Single‐step DME synthesis reactors typically utilize a mix of two catalysts, one promoting the synthesis of methanol from syngas (CO + 2H2 → CH3OH) and one promoting the dehydration of the methanol to DME (2CH3OH → CH3OCH3 + H2O). Both liquid‐phase and fixed‐bed reactors are offered commercially. Leading developers of liquid‐phase DME synthesis reactors are DME Development, Inc., a Japanese consortium of nine companies led by NKK and Nippon Sanso (Adachi et al. 2000; Air Products and Chemicals 2001; Brown et al. 1991; Fujimoto et al. 1995; Ohno 2006).
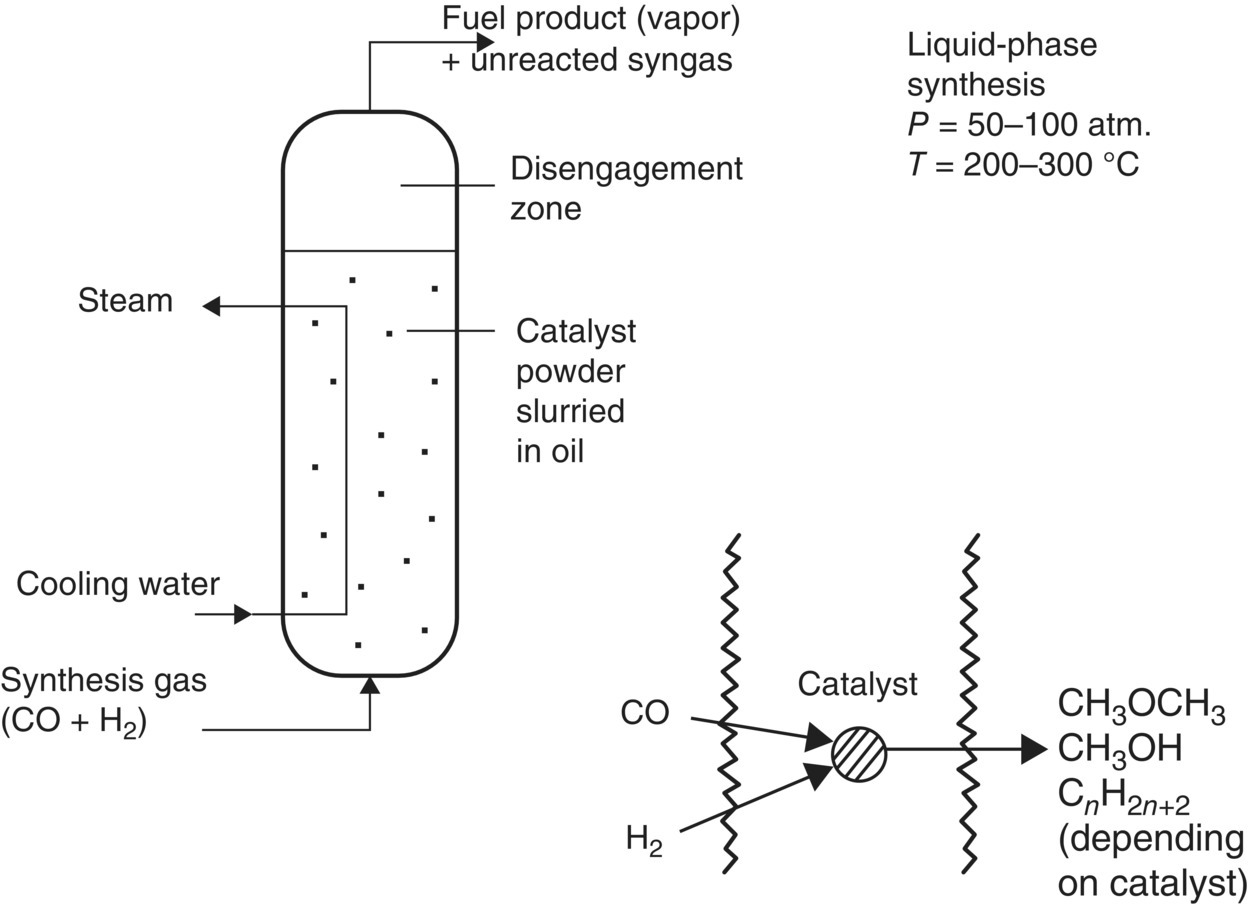
The DME reactor design of Air Products is derived from its liquid‐phase methanol (LPMEOH) synthesis process developed in the 1980s. A commercial‐scale LPMEOH demonstration plant (250 T/day methanol capacity) has been operating since 1997 with gas produced by the Eastman Chemical Company’s coal gasification facility in Kingsport, Tennessee (Eastman Chemical and Air Products and Chemicals 2003). The construction of this facility was preceded by extensive testing in a 10 tpd process development unit (PDU) in LaPorte, Texas. The PDU was operated in 1999 to generate test data on direct DME synthesis (Air Products and Chemicals 1993, 2001, 2002; Weyerhaeuser Company 2000).
Pressurized Chemrec BLG
In 2010, a black liquor gasification DME and motor fuel (MF) demonstration plant was inaugurated in Piteå in Sweden (Landälv et al. 2010). Figure 9.23 shows a schematic of the Piteå DME and MF production plant (Landälv et al. 2010; Larson et al. 2006a). When used as a fuel in a truck diesel engine, BioDME gives an equally high‐efficiency rating and a lower noise level compared with a conventional engine. Compared with diesel, BioDME generates an impressive lower carbon dioxide emission (CO2). In addition, its combustion produces very low emissions of particulate matters (PM) and nitrogen oxides (NOx). This makes BioDME an ideal fuel for diesel engines. DME is a gas at ambient conditions but is liquefied at low pressure, just five bars and is handled as a liquid during distribution and use. It is simple to handle, similar to propane. DME can be produced from natural gas and also from various types of biomass. When it is produced from biomass, it is known as BioDME (Larson et al. 2006a; Salomonsson 2011).
The BioDME project aims to demonstrate production of environmentally optimized synthetic biofuel from lignocellulosic biomass at an industrial scale (Landävl 2010; Lindblom 2012; Salomonsson 2013). The project involves a consortium of Chemrec, Haldor Topsøe, Volvo, Preem, Total, Delphi, and ETC. The project is supported by the Swedish Energy Agency and the EU’s Seventh Framework Program. The output of this demonstration is DME produced from black liquor through the production of clean syngas and a final fuel synthesis step. The overall possible chemicals that can be produced from the syngas are hydrogen, methanol, DME, FT fuels, ethanol, and methyl tertiary butyl ether (Tampier et al. 2004).
Leave a Reply