Fibre–polymer composites are susceptible to damage from impact events such as bird strike, dropped tools during aircraft maintenance, tarmac debris kicked-up by the wheels during take-off or landing, and large hail stones. Impact testing is performed at different impact energy levels to screen composite materials for damage resistance and damage tolerance. The most common and simplest test for measuring impact resistance is the falling- weight test, as shown in Fig. 5.20. A flat specimen panel of the composite material is impacted perpendicular to the surface by a hard object, usually a hemispherical steel tub. The weight is dropped from a height of 1–2 m with a mass of 4.5–9 kg to replicate a low-velocity impact event on an aircraft. The amount of damage caused by the impact event is measured (often by a nondestructive inspection method such as ultrasonics or radiography) to determine the damage resistance. The residual mechanical properties, such as compression strength or fatigue life, may also be measured to determine the damage tolerance. Civil aviation authorities specify no reduction to the mechanical properties following an impact at an energy level in the range of 35–50 J whereas the USAF specifies a minimum energy level of 135 J.
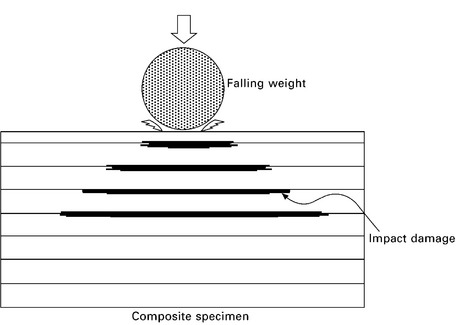
5.20 Impact testing of composites.
Other impact tests are often included at higher energy levels to fully characterise the impact resistance of aircraft composite components. These may include ballistic impact for critical military structures (e.g. main rotor blades), ice-hail simulation and bird strike simulation.
Leave a Reply