Processes used in the manufacture of products follow known production guidelines and adhere to environmental rules and regulations and the ease at which this is done includes the ability of the designer to incorporate already existing designs, refine and adapt product mixes, and to manipulate products to use designs in ingenious manners to create complimentary products using the same or improved tooling. Products meet strict monetary guidelines dedicated to responsible selection of materials, clean production; monitoring processes to avoid waste within local and global boundaries.
Design for manufacturing (also sometimes known as design for manufacturability or DFM) is the general engineering practice of designing products in such a way that they are easy to manufacture. The concept exists in almost all engineering disciplines, but the implementation differs widely depending on the manufacturing technology. DFM describes the process of designing or engineering a product in order to facilitate the manufacturing process in order to reduce its manufacturing costs. DFM will allow potential problems to be fixed in the design phase which is the least expensive place to address them. Other factors may affect the manufacturability such as the type of raw material, the form of the raw material, dimensional tolerances, and secondary processing such as finishing.
DFM process asks typical questions: Is the product easy to manufacture? Does it facilitate environmentally and socially responsible manufacturing by, for example, having components that can be cleaned without the use of toxic materials? Does it reduce production of products that fail quality standards, thus reducing manufacturing waste? From a sustainable engineering perspective, much of the environmental and social impacts of manufacturing can be ameliorated not just by proper manufacturing line design, but through good product design as well (Allenby 2012).
Depending on the various types of manufacturing processes, there are a set of guidelines for DFM practices. These DFM guidelines help to precisely define various tolerances, rules, and common manufacturing checks related to DFM. While DFM is applicable to the design process, a similar concept called Design for Six Sigma is also practiced in many organizations.
Design for Assembly
Manufacture for assembly can pay homage to work done in vehicle creation that originally used all three methods of assembly to produce high‐quality products; human, mechanical, and a combination of human and mechanical assembly. The goal of production is to use thoughtful creation to produce a product with speed and without error which includes the use of human ergonomics, technical oversight of mechanical creation combined with regular maintenance. Assembly that doesn’t overheat, freeze, or breakdown easily gets high marks in service longevity and higher profits.
Design for Disassembly
What is put together needs to be made such that it can come apart without harm. The areas of concern range from upgrades, to rebuilds of product; modifications and adaptations of machinery used to create products; flexibility of product manufacture to meet changing standards; and improved reduction of waste and cost of manufacture by being able to reverse processes.
When decisions are made to initially make a product, mock ups are made and pilots are put into production and the product is put to rigorous testing, engineering also takes on the job to refuse to duplicate one‐case only scenarios, reliability includes the unexpected and how to fix it.
Design for Sustainable Manufacturing
Sustainable manufacturing can be defined as the creation of a manufactured product through a concurrent improvement in the resulting effect on factory and product sustainability. The concept of sustainable manufacturing demands a renewed design of production systems in order to condition the related sustainability on product life cycle and factory operations.
Designing sustainable production systems imply, on the one hand, the analysis and optimization of intra‐factory aspects that are related to manufacturing plants. Such aspects can regard the resource consumption restrain, reuse resources discarded from previous products rather than to continue using virgin materials to improve the process efficiency, the ergonomics for the factory workers, the elimination of hazardous substances, the minimization of factory emissions and waste as well as internal emissions, the integrated management of information in the production facilities, and the technological updating of machines and plants.
Other inter‐factories aspects concern the sustainable design of manufactured products, product chain dematerialization, management of the background and foreground supply chains, support of circular economy paradigm, and the labeling for sustainability.
Design for Sustainability
Design for sustainability (also called environmentally sustainable design, environmentally conscious design, etc.) is the philosophy of designing physical objects, the built environment, and services to comply with the principles of social, economic, and ecological sustainability.
The intention of sustainable design is to “eliminate negative environmental impact completely through skillful, sensitive design.” Manifestations of sustainable design require renewable resources, impact the environment minimally, and connect people with the natural environment.
Great design is sustainable design: rather than considering green building design as an externality, architects must think about it as a set of principles for great design. This includes better user experience and comfort, doing more with less to enable the building to easily achieve peak performance, and maximizing the effectives of durable, quality materials. Rather than the well‐known edict “form follows function,” it’s time to think “form follows environment.”
Beyond the “elimination of negative environmental impact,” sustainable design must create projects that are meaningful innovations that can shift behavior. A dynamic balance between economy and society intended to generate long‐term relationships between user and object/service and finally to be respectful and mindful of the environmental and social differences (McLennan 2004).
Many more modules might be used, depending in part on the particular product and the specific design issues associated with it. Moreover, these sorts of product design processes require expertise in very different areas, which is one reason modern product design is usually done by teams (AIChE, IFS 2004; Allenby 2012; Sikdar 2003). For example, the law department would provide input on applicable regulations and potential liabilities that should be addressed, while the environment, health, and safety group (or corporate equivalent) would provide the technical expertise on environmental implications of product design and manufacturing options. Among engineering team members, it is likely that some would be experts in design of manufacturing processes, some in product design, some in materials science, and, increasingly, some experts in lifecycle assessment of process and product impact and performance. Note, however, that design is always a balancing process, with many different constraints and objectives; what emerges must reflect real‐world conditions, rather than wishful thinking. Thus, for example, sustainability activities are free to demand that all toxics be eliminated from a complex product, but it is rare design indeed where engineers can do that and at the same time meet all other relevant conditions. Similarly, it is often the case that activist groups do not reflect the characteristics of all consumer segments in the marketplace; firms can lead, but at least in a free market they must also be responsive to consumer demand (Allenby 2012).
So what is the process that a product might go through before it actually gets to the market? Figure 10.1 maps out a typical route, with decision points, usually called “gates,” noted as numbers (Allenby 2012; Graedel and Allenby 2003). At each gate, either a formal or informal review by the team responsible for the product, which might include not just the design team members, but people from marketing, sourcing, logistics, external affairs (an organization responsible for both representing the firm to external audiences and informing the firm about looming developments, such as material bans, that might affect the product), is held. The continued commercial viability of the product is assessed, given the product characteristics that are increasingly locked in as the design proceeds. The reason for such continued assessments is clear: the earlier an uncompetitive product is identified and killed, the less time, money, and resources are wasted. Thus, each gate not only informs the next stage of the design process, but is an important governance mechanism assuring robust design. From a sustainable engineering perspective, these gates become even more important, as they are existing mechanisms for managing the ever increasing demands of stakeholders and NGOs on firms, their products, and their activities around the world. A good gate process can be an important part of institutionalizing sustainable engineering. Conversely, an inadequate one – say, one that ignores the requirements of important markets, or of powerful activist stakeholders, or fails to identify important sustainability issues so that they may be addresses early in the design stage – can make a design less efficient, more expensive, and perhaps inadequate (Allenby 2012).
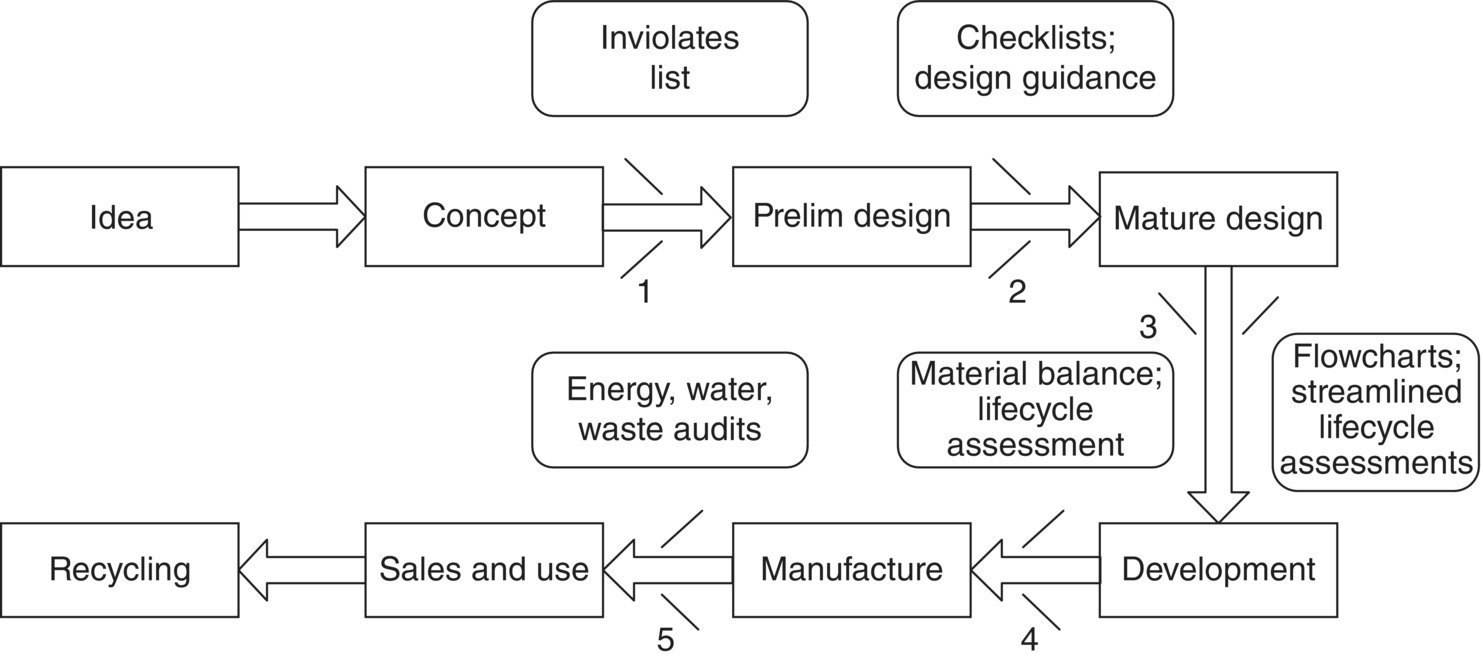
Leave a Reply