Cold-chamber die casting is used for relatively high melting point non-ferrous alloys such as aluminium, magnesium, and brass which require higher pressure and temperature for melting. These metals are not melted in a self-contained pot as in hot-chamber die casting due to short life of pot (Figure 20.21). Therefore, the metal is melted in an auxiliary furnace and is ladled to the plunger cavity next to the dies. It is then forced into the dies under hydraulic pressure. The cold-chamber die casting machines operating by this method are built very strong and rigid to withstand the heavy pressure exerted on the metal as it is forced into the dies.
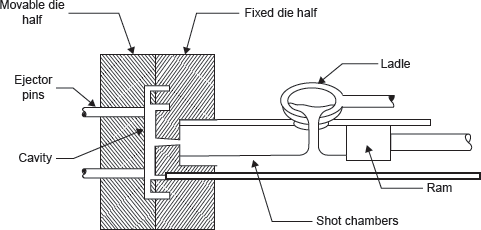
Figure 20.21 Cold-chamber Die Casting Machine
Advantages of Die Casting
- Production rate is very high.
- Parts have good dimensional accuracy and surface finish.
- Because of high pressure a thin wall up to 0.5 mm of casting can be produced.
- No riser is used due to use of high pressure injection of molten metal.
Limitations of Die Casting
- Die casting has a porosity problem as gases tend to be entrapped.
- The process is economical for large production run only.
Leave a Reply