Aluminium has been an important aerospace structural material in the development of weight-efficient airframes for aircraft since the 1930s. The development of aircraft capable of flying at high speeds and high altitudes would have been difficult without the use of high-strength aluminium alloys in major airframe components such as the fuselage and wings. Compared with other major aerospace materials, such as magnesium, titanium, steel and fibre-reinforced polymer composite, aluminium is used in greater quantities in the majority of aircraft. Aluminium accounts for 60–80% of the airframe weight of most modern aircraft, helicopters and space vehicles. Aluminium is likely to remain an important structural material despite the growing use of composites in large passenger airliners such as the Airbus 380 and 350XWB and the Boeing 787. Around 400 000 tonne of aluminium is used each year in building military and civil aircraft. Many types of airliners continue to be constructed mostly of aluminium, including aircraft built in large numbers such as the Boeing 737, 747 and 757 and the Airbus A320 and A340. Competition between aluminium and composite as the dominant structural material is likely to intensify over the coming years, although aluminium remains central to weight-efficient airframe construction.
Figure 8.1 shows examples of the present day use of aluminium alloys in passenger and military aircraft: the Boeing 747 and Hornet F/A-18. The weight percentages of structural materials used in the Boeing 747 is typical of passenger aircraft built between 1960 and 2000. Most of the airframe is constructed using high-strength aluminium alloys, and only small percentages of other metals and composites are used. Aluminium is used in the main structural sections of the B747, including the wings, fuselage and empennage. The only major components not built almost entirely from aluminium are the landing gear (which is made using high-strength steel and titanium) and turbine engines (which are made using various heat-resistant materials including nickel-based superalloys and titanium).
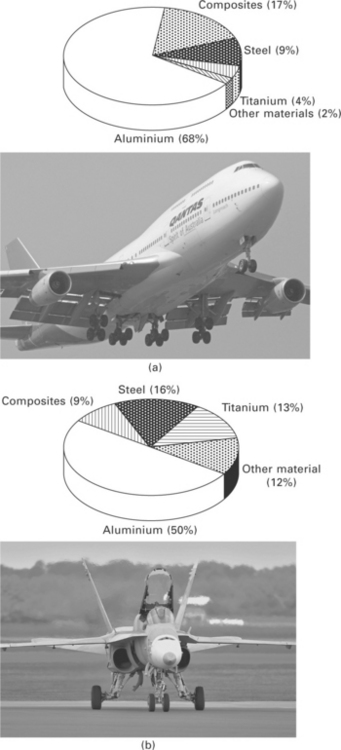
8.1 Use of aluminium alloys and other structural materials in (a) the Boeing 747 and (b) Hornet F/A-18. (a) Photograph supplied courtesy of M. Tian. (b) Photograph supplied courtesy of M. Nowicki.
The amount of aluminium alloy used in modern fighters varies considerably between aircraft types, although many are built almost entirely using aluminium. In general, the percentage of the airframe made using aluminium is lower for military attack aircraft than for civil aircraft. The airframe of most modern military aircraft consists of 40–60% aluminium, which is less than the 60–80% used in commercial airliners. The Hornet is typical of military aircraft built over the past thirty years in that aluminium is the most common structural material.
Aluminium is a popular aerospace structural material for many important reasons, including:
ease of fabrication, including casting, forging and heat-treatment;
light weight (density of only 2.7 g cm−3);
high specific stiffness and specific strength;
ductility, fracture toughness and fatigue resistance; and
good control of properties by mechanical and thermal treatments.
As with any other aerospace material, there are several disadvantages of using aluminium alloys in aircraft structures including:
low mechanical properties at elevated temperature (softening occurs above ~ 150 °C);
susceptibility to stress corrosion cracking;
corrosion when in contact with carbon-fibre composites; and
age-hardenable alloys cannot be easily welded.
The describes aluminium alloys, with special attention given to those alloys that are used in aircraft, helicopters, spacecraft and other aerial vehicles. The following aspects of aluminium alloys are covered: the benefits and problems of using aluminium alloys in aircraft; the different grades of aluminium alloys and the types used in aircraft; and engineering properties of aerospace aluminium alloys and their heat treatment.
Leave a Reply