On a large scale, decontamination and inoculation must be done on a continuous basis and not batchwise as in a laboratory trial (Figure 6.9). To achieve this, the FPL investigators built a treatment system based on two screw conveyers that transport the chips and act as treatment chambers. Figure 6.9 is an overview of the continuous process equipment used in 5‐ and 50‐T trials. Steam is injected into the first screw conveyer, which heats and decontaminates the chip surface. A surge bin, located between the two conveyers, acts as a buffer. From the bottom of the surge bin, a second screw conveyer removes the chips, which are subsequently cooled with filtered air. In the second half of the second screw conveyer, the inoculum suspension containing fungus, unsterilized corn steep liquor, and water is applied and mixed with the chips through the tumbling action. From the screw conveyer, the chips fall into the pile or reactor for a two‐week incubation. In the first scale‐up trial, 5 T of spruce wood chips were inoculated and incubated at a throughput of approximately 0.5 T/h.
In successful outdoor trials with the biopulping fungus Ceriporiopsis subvermispora, nearly 50 T of spruce was treated at a throughput of about 2 T/h (dry weight basis) continuously for over 20 hours. During the two weeks, the chip pile was maintained within the temperature growth range for the fungus, despite the outdoor exposure to ambient conditions.
Economics and Environmental Benefits of the Biopulping Process
The economic benefits of biopulping, evaluated based on the process studies and engineering data, result from several effects. Energy reduction at the refiner was used as the primary criterion for the effectiveness of biopulping. For a two‐week process, the savings should be a minimum of 25% under the worst‐case conditions of wood species and minimal process control, whereas up to nearly 40% can be achieved under some circumstances. Additionally, mills that are currently throughput‐limited as a result of refiner capacity may achieve total capacity increases as a result of biopulping. The improved strength of the biomechanical pulps would allow the required strength of the blend to be achieved with a lower percentage of the kraft pulp in those cases where the pulps are blended. Finally, only benign materials are used, and no additional waste streams are generated. An economic analysis of the process yielded very favorable results. The analysis of a 200 T/day TMP mill are summarized here. Under different scenarios and assumptions for utility costs, equipment needs, and operating costs, the net savings can range from $10 to more than $26/T of pulp produced, with an estimated capital investment of $2.5 million. Mills that are refiner‐limited can experience throughput increases of over 30% from the reduction in refining energy by running the refiners to a constant total power load. Even a modest throughput increase of 10%, coupled with the energy savings of 30%, results in a payback in less than 1 year. This is equivalent to a savings of $34/T at a 15% rate of return on capital. Furthermore, many mills blend mechanical pulps and kraft pulps to achieve the optical and strength properties desired. Additional benefits of over $10/T can be realized when the anticipated stronger biopulped TMP is partially substituted for kraft at a 5% rate. The results of a 600 T/day analysis have also been published (Scott et al. 1998a, b). This preliminary analysis is subject to appropriate qualifications. The capital costs are subject to some variability, in particular the costs associated with integrating the new facility into an existing site. The additional advantages of biopulping, including the environmental benefits and pitch reduction, have not been quantified in this report. Finally, much of this analysis is site‐specific, depending on the operating conditions at the particular mill considering incorporating biopulping into its operations.
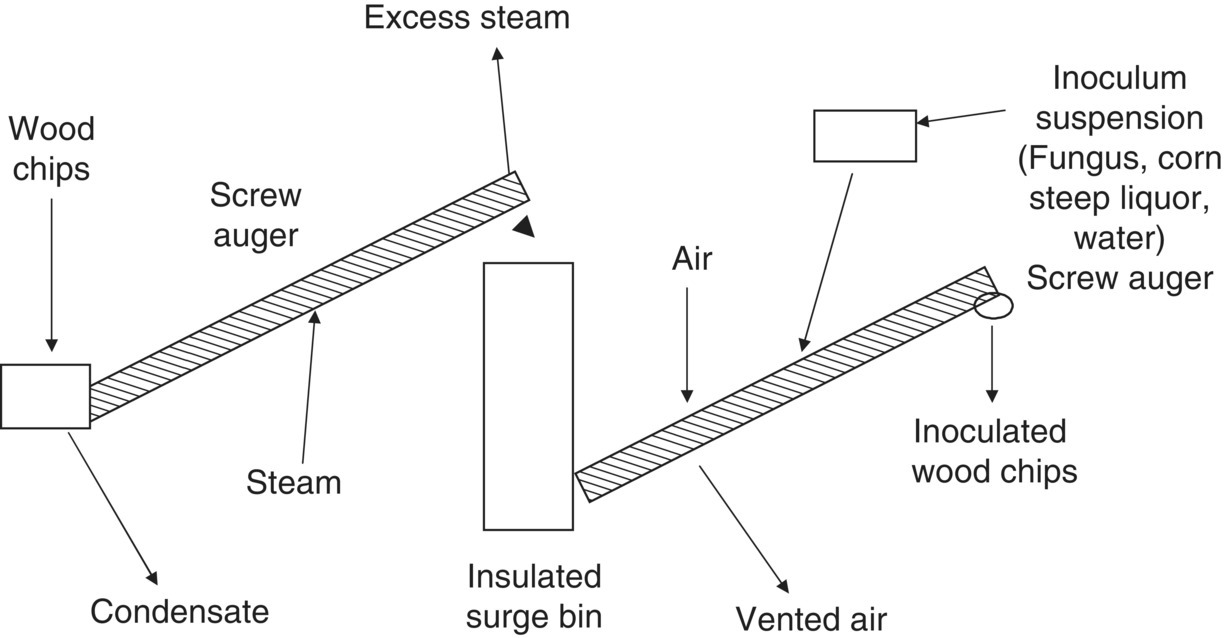
Although the environmental benefits of biopulping for mechanical pulping have not been quantitatively determined in an economic sense, we can discuss the benefits qualitatively. Sykes (1994) determined that there were no environmental problems with the effluent from a biopulping process. In terms of GHGs, there is a net benefit to the biopulping process. The process itself is oxidative, producing carbon dioxide as the fungus metabolizes the various wood components. However, based on the typical generation efficiency of electrical energy, the reduced energy requirements (~30%) significantly lower the overall generation of carbon dioxide when the entire system is analyzed. Finally, in terms of biological issues with using fungi in the wood yard, there are benefits to using the biopulping fungus. The biopulping fungus outcompetes the normal cohort of fungi and other organisms that will grow in an uncontrolled wood chip pile. Some of these other organisms, such as Aspergillis, can be detrimental to human health. The biopulping fungi are naturally occurring in the forests of the world and have no known health effects on humans. More information on benefit–cost analysis and economic input–output model (EIO‐LCA) for chemical process and manufacturing industries are available in Appendix F.
Leave a Reply