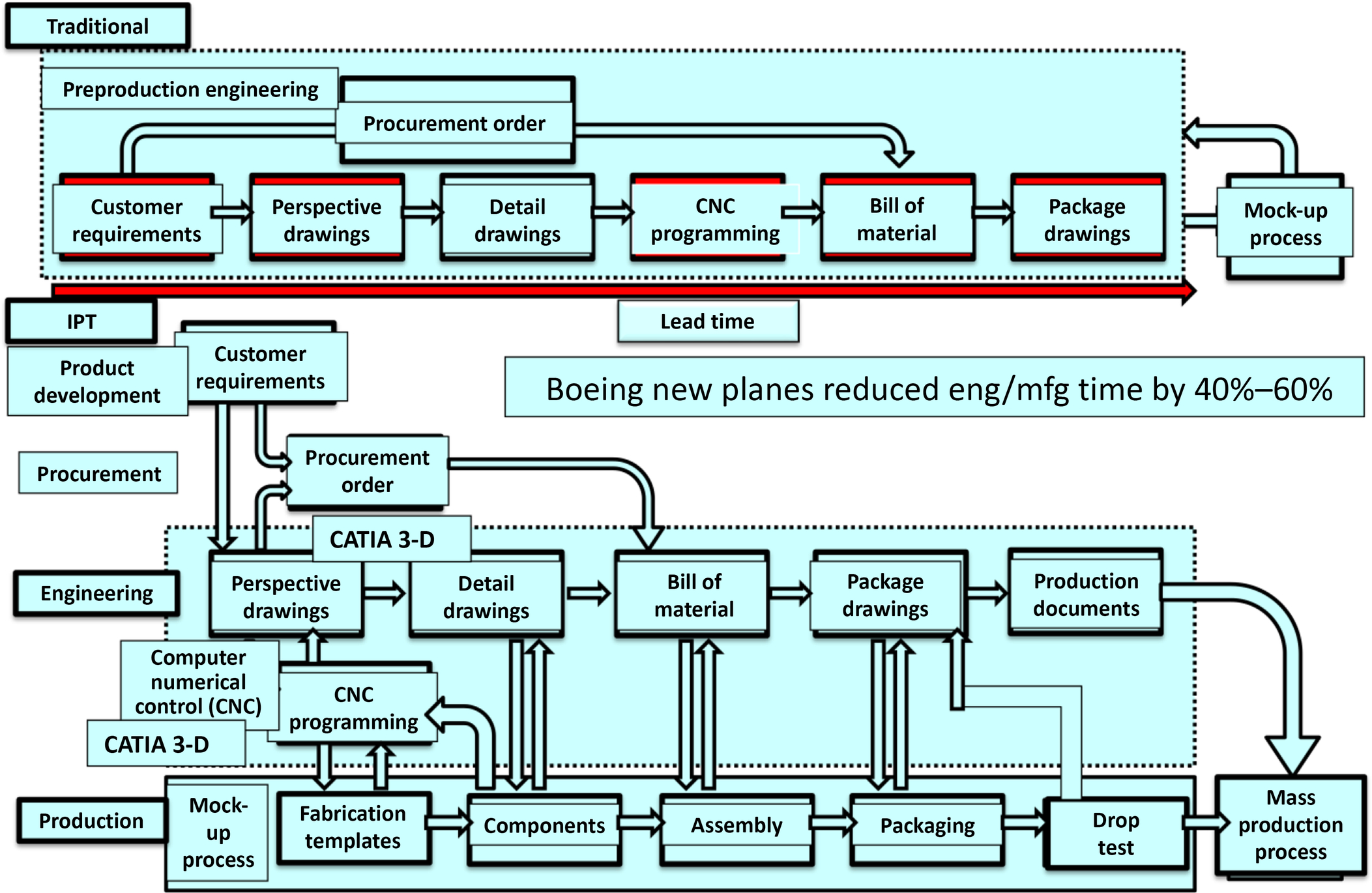
Fig. 3.1.8 shows the core team members and part-time members of the Integrated Product Team (IPT).
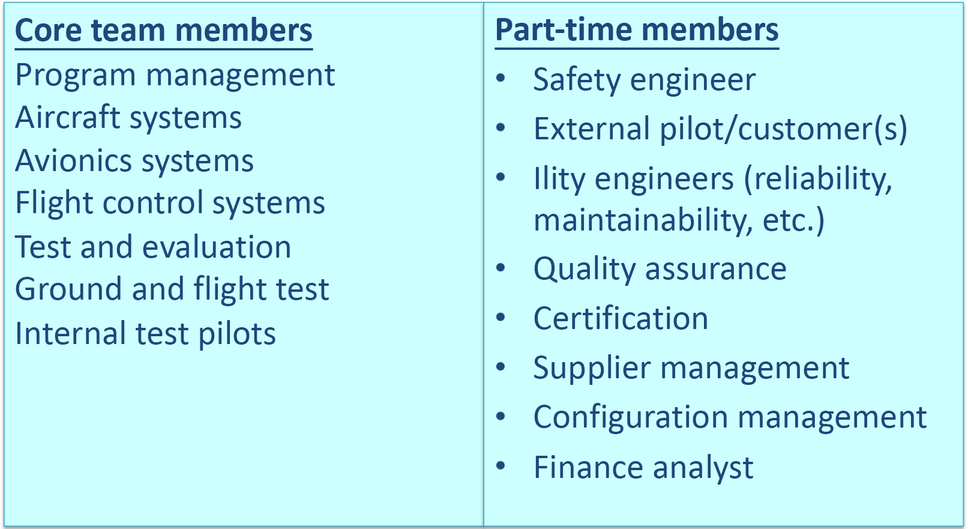
An IPT/team-based approach was a streamlined, integrated, concurrent approach to designing products and processes. The unique strength of this IPT approach was speed to market. Furthermore, the product teams that adopted this approach became more responsive to the needs of the customers. These qualities were essential to total customer satisfaction.
Traditional product development lacked of up-front communications among affected functional disciplines. The functional approach to design and project activity often led to disjointed interfaces and product launch delays. Because of this inefficient traditional approach, personnel had to resolve conflicts after they received their work assignments, a situation that led to lower quality, increased overall costs, and poor performance impacting the program schedule.
Successful implementation of the IPT approach called for policy definition, resources, training, and team formation. IPT leaders must have empowered staff members to participate in decision making and to form self-managed work teams that took responsibility for managerial duties, such as scheduling, training, hiring, and discipline. The team defined the integrated master schedule and negotiated the handoff points for each functional discipline. One outcome of a successful implementation of the IPT approach was increased awareness of what other teammates do functionally and of their requirements. This awareness resulted in an increase in meaningful, cross-functional communication.
Design changes were costly, and the later the changes, the more costly their implementation. The traditional sequential product development process versus the team-based approach is shown in Fig. 3.1.9. The overlapped concurrent segments in Figure 3.1.9 represent the time savings in the various program phases. Speed to market stretched the stream of income before technological obsolescence caught up. An IPT approach created opportunities in market share, market leadership, and profits. Teammates who regularly saw one another communicated best; therefore, to maximize communication and minimize design changes, locating each project’s team members near each other was critical to success of a product team.
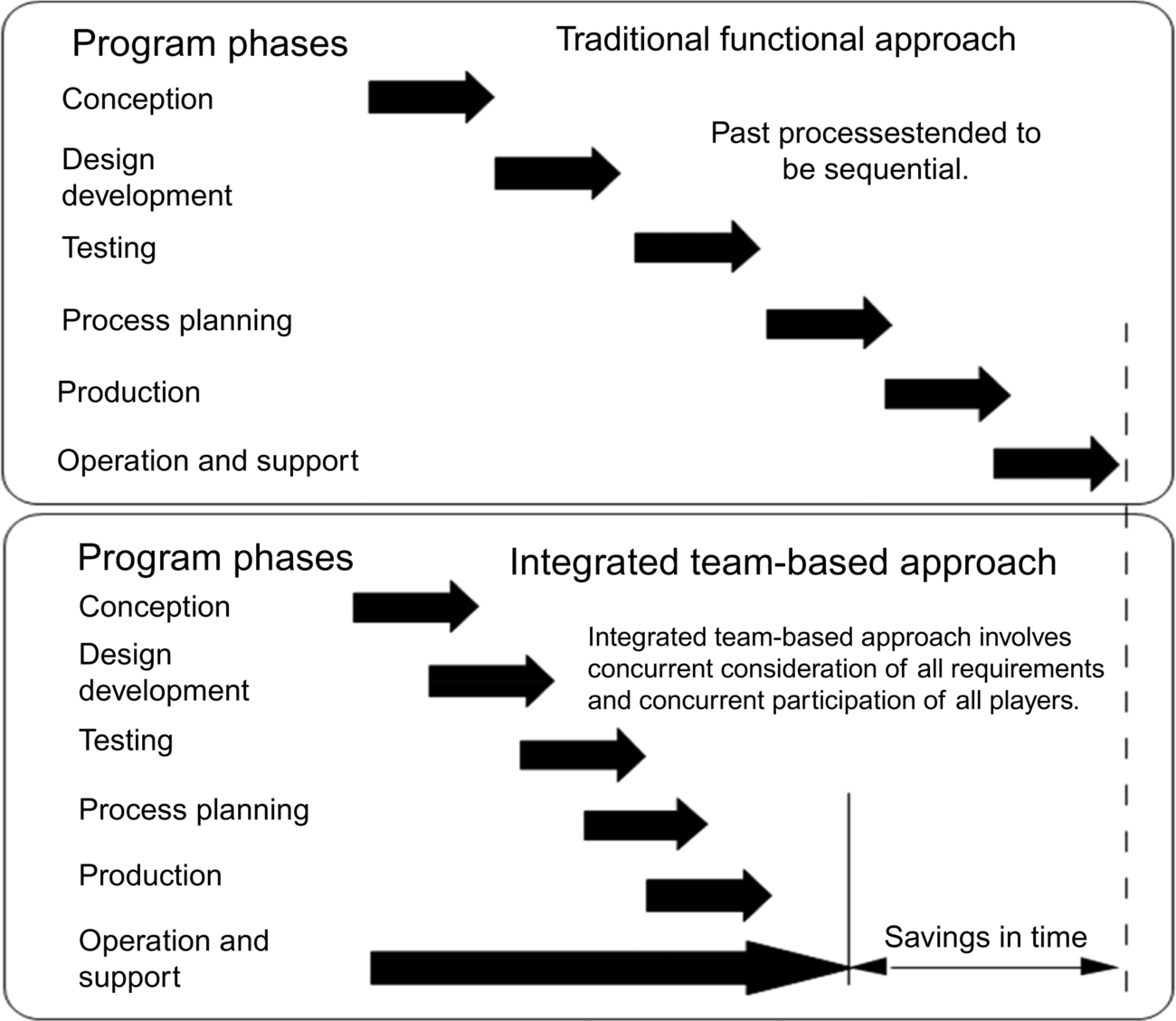
Moving a product to market quickly gives any company a competitive advantage. Compared to the integrated product team approach, the traditional, sequential product development process was expensive and took too long to complete.
Fig. 3.1.10 shows the ten-step planning and execution process of the IPT and its deliverables.
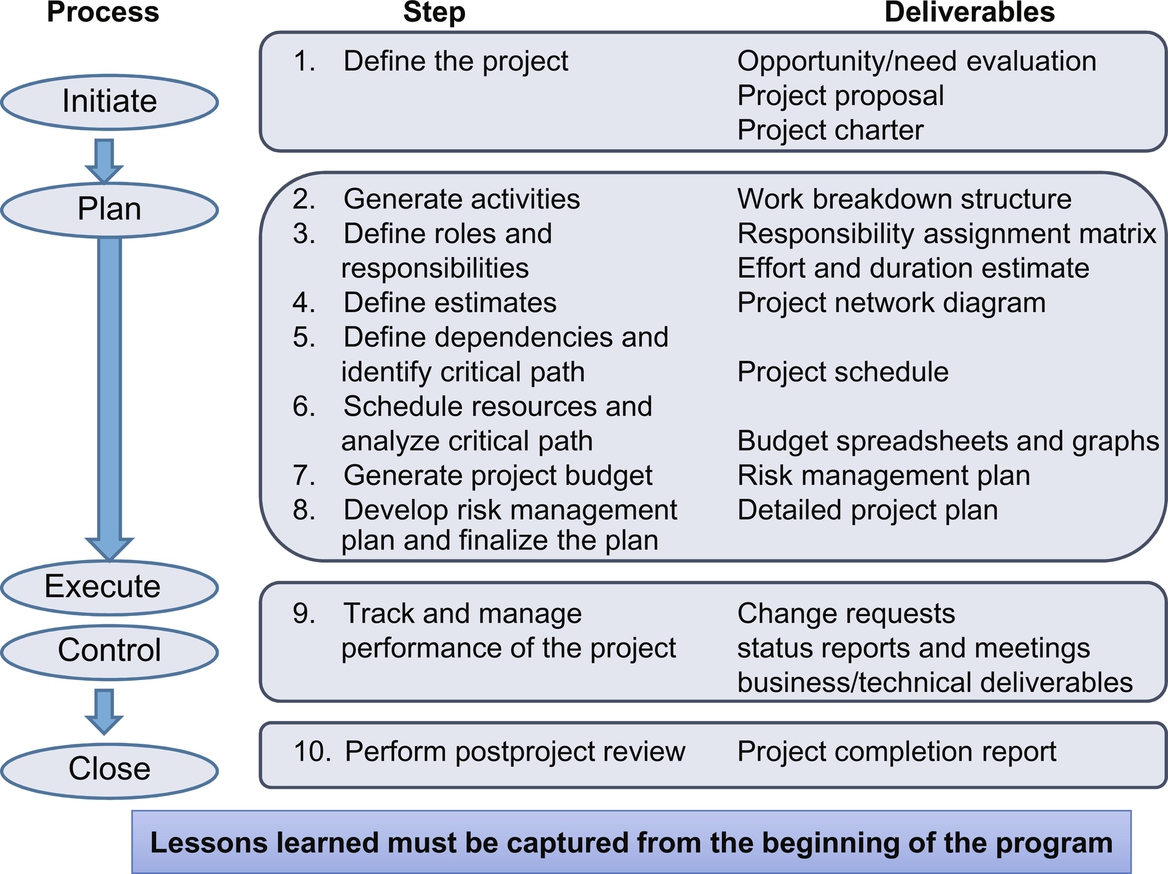
Traditional airplane design solution factors considered are drag, weight, noise, schedule reliability, development cost, and build cost. The additional factors considered are maintenance cost and airplane availability.
Research shows that influence on lifecycle costs for an airplane are:
- 1. Design received only 5% of the total resource allocation, but design’s influence on downstream costs was determined to be 70%!
- 2. Material: 50%; influences of: 20%
- 3. Labor: 15%; influences of: 5%
- 4. Overhead: 30%; influences of: 5%
Design resources are the highest leveraged resource in aircraft manufacturing. Therefore, fewer design changes will definitely influence lifecycle costs for an airplane.
Leave a Reply