EIP development (EIPD) is a new paradigm for achieving excellence in business and environmental performance. It opens up innovative new avenues for managing businesses and conducting economic development. By creating linkages among local “resources,” including businesses, nonprofit groups, governments, unions, and educational institutions, communities can creatively foster dynamic and responsible growth. Antiquated business strategies, based on isolated enterprises, are no longer responsive enough to market, environmental, and community requirements.
Economic development is a never‐ending challenge for communities. As the global marketplace has become increasingly competitive, municipalities, counties, states, and regions seek new strategies for attracting good investments with good jobs. Moreover, communities everywhere are demanding improvements in local ecosystems. In the past, economic development and environmental protection were seen as mutually exclusive. However, new practices and activities are challenging that assumption. One broad category of activities falls under the umbrella of EIPD.
Sustainable EIPD looks systematically at development, business, and the environment attempting to stretch the boundaries of current practice. On one level, it is as directly practical as making the right connections between wastes and resources needed for production. At another level, it is a whole new way of thinking about doing business and interacting with communities. The eco‐industrial approach has many ways of being applied. At a most basic level, each organization seeks higher performance internally. However, most eco‐industrial activity is moving ahead by increasing interconnections between companies.
Just as in nature interconnected systems work together to ensure survivability and efficient use of resources and energy, in the business world, strategic partnerships, networked manufacturing, and preferred supplier arrangements assist companies to grow, to contain costs, and to reach for new opportunities. Eco‐industrial development can help to achieve these goals by offering businesses access to cost‐effective, quality resources for producing products or delivering services.
The vital task of securing community support for eco‐industrial projects calls for multi‐stakeholder engagement in setting a vision for local development. Companies that offer attractive models in their community outreach will have an edge in obtaining popular support. Attention to getting wide backing for a project in the early planning stages can reduce delays due to the reflexive community opposition that often crops up when a major change is proposed. A positive and proactive stance in anticipating and overcoming residents’ concerns can be most helpful.
The three mini‐case studies presented in Section 9.2.3 illustrate the range of results that are possible when an attempt is made to husband the resources and improve the environment of communities dominated by a single industry.
EIPs – The Ebara Process: Mini Case Study 9.1 in Japan
The first fertilizer plant using the Ebara process using SO2 and NOx gases from a nearby coal‐fired power station was developed and marketed by the Tokyo‐based Ebara International Corporation (Das 2005; Ebara 2010). Electron beam irradiation of a flue gas containing both SO2 and NOx (about 95% NO and 5% NO2) acts on these pollutants by oxidizing them to nitrogen dioxide and sulfur trioxide anions. Addition of water and ammonia to these ionized gases yields solid products, ammonium nitrate (NH4NO3), and ammonium sulfate ((NH4)2SO4) that can be separated and sold as fertilizers. The simplified chemical reactions are as follows:





The main attraction of the Ebara process (Figure 9.2) is the simultaneous removal of both SO2 and NOx. The complex reaction mechanism entails ionization, the formation of excited electronic states, the transfer of excitation energy between molecules, molecular dissociation, electron capture, neutralization, and radical reactions. The flue gas is first cooled and humidified, then irradiated by means of a high‐intensity electron beam. The flue gas is routed first through electrostatic precipitators (ESPs) or other mechanical collectors to remove particulates, such as fly ash. The gas is next piped to a spray cooler and humidified and cooled to a temperature in the 160–200 °F range, the optimal temperature. Anhydrous ammonia is introduced in stoichiometric amounts at this point. The ammoniated flue gas is passed to an electron‐beam reactor chamber, where it is irradiated (1.5 Mrad dose), producing nitrate and sulfate anions. These species react with ammonia to yield a dry, particulate mixture of NH4NO3 and (NH4)2SO4.
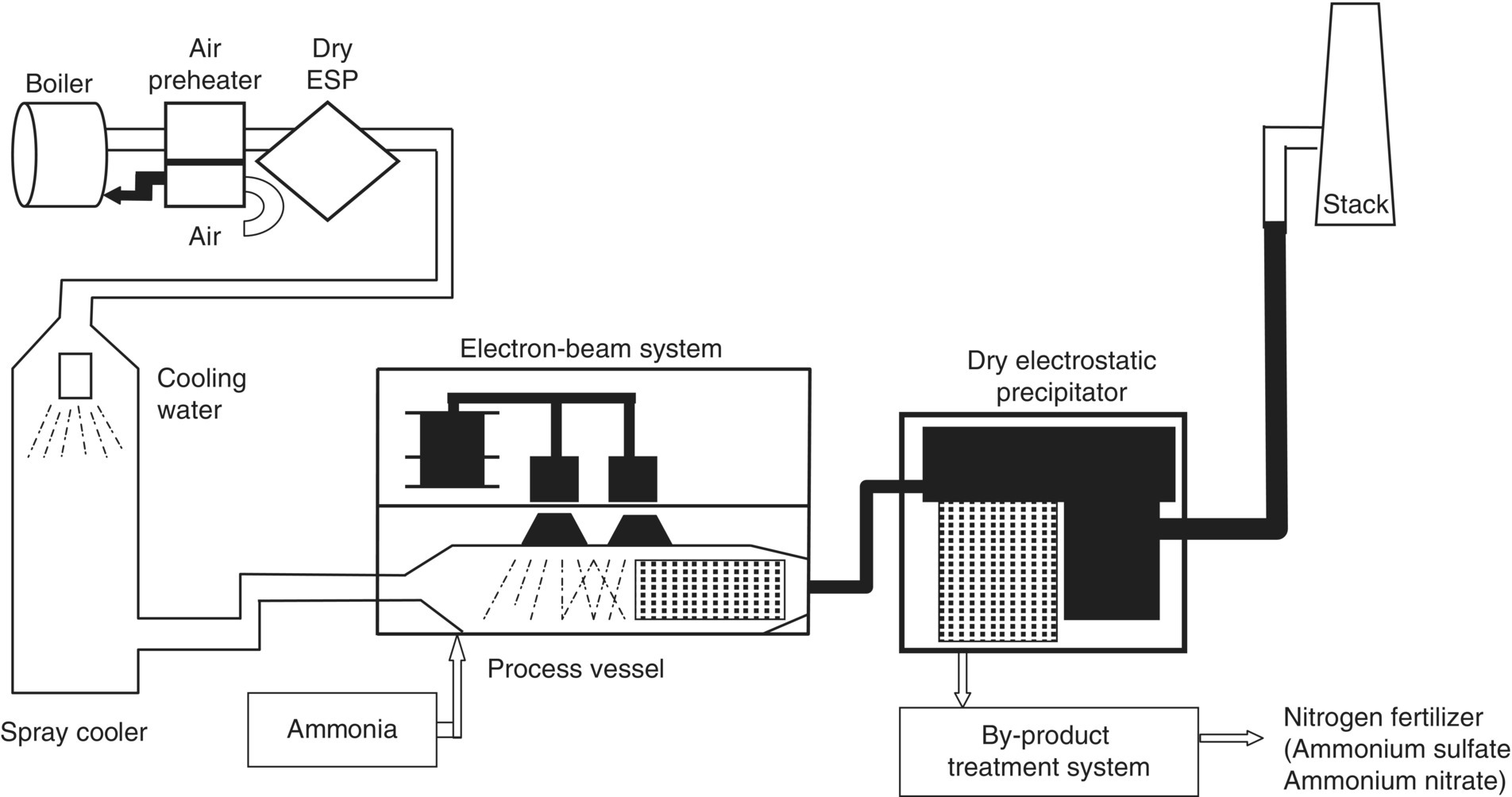
Leave a Reply