Fracture toughness is an engineering property that defines the resistance of a material against cracking. Tough materials require large amounts of energy to crack whereas low toughness materials have little resistance against cracking. For the materials used in aircraft structures, fracture toughness is just as important as other mechanical properties such as elastic modulus and strength. Aerospace materials need high toughness to resist the growth of cracks initiating at damage sites (e.g. corrosion pits, impacted regions) or sites of high stress concentration (e.g. fastener holes, windows, doors and other access points in the aircraft).
There are several test methods to measure fracture toughness, and the most common is the single-edge notch bend (SENB) test. The SENB specimen is a rectangular block of the test material containing a machined notch with a V-shaped tip (Fig. 5.18). The notch extends about 50% through the specimen. The SENB test involves applying a three-point load to the specimen to generate a tensile stress at the notch tip. The applied load required to grow a crack from the notch tip through the specimen is used to calculate the fracture toughness. Tough materials require a high load to cause complete fracture of the specimen. Another popular fracture test is the compact tension (CT) method, which involves tension loading a block-shaped specimen containing a sharp notch (Fig. 5.19). The load required to break the specimen is used to calculate the fracture toughness.
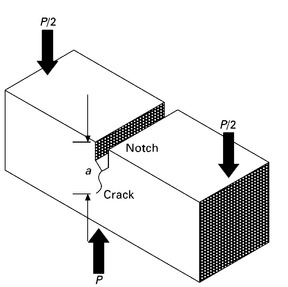
5.18 Single-edge notch bend specimen for fracture toughness testing.
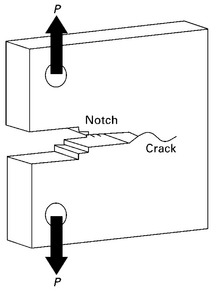
5.19 Compact tension specimen for fracture toughness testing.
The toughness values for materials vary over a wide range (five orders of magnitude), from the very tough to extremely brittle. Tough metals have a fracture energy of 100 kJ m−2 or more, whereas those of weak brittle materials are under 0.01 kJ m−2. Most high-strength alloys, including those used in aircraft structures, have moderately high toughness (20–100 kJ m−2). Fibre–polymer composites have anisotropic toughness properties because of their microstructure, and the highest toughness (10–30 kJ m−2) is when the direction of crack growth is perpendicular to the fibre orientation. The fracture toughness properties of aerospace materials.
The toughness properties of materials are also measured using impact tests. These tests involve measuring the energy required to fracture the material specimen when impacted at high velocity by a heavy object. The impact energy absorbed by the specimen is related to its toughness; tough materials require higher impact energies than brittle materials. The most popular methods are the Charpy and Izod impact tests. Both tests involve striking the specimen containing a V-notch with a pendulum travelling at a set speed. Impact loading of the specimen produces much higher strain rates than those generated in the SENB and CT fracture toughness tests. Therefore, the Charpy and Izod tests are useful for determining the dynamic toughness of materials under high loading rates, such as those experienced during an impact event (e.g. bird strike). However, the tests are qualitative; the result can only be used to compare the relative impact toughness properties between materials. Impact test results cannot be used to calculate the intrinsic fracture toughness of the material, although the test is used as a simple, accurate and inexpensive method for screening materials for toughness.
Leave a Reply