A life cycle inventory (LCI) quantifies energy and raw material requirements, atmospheric emissions, waterborne emissions, solid wastes, and other releases for the entire life cycle of a product, process, or activity (USEPA 1993). Such an inventory is in the form of a list of the quantities of pollutants released to the environment and the amounts of energy and materials consumed. The results can be segregated by life cycle stage, by media (air, water, land), by specific processes, or any combination thereof.
Without an LCI, no basis exists to evaluate comparative environmental impacts or potential improvements. The level of accuracy and detail of the data collected is reflected throughout the remainder of the LCA process. LCI analyses can be used by industry for comparing products, processes, and materials. Government policy makers, too, can use LCI analyses in the development of regulations targeting resource use and environmental emissions.
The USEPA published two guidance documents, Life‐Cycle Assessment: Inventory Guidelines and Principles (USEPA 1993) and Guidelines for Assessing the Quality of Life‐Cycle Inventory Analysis (USEPA 1995). These federal guidelines provide the framework for performing an inventory analysis and assessing the quality of the data used and the results. The two documents define the following steps of an LCI:
- Develop a flow diagram of the processes being evaluated
- Develop a data collection plan
- Collect data
- Evaluate and report results
Develop a Flow Diagram
A flow diagram is a tool to map the inputs and outputs to a process or system. The system boundary varies for the LCA, as established in the goal definition and scoping phase and expanded to include process inputs and outputs serves as the system boundary for the flow diagram. Unit processes inside the system boundary link together to form a complete life cycle picture of the required inputs and outputs (material and energy) to the system. Figure 6.4 illustrates the components of a generic unit process within a flow diagram for a given system boundary. The more complex the flow diagram, the greater the accuracy and utility of the results. Unfortunately, increased complexity also means more time and resources must be devoted to this step, as well as the data collecting and analyzing steps.
Flow diagrams are used to model all alternatives under consideration (e.g. both a baseline system and alternative systems). For a comparative study, it is important that both the baseline and alternatives use the same system boundary and are modeled to the same level of detail. If not, the accuracy of the results may be skewed.
Develop an LCI Data Collection Plan
An LCI data collection plan ensures that the quality and accuracy of data, characterized as part of the goal definition and scoping phase, meet the expectations of the decision‐makers.
Key elements of a data collection plan include the following:
- Defining data quality goals
- Identifying data sources and types
- Identifying data quality indicators
- Developing a data collection worksheet and checklist
Define data quality goals – Data quality goals provide a framework for balancing available time and resources against the quality of the data required to make a decision regarding overall environmental or human health impact (USEPA 1989a). Data quality goals, which are closely linked to overall study goals, both aid LCA practitioners in structuring an appropriate approach to data collection and serve as data quality performance criteria.
Although the number and nature of data quality goals necessarily depend on the level of accuracy required for a given LCA, the following list of hypothetical data quality goals is typical. Site‐specific data are required for raw materials and energy inputs, water consumption, air emissions, water effluents, and solid waste generation. Approximate data values are adequate for the energy data category. Air emission data should be representative of similar sites in the United States. A minimum of 95% of the material and energy inputs should be accounted for in the LCI.
Identify data quality indicators – Data quality indicators are benchmarks against which the collected data can be measured to determine if data quality requirements have been met. Selection depends on which of the available indicators are most appropriate and applicable to the specific data sources being evaluated. Examples of indicators are precision, completeness, representativeness, consistency, and reproducibility.
Identify data sources and types – For each life cycle stage, unit process, or type of environmental release, the data source and/or type that will provide sufficient accuracy and quality to meet the study’s goal is specified. Doing this prior to data collection helps to reduce costs and the time required to collect the data. Data sources include
- meter readings from equipment operating logs or journals; industry data reports, databases, or consultant’s laboratory test results; government documents, reports, and databases; other publicly available databases or clearinghouses; journals, and papers, books; reference books; patents; and trade associations. Related LCI studies are also useful, as are equipment and process specifications best engineering judgment.
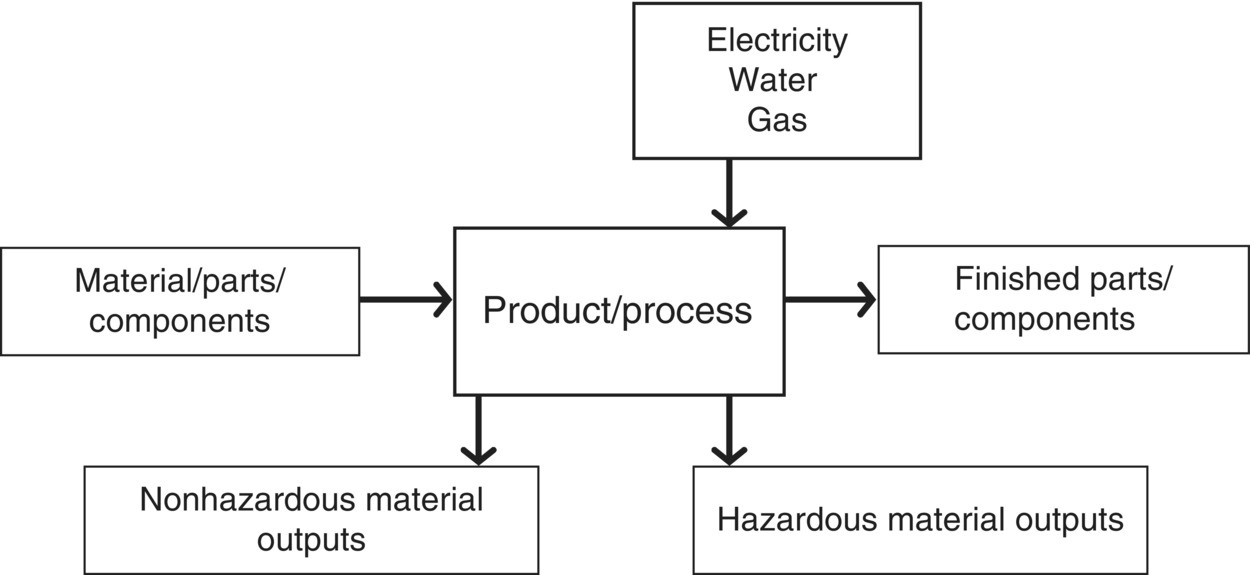
Examples of data types include full measured, modeled, and sampled data; non site‐specific (i.e. surrogate) data; non‐LCI data (i.e. not intended for use in an LCI); and vendor data.
The required level of aggregated data should also be specified. For example, the reader should be able to ascertain quickly whether data are representative of one process or several processes.
Develop a data collection worksheet and checklist – The LCI checklist should cover most of the decision areas in the performance of an inventory. This document can be prepared to guide data collection and validation and can enable construction of a database to store collected data electronically. The following general decision areas should be addressed on the inventory checklist:
- purpose of the inventory
- system boundaries
- geographic scope
- types of data used
- data collection procedures
- data quality measures
- computational model construction
- presentation of results
All inputs and outputs for each process modeled in the flow diagram should be recorded on an accompanying data worksheet.
The checklist and worksheet are valuable tools for ensuring completeness, accuracy, and consistency. They are especially important for large projects when several people collect data from multiple sources. The checklist and worksheet should be tailored to meet the needs of a specific LCI.
Collect Data
The flow diagram(s) developed in step 1 provides the road map for data to be collected. Step 2 specifies the required data sources, types, quality, accuracy, and collection methods. Step 3 consists of finding and filling in the flow diagram and worksheets with numerical data. This may not be a simple task. If some data are difficult or impossible to obtain, and available data are difficult to convert to the appropriate functional unit; therefore, the system boundaries or data quality goals of the study will have to be refined to describe the results that can reliably be obtained from the data available. This iterative process is common for most LCAs.
Data collection efforts involve a combination of research, site‐visits, and direct contact with experts which generate large quantities of data. An electronic database or spreadsheet can be useful to hold and manipulate the data. Alternatively, it may be more cost effective to buy a commercially available LCA software package (see Section 6.3). Prior to purchasing an LCA software package the decision‐makers or LCA practitioner should insure that it will provide the level of data analysis required.
A second method to reduce data collection time and resources is to obtain non‐site specific inventory data. Several organizations have developed databases specifically for LCA that contain some of the basic data commonly needed in constructing an LCI. Some of the databases are sold in conjunction with LCI data collection software; others are stand‐alone resources. Many companies with proprietary software also offer consulting services for LCA design.
Evaluate and Document the LCI Results
When the data have been collected and organized, the accuracy of the results must be verified. In documenting the results of the LCI, it is important to thoroughly describe the methodology used in the analysis, define the systems analyzed and the boundaries that were set, and state all assumptions made in performing the inventory analysis. Use of the checklist and worksheet (see step 2) supports a clear process for documenting this information. The outcome of the inventory analysis is a list containing the quantities of pollutants released to the environment and the amount of energy and materials consumed. The information can be organized by life cycle stage, by media (air, water, land), by specific process, or any combination thereof that is consistent with the ground rules.
If the sensitivity of the LCI data collection efforts has not been properly determined before the next stage, life cycle impact assessment (LCIA), is begun, the LCA itself may have to be repeated because the data are found to be insufficient to permit the drawing of the desired conclusions.
Leave a Reply