Earthwork and moving equipment are available to suit different field conditions which are discussed below.
1. Excavators
Excavators are digging machines. These machines consist of the following components (Fig. 32.1):
- An undercarriage – this gives mobility to the excavator. This may be mounted with crawler track or wheel.
- A superstructure with operator’s cabin – this could traverse through 360° or fitted on a rigid frame.
- Hydraulically articulated booms and dipper arms with bucket.
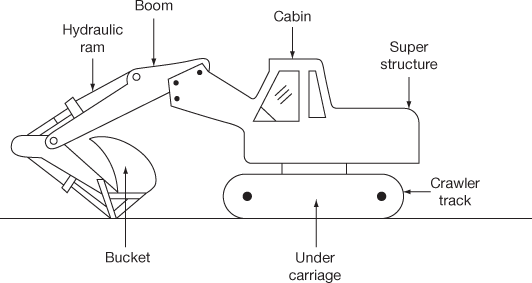
Figure 32.1 Excavator
Excavators may be of mechanical (or cable operated) or hydraulic types. Hydraulic excavators have more advantages. They can be fitted with various multi-purpose attachments for various earth moving works. Most efficient action of the machine is that the hydraulic unit of action of the excavator which directs the bucket teeth at their most efficient angle during dipping operation.
Mechanical or cable operated excavators are of either hoe or shovel type. In hoe type the bucket opening fences towards the machine whereas in shovel the bucket opening faces away from the machine.
Excavators are of four types, viz., crawler-mounted excavator, truck-mounted excavator, self-propelled excavator, and excavator mounted on barge or rail.
Excavators include dipper or power shovel, dragline, clamshell and drag shovel. All these machines basically fall under shovel family in that the front end only is changed. Shovel based machines have a common type of operating and tracking mechanism.
2. Shovels
Shovel is often used for a specific type of excavating machine fitted with a short length boom and working with forward strokes. The following are the four types of machines which have the same basic structure but the front-end attachments are different:
- Dipper shovel
- Drag shovel or hoe
- Dragline
- Clamshell
The frontline attachments are as follows:
- Shovel boom and dipper stick for a dipper shovel.
- Shovel boom, jack boom and stick for a drag shovel.
- Crane boom with a failed and a loosely attached bucket for dragline.
- Crane boom with a special type of bucket for a clamshell.
(i) Dipper Shovel
The dipper shovel or power shovel is the most popular of the shovel excavator. It consists of a boom, dipper stick, the bucket and the mechanism of operation. The lower end of the boom is hinged to the support bracket and the upper end carries the bucket hoist sheaves. The dipper stick moves back and forth on a dipper drum through a guide formed by a saddle block. In order to cause the stick to slide back and forth, the dipper drum is rotated (Fig. 32.2). The bucket of the power shovel is strongly built of steel. These are generally used for digging hard rock in quarries or ores in mines. The digging is done above the machine base level
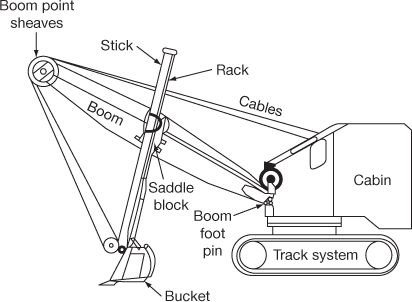
Figure 32.2 Dipper shovel
(ii) Drag Shovel or Hoe
It is also called as a Pull shovel. As this machine resembles the digging mechanism of an ordinary garden hoe it gets the name. The digging action results from the drag or pull of the bucket towards the machine. This action helps for digging below the machine level particularly while digging for trenches, footings, basements, etc., Fig. 32.3 (Mahesh Varma, 1979).
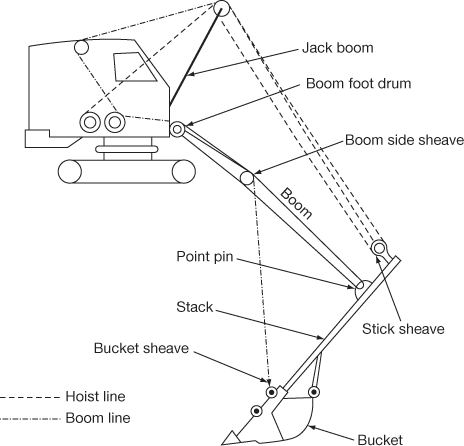
Figure 32.3 Drag shovel (Source: Mahesh Varma 1979) (Construction Equipment: It’s Planning & Applications, 1979, Metropolitan, New Delhi)
This shovel consists of a boom, a stick, a jack boom and a bucket which is attached at the end of the stick. The stick is hinged by a pin with a boom. This enables to turn over the pin to take any desired direction best suited for digging or dumping operations. The lower end of the stick carries the bucket and the upper end carries a sheave having the hoist cable supported on a jack bottom at the other end. This arrangement enables to hoist the cable when pulled and the reaction at the stick enables to move the boom with stick up or down. Thus the boom is capable of taking any position in vertical plane.
Drag shovels have application in
- Digging trenches, footings or basements
- Digging for hard materials
- Providing close trimming whenever needed, and
- Where excavated materials need to be dumped at a short distance.
(iii) Dragline
As this machine drags the bucket against the material to be dug it attains this name. This consists of a boom, a bucket, a fairlead and hoist, dump and drag cables, Fig. 32.4 (Mahesh Varma, 1979). The boom is similar to that of a crane boom. The top and bottom ends of the boom are known as the point and the foot respectively. The boom is attached to the deck with pin at foot and supported at the point through the boom hoist cable. This cable passes over a pair of sheaves placed one on each side. They have three types of buckets, viz., light, medium and heavy, which are used depending on the nature of material.
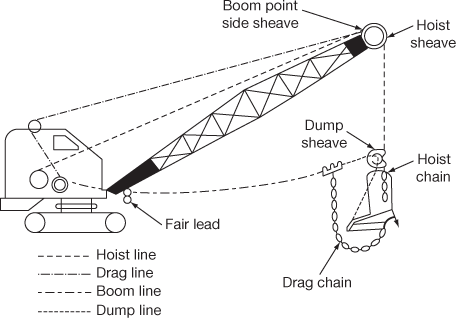
Figure 32.4 Dragline (Source: Mahesh Varma, 1979) Construction Equipment: It’s Planning & Applications, 1979, Metropolitan, New Delhi
A dragline can dig and dump over longer distance than an ordinary shovel can do. Because of its long boom the machine need not be seated close to the pit. Thus it can handle digging of underwater excavation while stationing the machine on a firm soil away from the location of the pit. This can dig below the track level and can handle soft materials comfortably.
(iv) Clamshell
It gets the name as its bucket resembles to a clam which is a shellfish with a hinged double shell. It is having most of the characteristics of dragline and crane. Digging is done as in a dragline and soon after the bucket is filled, it works like a crane. It has a crane boom with a specially designed bucket attached to it at the upper end through cables. The bucket is hinged at top and has either sharp edge or the teeth at the bottom (Fig. 32.5).
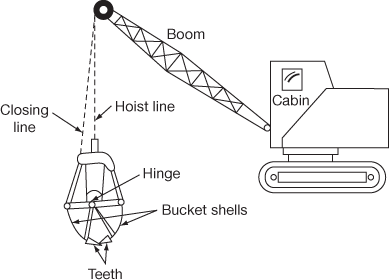
Figure 32.5 Clamshell
During digging process the bucket is lowered with shells open. When reaching the surface to be dug it makes a good contact with it. The weight of the bucket helps the sharp-edge or the teeth at the bottom of the bucket to dig into the surface or material, thereby filling the bucket. Once the bucket is filled the shells close.
The bucket is then hoisted and swung to the position where dumping has to be done and contents are dropped. Buckets may be light or heavy weight and used depending on the type.
Its applications are widely used where
- The digging or dumping vertically is needed.
- The material is relatively soft or medium hard.
- Digging of trenches.
- Loading materials in a bin or a stock pile.
- Accurate dumping of materials.
3. Bulldozers
It is an important equipment on a construction project. It is basically a scraping and pushing unit. However, it is a multi-purpose equipment which can be used for different purposes with some modifications. Accordingly they are called as angle dozer, tilt dozer, tree dozer, and push dozer. Up to 100 m distance these can be used to haul.
Angle dozer pushes its load at an angle (nearly 25°) to the direction of travel. This is helpful (i) when the material has to be pushed down the slope on hill work and (ii) where a long windrow has to be made during the travel of the dozer.
Tilt dozer is used to start excavating a ditch or a trench or for excavation in hard ground. For this the blade is required to be tilted by raising one end up to 25 cm above the other. Push dozer is used to push the scraper unit after digging and also during loading operation using the pusher plate.
Tree dozer is used to uproot and remove trees.
4. Tractors
A tractor is a multi-purpose machine. This comes in varied type of light model to heavy model. The light model is used for agricultural or small haulage purposes. Heavy model equipped with several special rings are used for earth moving work. This is an important piece of equipment which is indispensable on all important projects.
Two principal applications of tractors are as follows:
- Clearing and excavating machinery.
- Hauling and conveying machinery.
There are two types, viz., wheeled tractors and crawler tractors. The wheeled type is used for light and speedy jobs. As regards to its applicability it falls between the crawler tractor and the truck. The crawler tractors are rugged machines which are used for heavy duty work. It is used particularly when there is a demand for more tractor power and speed of movement. Now-a-days wheeled units have been made to work on the jobs which are intended for the crawler type. Wheel tractors are now available for all practical earth moving jobs including nipping and dozing.
5. Motor Graders
A grader is primarily a device for loading or finishing earth work. Sometimes it is also used for mixing gravel, making windrows and trimming slopes. There are two types of graders, viz., towed and motorised.
The towed type is of small size with a tractor. The controls are in general manual and sometimes a small petrol engine is fitted on the framework of the grader to operate the controls. It is operated by separate operator.
Attachments to the grader include the blade (also called as moldboard), the scarifier, the bulldozer or the snowplow, the elevator and the roller. The versatility of the machine is increased by the addition of these tools. The blade is thick and like a blade of dozer and can swivel through 180°. The scarifier is the tool for loosening hard soil and may be mounted in the front or in the rear of the machine. The bulldozer and the snowplow (a V-shaped/blade) are front-cut attachments enables the grader to pick up the material cut by the blade and drop it over an inclined belt conveyor which transmits it into carrier unit or discharges it aside the windrow. In order to compact or smoothen the ground surface, a roller may be attached to the rear of the grader.
6. Scrapers
Scrapers are the devices to scrap the ground to load the material, to transport to the required distance, to dump at the intended place, to spread the dumped material over the required area, to attain the desired thickness and to return back to do the next cycle. In simple terms scrapers are designed to dig, load, haul, dump and spread. As a scraper does a multiple works it is also called a carry all.
A scraper is provided with a bowl, apron, ejector and a hydraulic system which are explained below (Fig. 32.6).
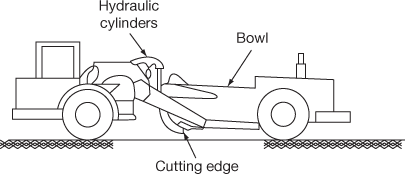
Figure 32.6 Scraper
(i) Bowl
It is a pan which is to hold the scraped material. It is hinged at the rear corners to the rear axle inside the wheels. It can tilt down for digging or ejecting. The size of a scraper is specified by the size of the bowl. At the bottom of the bowl a cutting edge is attached. In order to make a shallow cut, the cutting edge is lowered into material or dirt.
(ii) Apron
It is a wall located in front of the bowl to open or close in order to regulate the flow of the material in and out of the bowl. Further it is capable to open or to close during the carrying position also.
(iii) Ejector
It is also called as a tail gate which is the rear of the pan. It is provided with forward and backward movement inside the bowl. During loading it remains at its rear wall and moves in the forward direction to help in the ejection of the load during dumping.
(iv) Hydraulic System
All these operations are controlled by hydraulic cylinders.
The operation of a conventional scraper comprises of (i) digging or loading, (ii) transporting and (iii) unloading.
(i) Digging or Loading
Keeping the ejector at the rear and the apron raised (approximately to 40 cm) the operator moves to the cut. The bowl is then lowered to the required depth of cut, and the engine speed is increased and moved forward keeping the optimum depth of cut. After filling the bowl the apron is closed and the bowl is then raised.
(ii) Transporting
The bowl is transported in raised position so as to provide sufficient clearance from the ground. In order to prevent the loss of the collected material the apron is fully closed.
(iii) Unloading
The process of unloading by the scraper is called as dumping and spreading operation. In this operation the bowl is positioned so as to spread the material. So as to have an even spreading, a partial opening of the apron in the stage of unloading will be helpful. In the case of wet and sticky material, the apron should be raised and lowered separately. This helps the material behind it is get loosened and material drops out of the bowl by moving the ejector forward, the remaining material is pushed out at a uniform rate. After the dumping is complete, the tail gate is fully retarted, the apron is dropped and the bowl is raised to the transporting position. Using the cutting edge final finishing is done.
7. Loaders
Loader is a machine in which a bucket is attached to the arms and capable of being raised, lowered and dumped through mechanical or hydraulic controls. A very common type is one in which the loader is having the bucket in the front which is known as front-end loader.
Loaders are self-propelled and versatile equipment which are mounted either on crawler or wheel-type running gear. These loaders are fitted with front mounted general purpose bucket.
These loaders are operated through hydraulic rams with which they dig, scoop, lift, transport, carry, dump or load into hauling units, bins, hoppers, conveyors and stockpiles. With the additional parts added to the front and rear mounted attachments these can doze, scrap, grab, forklift, trench, grade, ditch, rip, clamp and winch.
Loaders are used for handling coal, sugar, sand, salt, stone, etc., to earth moving and digging works. Two types of loaders are crawler loaders and wheeled loader.
8. Trenchers
Trenchers are used to make trenches. Trenchers are used for excavating trenches or ditches of variable width and depth. The present day trenchers can be used to make trenches of width up to 12 m and depth up to 3 m can be excavated in one pass. Basically a trencher consists of :
- Self-propelled tractor (Fig. 32.7) or carrier mounting fitted with crawler or wheel-type running gear (Fig. 32.8).
- An excavating device consisting of several buckets on the periphery of the wheel and alternatively several cutters are provided for digging and discharging continuously.
- A provision conveying the excavated material.
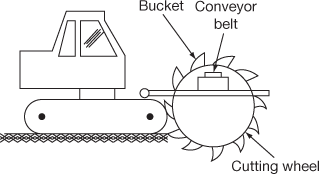
Figure 32.7 Trencher with tractor
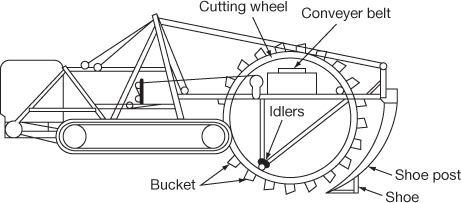
Figure 32.8 Wheel-type trencher or ditcher
The common type of trench excavator is the wheel trenchers. It consists of a pair of circular rims whose outside diameters are connected by V-shaped buckets or cutters. The wheel is turned by a chain drive which connects to the power source. The wheel moves to the top position when discharging the material and at the bottom position while digging. The buckets or cutters on the wheel perform the work of excavator while travelling upward. When the wheel reaches the top position the excavated material drops. The dropped material is carried on conveyors and discharged alongside of the trench.
The selection of a trenching equipment depends on various factors, viz., depth and width of trench, type of soil, disposal of excavated earth, ground water position, and the nature of the job.
Leave a Reply