The different view of single point cutting tool is shown in Figure 19.2. According to ASA (American Standard Association) there are seven parameters of tool geometry as mentioned below as
αb, αs, βe, βs, θe, θs, R
where αb is the back rake angle; αs, side rake angle; βe, end clearance angle; βs, side clearance angle; θe, end cutting edge angle; θs, side cutting edge angle; R, nose radius.
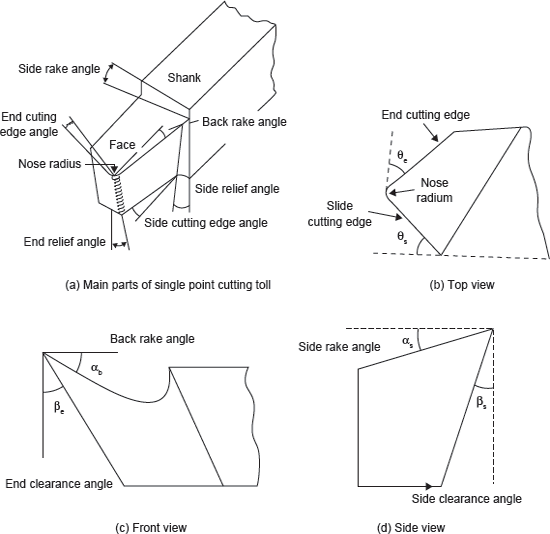
Figure 19.2 Nomenclature of Single Point Cutting Tool
Back Rake Angle and Side Rake Angle: Back rake angle is the angle between the face of the tool and a line parallel with base of the tool measured in a perpendicular plane through the side cutting edge. If the slope face is downward toward the nose, it is negative back rake angle and if it is upward toward nose, it is positive back rake angle. This angle helps in removing the chips away from the work piece. Generally, ceramic or brittle tool materials have negative back rake angle. It ranges from −5° to 15°.
Side rake angle is the angle between the base of the tool shank and the face of the tool measured in a plane perpendicular to the plane through the side cutting edge and right angle to the base. If the tool face is sloping upward towards the side cutting edge, side rake angle is positive and it is negative when it is sloping downward towards the side cutting edge. Positive side rake angle results in lower cutting force and low power consumption, and thus better cutting action. Negative side rake angle is used for rough cut and heavy duty applications. It ranges from −5° to 15°.
End Relief Angle and Side Relief Angle: The angle between the planes of the end flank immediately below the end cutting edge and line perpendicular to the base and right angle to the axis is known as end relief angle and the angle between the planes of the side flank immediately below the side cutting edge and line perpendicular to base along the axis is known as side relief angle. Relief angles are provided to ensure that no rubbing occurs between the work surface and flank surfaces of the tool. For general turning operations, they range from 5° to 15°.
End Cutting Edge Angle and Side Cutting Edge Angle: The angle between the plane along the end cutting edge and the plane perpendicular to the axis, both right angles to the base, is known as end cutting edge angle. End cutting edge angle provides a clearance to the trailing edge end of the cutting edge and machined surface to prevent the rubbing and drag action between them. Smaller value of end cutting edge angle generally uses less contact area with respect to the metal being cut. Larger end cutting edge angle results in vibration or chatter. It is limited to 5°.
The angle between the plane along the side cutting edge and the plane perpendicular to the axis, both right angles to the base, is known as side cutting edge angle. It prevents the shock of the cut at the tip of the tool. It can vary from 0° to 90°. On increasing the angle, thickness of the chip decreases but its width increases.
Nose Radius: The nose radius has a major influence on surface finish. A sharp point at the end of a tool leaves a groove on the path of cut. Increase in nose radius usually decreases tool wear and improves surface finish. Generally, for roughing largest nose radius is selected. A larger nose radius permits higher feed, but must be checked against any vibration tendencies.
Leave a Reply