This process was originally practiced by artisans in the 16th century forming the object in wax by hand. The wax object or pattern was then covered by a plaster investment (Figure 20.25). When this plaster became hard, the mould was heated in an oven, melting the wax and at the same time further drying hardening the mould. Here the pattern used is not removed from the mould but is replaced by molten metal in making the casting. Wax is removed by vaporization. In place of wax thermosetting plastics may be used. Due to high dimensional accuracy it is also known as precision casting.
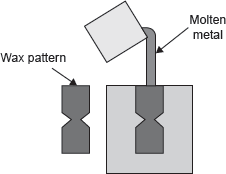
Figure 20.25 Lost-wax Precision Casting
- Intricate forms having undercuts can be cast easily.
- A very smooth surface on casting is obtained with no parting line.
- Dimensional accuracy is very good.
- Certain unmachinable parts can be cast.
- It may be used to replace die casting where shortruns are involved.
Disadvantages
- This casting process is expensive and limited to small casting.
Leave a Reply