Benjamin Franklin
Benjamin Franklin (Figure 8.8) contributed greatly to waste reduction thinking. Most of the basic goals of lean manufacturing and waste reduction were derived from Benjamin Franklin through documented examples. Poor Richard’s Almanac says of wasted time, “He that idly loses 5s. worth of time, loses 5s., and might as prudently throw 5s. into the river.” He added that avoiding unnecessary costs could be more profitable than increasing sales: “A penny saved is two pence clear. A pin a‐day is a groat a‐year. Save and have.”
Again Franklin’s The Way to Wealth says the following about carrying unnecessary inventory. “You call them goods; but, if you do not take care, they will prove evils to some of you. You expect they will be sold cheap, and, perhaps, they may [be bought] for less than they cost; but, if you have no occasion for them, they must be dear to you. Remember what Poor Richard says, ‘Buy what thou hast no need of, and ere long thou shalt sell thy necessaries’. In another place he says, ‘Many have been ruined by buying good penny worth’.” Henry Ford cited Franklin as a major influence on his own business practices, which included JIT manufacturing.
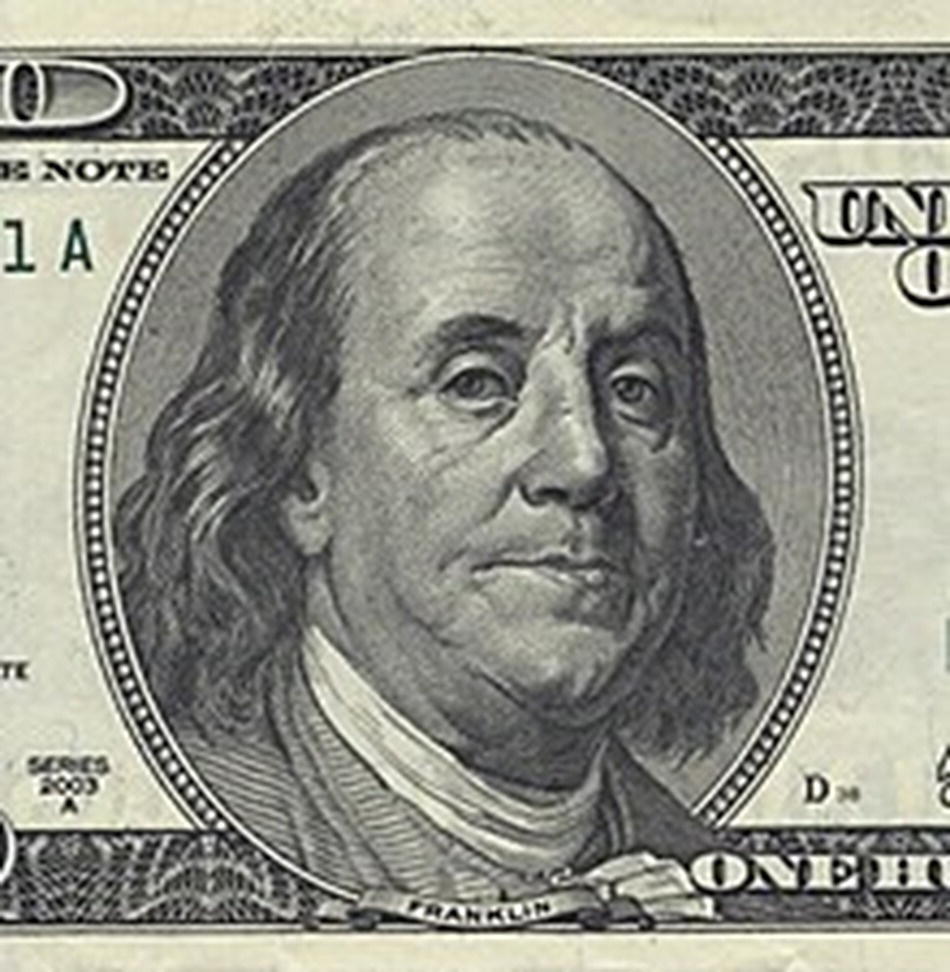
The accumulation of waste and energy within the work environment was noticed by motion efficiency expert Frank Gilbreth, who witnessed the inefficient practices of masons who often bend over to gather bricks from the ground. The introduction of a non‐stooping scaffold, which delivered the bricks at waist level, allowed masons to work about three times as quickly, and with the least amount of effort.
William Boeing
William E. Boeing (Figure 8.9) was born in Detroit, Michigan on 1 October 1881. Boeing moved to the Pacific Northwest at Hoquiam, Washington, and purchased extensive timberlands around Grays Harbor on the Pacific (west) side of the Olympic Peninsula and also bought into lumber operations. He made a success of the venture, in part by shipping lumber to the East Coast via the new Panama Canal, generating funds that he would later apply to a very different business. William Boeing left Yale University in 1903 to take advantage of opportunities in the risky and cyclical, but financially rewarding, Northwest timber industry. That experience would serve him well in aviation.
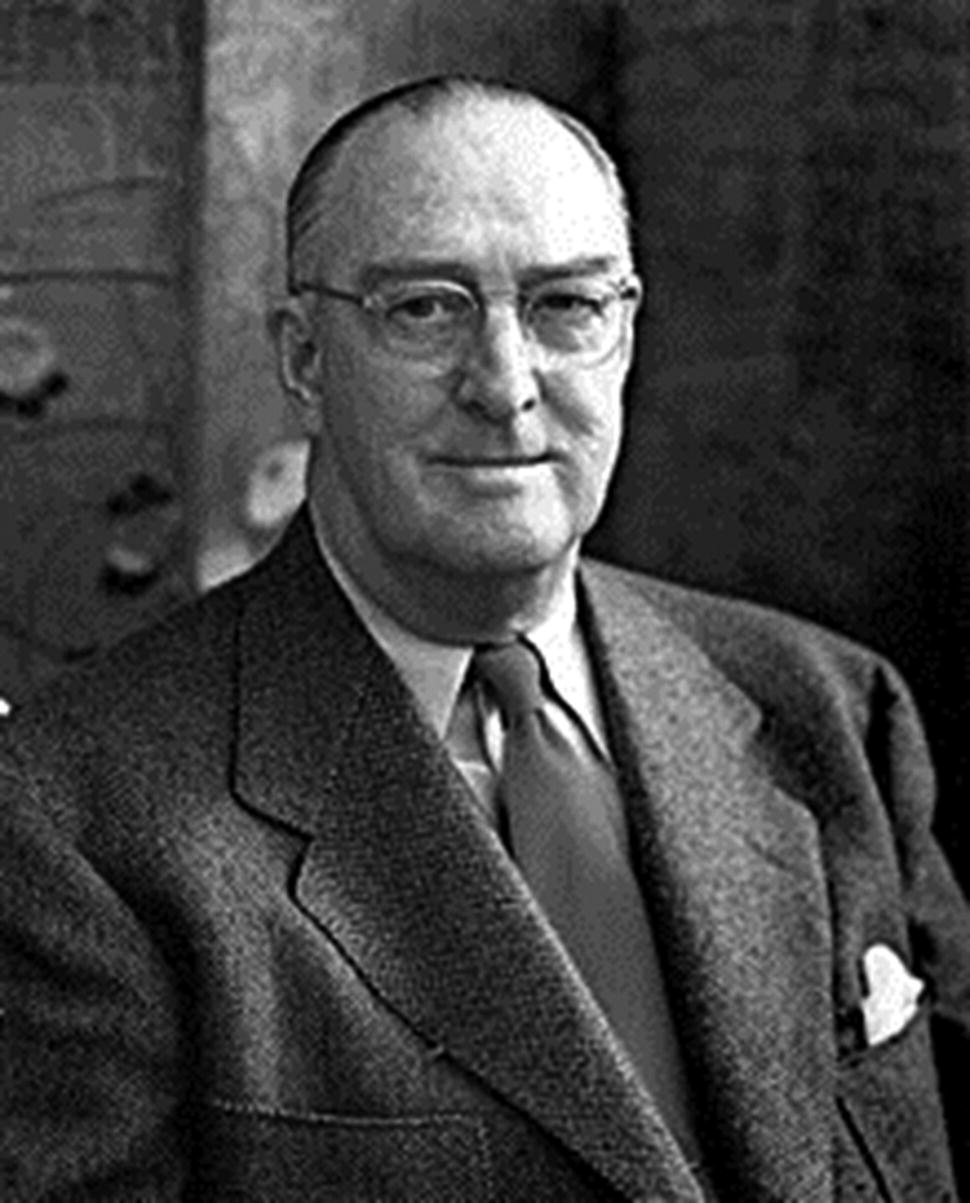
In 1916, Boeing went into business with George Westervelt as “B & W” and founded the Pacific Aero Products Co. The company’s first plane was the Boeing Model 1 (B & W Seaplane). When America entered the First World War on 8 April 1917, a little more than a month later, Boeing changed the name from Pacific Aero Products Co. to Boeing Airplane Company and obtained orders from the US Navy for 50 planes. At the end of the War, Boeing began to concentrate on commercial aircraft. He secured contracts to supply airmail service and built a successful airmail operation and later passenger service that evolved into United Airlines.
Under his guidance, a tiny airplane‐manufacturing company grew into a huge corporation of related industries. When post‐Depression legislation in 1934 mandated the dispersion of the corporation, Boeing sold his interests in the Boeing Airplane Co., but he continued to work on other business ventures.
He became one of America’s most successful breeders of thoroughbred horses. He never lost his interest in aviation, and during World War II he volunteered as a consultant to the company. He lived until 1956, long enough to see the company he started enter the jet age.
William E. Boeing was a private person, a visionary, a perfectionist, and a stickler for the facts. The wall of his outer office bore a placard that reads: “2329 Hippocrates said: 1. There is no authority except facts. 2. Facts are obtained by accurate observation. 3. Deductions are to be made only from facts. 4. Experience has proved the truth of these rules.” According to his son, William Boeing, Jr., Boeing was a fast and avid reader and remembered everything he read. He was also a perfectionist. While visiting his airplane building shop at the Duwamish shipyard in 1916, Boeing saw a set of improperly sawed spruce ribs. He brushed them to the floor and walked all over them until they were broken. A frayed aileron cable caused him to remark, “I, for one, will close up shop rather than send out work of this kind.”
Frederick Winslow Taylor
Frederick Winslow Taylor (Figure 8.10), the father of scientific management, introduced what are now called standardization and best practice deployment. In Principles of Scientific Management (Taylor 1911), Taylor said: “And whenever a workman proposes an improvement, it should be the policy of the management to make a careful analysis of the new method, and if necessary conduct a series of experiments to determine accurately the relative merit of the new suggestion and of the old standard. And whenever the new method is found to be markedly superior to the old, it should be adopted as the standard for the whole establishment.”
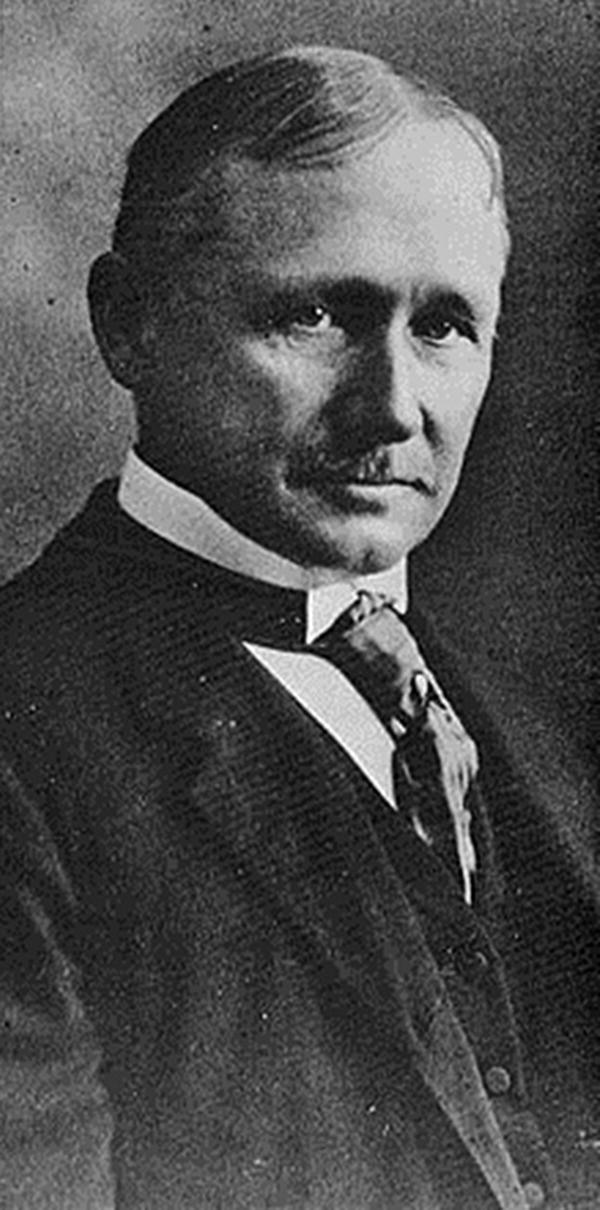
Taylor also warned explicitly against cutting piece rates (or, by implication, cutting wages or discharging workers) when efficiency improvements reduce the need for fresh labor: “. . .after a workman has had the price per piece of the work he is doing lowered two or three times as a result of his having worked harder and increased his output, he is likely entirely to lose sight of his employer’s side of the case and become imbued with a grim determination to have no more cuts if soldiering [marking time, just doing what he is told] can prevent it.”
Shigeo Shingo, the best‐known exponent of single minute exchange of die and error‐proofing or poka‐yoke, cites Principles of Scientific Management as his inspiration (Shigeo Shingo 1987). American industrialists recognized the threat of cheap offshore labor to American workers during the 1910s, and explicitly stated the goal of what is now called lean manufacturing as a countermeasure. Henry Towne, past President of the American Society of Mechanical Engineers, wrote in the Foreword to Frederick Winslow Taylor’s Shop Management (1911): “We are justly proud of the high wage rates which prevail throughout our country, and jealous of any interference with them by the products of the cheaper labor of other countries.” To maintain this condition, to strengthen our control of home markets, and, above all, to broaden our opportunities in foreign markets where we must compete with the products of other industrial nations, we should welcome and encourage every influence tending to increase the efficiency of our productive processes.
Henry Ford
Henry Ford (Figure 8.11) initially ignored the impact of waste accumulation while developing his mass assembly manufacturing system. Charles Buxton Going wrote in 1915: “Ford’s success has startled the country, almost the world, financially, industrially, mechanically. It exhibits in higher degree than most persons would have thought possible the seemingly contradictory requirements of true efficiency, which are: constant increase of quality, great increase of pay to the workers, repeated reduction in cost to the consumer. And with these appears, as at once cause and effect, an absolutely incredible enlargement of output reaching something like one hundredfold in less than ten years, and an enormous profit to the manufacturer” (Arnold and Faurote 1915).
Ford, in My Life and Work (Ford and Crowther 1922), provided a single‐paragraph description that encompasses the entire concept of waste:
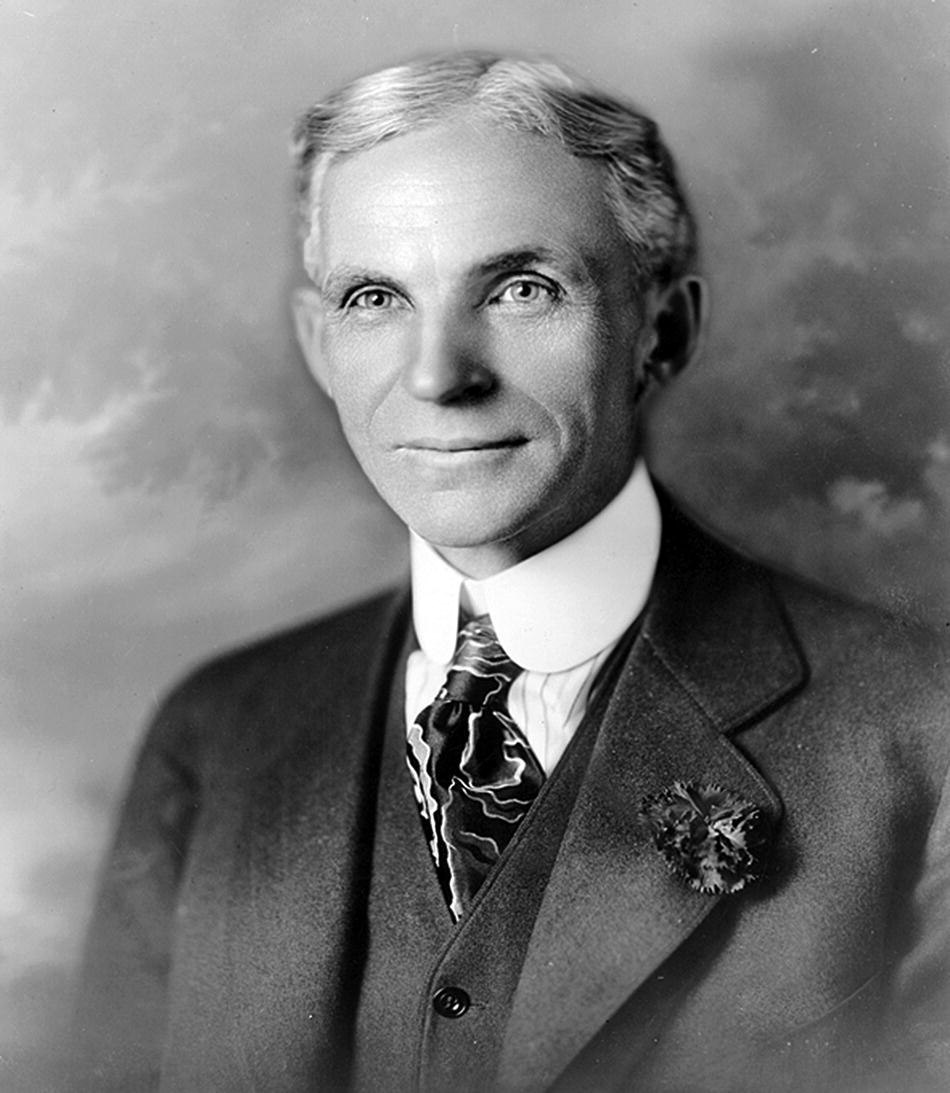
I believe that the average farmer puts to a really useful purpose only about 5% of the energy he expends. . . . Not only is everything done by hand, but seldom is a thought given to a logical arrangement. A farmer doing his chores will walk up and down a rickety ladder a dozen times. He will carry water for years instead of putting in a few lengths of pipe. His whole idea, when there is extra work to do, is to hire extra men. He thinks of putting money into improvements as an expense. . . . It is waste motion—waste effort—that makes farm prices high and profits low.
Poor arrangement of the workplace – a major focus of the modern kaizen – and doing a job inefficiently out of habit – are major forms of waste even in modern workplaces.
Ford also pointed out how easy it was to overlook material waste. A former employee, Harry Bennett, wrote: “One day when Mr. Ford and I were together he spotted some rust in the slag that ballasted the right of way of the D. T. & I [railroad]. This slag had been dumped there from our own furnaces. ‘You know,’ Mr. Ford said to me, ‘there’s iron in that slag’. You make the crane crews who put it out there sort it over, and take it back to the plant” (Bennett and Marcus 1951).
In other words, Ford saw the rust and realized that the steel plant was not recovering all of the iron.
Ford’s early success, however, was not sustainable. As James Womack and Daniel Jones pointed out in “Lean Thinking,” what Ford accomplished represented the “special case” rather than a robust lean solution (Womack and Jones 2003). The major challenge that Ford faced was that his methods were built for a steady‐state environment, rather than for the dynamic conditions firms increasingly face today (Ruffa 2008). Although his rigid, top‐down controls made it possible to hold variation in work activities down to very low levels, his approach did not respond well to uncertain, dynamic business conditions; they responded particularly badly to the need for new product innovation. This was made clear by Ford’s precipitous decline when the company was forced to finally introduce a follow‐on to the Model T.
Design for manufacture (DFM) is a concept derived from Ford which emphasizes the importance of standardizing individual parts as well as eliminating redundant components in My Life and Work (Ford and Crowther 1922). This standardization was central to Ford’s concept of mass production, and the manufacturing “tolerances,” or upper and lower dimensional limits that ensured interchangeability of parts became widely applied across manufacturing. Decades later, the renowned Japanese quality guru, Genichi Taguchi, demonstrated that this “goal post” method of measuring was inadequate. He showed that “loss” in capabilities did not begin only after exceeding these tolerances, but increased as described by the Taguchi Loss Function at any condition exceeding the nominal condition. This became an important part of W. Edwards Deming’s quality movement of the 1980s, later helping to develop improved understanding of key areas of focus such as cycle time variation in improving manufacturing quality and efficiencies in aerospace and other industries.
While Ford is renowned for his production line, it is often not recognized how much effort he put into removing the fitters’ work to make the production line possible. Previous to the use, Ford’s car’s components were fitted and reshaped by a skilled engineer at the point of use, so that they would connect properly. By enforcing very strict specification and quality criteria on component manufacture, he eliminated this work almost entirely, reducing manufacturing effort by between 60 and 90% (Hounshell 1984). However, Ford’s mass production system failed to incorporate the notion of “pull production” and thus often suffered from overproduction.
Leave a Reply