The costs and estimating methodology in this section are directed toward the “study” estimate with a nominal accuracy of ±30%. According to Perry’s Chemical Engineer’s Handbook, a study estimate is “used to estimate the economic feasibility of a project before expending significant funds for piloting, marketing, land surveys, and acquisition. However, it can be prepared at relatively low cost with minimum data” (Perry and Green 1997). Specifically, the development of a study estimate calls for knowledge of the following:
- Location of the source within the plant
- Rough sketch of the process flow sheet (i.e. the relative locations of the equipment in the system)
- Preliminary sizes of, and material specifications for, the system equipment items
- Approximate sizes and types of construction of any buildings required to house the control system
- Rough estimates of utility requirements (e.g. electricity)
- Preliminary flow sheet and specifications for ducts and piping
- Approximate sizes of motors required
In addition, since the accuracy of an estimate (study or otherwise) depends on the amount of engineering work expended on the project, the user will need an estimate of the labor hours required for engineering and drafting activities. There are four other types of estimate.
The order‐of‐magnitude estimate, a rule‐of‐thumb procedure, can be used only for plant installations of the repetitive type for which there exists good cost history. Its error bounds are greater than ±30%. (However, Perry states that “no limits of accuracy can safely be applied to [an order‐of‐magnitude estimate].”) The sole input required for making an order‐of‐magnitude estimate is the control system’s capacity (often measured by the maximum volumetric flow rate of the gas passing through the system).
The other three types of estimate, listed next, are preferable.
- Scope, budget authorization, or preliminary. This estimate, nominally of ±20% accuracy, requires more detailed knowledge than the study estimate regarding the site, flow sheet, equipment, buildings, etc. In addition, rough specifications for the insulation and instrumentation are also needed.
- Project control or definitive. These estimates, accurate to within ±10%, require yet more information than the scope estimates, especially concerning the site, equipment, and electrical requirements.
- Firm or contractor’s or detailed. This is the most accurate (±5%) of the estimate types, requiring complete drawings, specifications, and site surveys. Consequently, detailed cost estimates are typically not available until right before construction. Common sense suggests that there is seldom enough time to prepare such estimate before approval to proceed with the project has been obtained.
Elements of Total Capital Investment
Total capital investment (TCI) includes all costs required to purchase equipment needed for the control system (purchased equipment costs), the costs of labor and materials for installing that equipment (direct installation costs), costs for site preparation and buildings, and certain other costs (indirect installation costs). TCI also includes costs for land, working capital, and off‐site facilities.
Direct installation costs include costs for foundations and supports, erecting and handling the equipment, electrical work, piping, insulation, and painting. Typical indirect installation costs are engineering costs, construction and field expenses (i.e. costs for construction supervisory personnel, office personnel, rental of temporary offices, etc.), contractor fees (for construction and engineering firms involved in the project), start‐up and performance test costs (to get the control system running and to verify that it meets performance guarantees), and associated costs with contingencies. “Contingencies” is a catch‐all category that covers unforeseen costs that may arise if, for example, it becomes necessary to redesign, modify equipment, to pay higher costs of equipment or field labor costs, or to compensate for delays in start‐up. Contingency costs are not the same as uncertainty and retrofit factor costs.
The elements of TCI are displayed in Figure 7.1. Note item “battery limits” cost, which is the sum of the purchased equipment cost, direct and indirect installation costs, and costs of site preparation and buildings. By definition, this is the total estimate for a specific job; any support facilities that may be needed (e.g. control systems) are assumed to already exist at the plant and are not included in the battery limits. For systems installed in new plants, off‐site facilities (special facilities for supporting the control system) also might be excluded from the battery limits. Off‐site facilities are exemplified by units to produce steam, electricity, and treated water; laboratory buildings; and railroad spurs, roads, and other transportation infrastructure items. Pollution control devices rarely consume enough energy to warrant dedicated off‐site capital units. However, it may be necessary – especially in the case of control systems installed in new or “grassroots” plants – to build extra capacity into the site’s generating plant to service the system. (A Venturi scrubber, which often requires large amounts of electricity, is a good example.) Nevertheless, that the capital cost of a device does not include utility costs, even if the device were to require an offsite facility. Utility costs are charged to the project as operating costs at a rate that covers both the investment and operating and maintenance costs for the utility.
As Figure 7.1 shows, the installation of pollution control equipment may also require land, but since most add‐on control systems take up very little space (a quarter‐acre or less), this cost tends to be relatively small. Certain control systems, such as those used for flue‐gas desulfurization or selective catalytic reduction (SCR), require larger quantities of land for the equipment, chemicals storage, and waste disposal. In these cases, especially when a retrofit installation must be performed, space constraints can significantly influence the cost of installation, and the purchase of additional land may be a significant factor in the development of the project’s capital costs. Land retains its value over time; however, land is not treated the same as other capital investments, retains its value over time, the purchase price of new land needed for sitting a pollution control device can be added to the TCI, but it must not be depreciated. Instead, if the firm plans to dismantle the device at some future time, either the land should be excluded from the analysis or its value included at the disposal point as an “income” to the project, to net it out of the cash flow (CF) analysis.
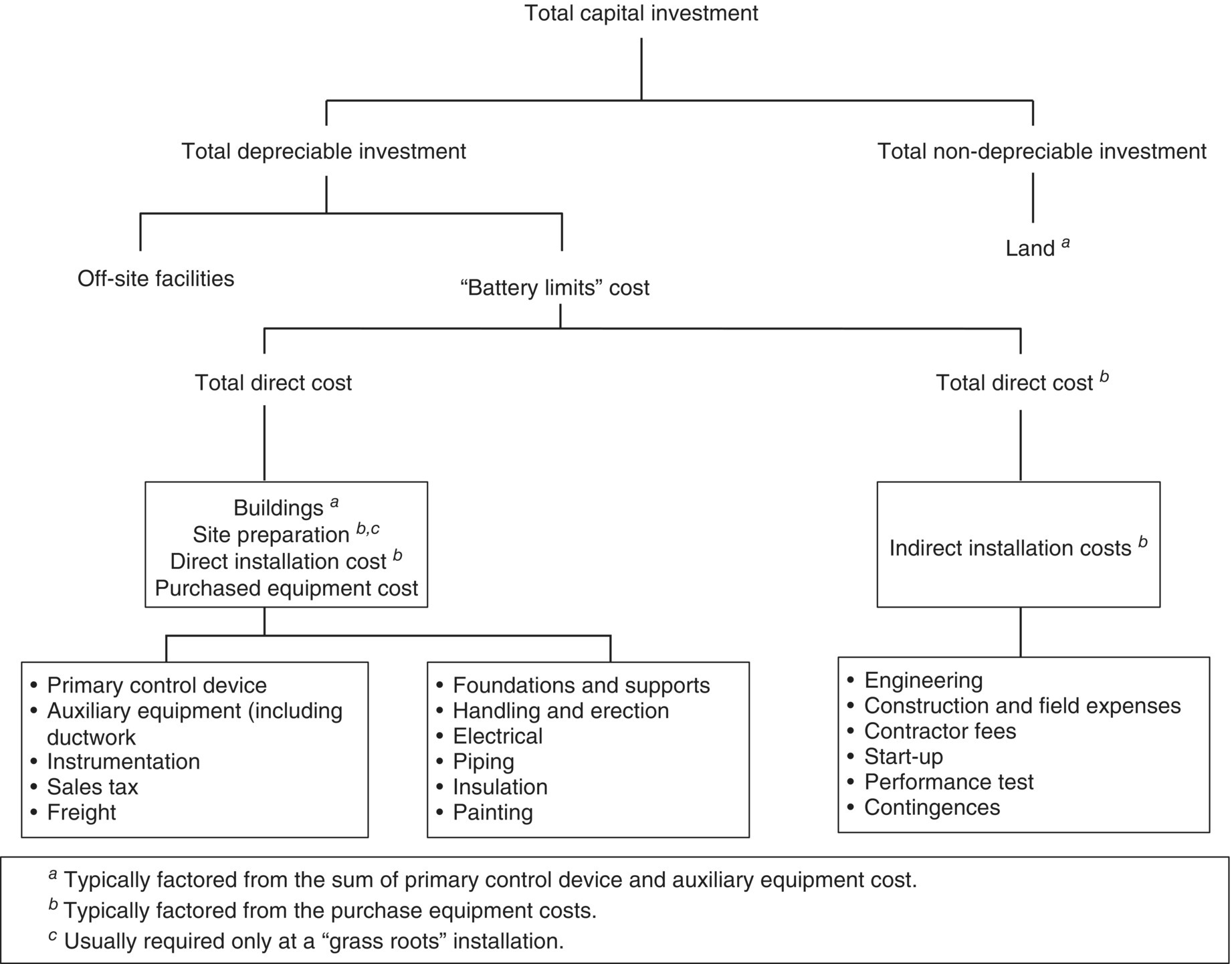
One might expect to include initial operational costs (the initial costs of fuel, chemicals, and other materials, as well as labor and maintenance related to start‐up) in the operating cost section of the cost analysis instead of in the capital component, but such an allocation would be inappropriate. Routine operation of the control does not begin until the system has been tested, balanced, and adjusted to work within its design parameters. Until then, all utilities consumed, all labor expended, and all maintenance and repairs performed are a part of the construction phase of the project and are included in the TCI in the “start‐up” component of the indirect installation costs.
Leave a Reply