Casting defects are unwanted feature or irregularities in casting which make it of poor quality. These defects occur due to several reasons such as poor design of casting, excess moisture in mould, improper ramming of moulding sand, misalignment of cope and drag, etc. The various types of casting defects are shown in Figure 20.27.
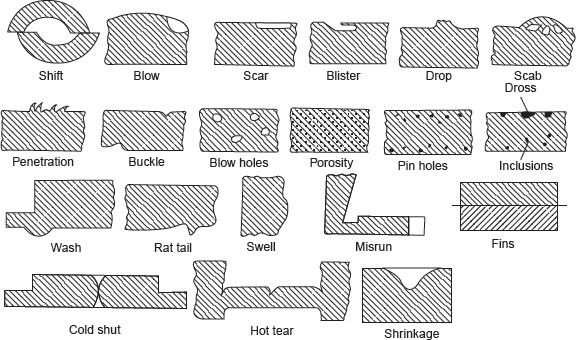
Figure 20.27 Casting Defects
Shifts: Misalignment of flask, i.e., cope and drag and mismatching of core cause shifts. These can be prevented by proper alignments and placing of core.
Blow: Blow is small, round holes appearing at the surface of the casting covered with a thin layer of metal.
Scar: It is shallow blow, which is usually found on a flat casting surface.
Swell: Swell is an enlargement of the mould cavity due to metal pressure. It is caused due to defective ramming of the mould. To avoid swells, the sand should be rammed properly and evenly.
Blister: This is scar covered by a thin layer of a metal.
Drop: When the upper surface of the mould cracks, and pieces of sand fall into the molten metal, this defect occurs. This is caused by low strength and soft ramming of sand, in sufficient fluxing of molten metal and insufficient reinforcement of sand projections in the cope.
Scab: Liquid metal penetrates behind the surface of mould. Scabs can be identified as rough, irregular projection on the surface containing embedded sand. They are caused using too fine sand, sand having low permeability and high moisture content, and by uneven mould ramming or slow running of molten metal over the sand surface thereby producing intense local heating.
Metal Penetration and Rough Surface: This defect appears as an uneven and rough external surface of the casting. The metal penetration between the sand grains occurs due to low strength, large grain size, high permeability, and soft ramming of sand.
Buckle: This defect is similar to the rat-tail but differs from it in the sense that it is in the form of V-shaped depression in the surface of the casting.
Blowholes: Blowholes are smooth, round holes appearing in the form of a cluster of a large number of small holes below the surface of a casting. Possible causes are excess moisture in the moulding sand, moisture on chills, chaplets, and insufficiently baked and improperly vented core.
Porosity: Porosity is entrapped gases in the form of fine small bubbles throughout the casting.
Pinholes: Pinholes are numerous small holes, usually less than 2 mm, visible on the surface of the casting cleaned by shot blasting. They are caused by sand with high moisture content, absorption of hydrogen or carbon monoxide gas, or when steel is poured from wet ladles.
Inclusions: Inclusion is mixing of foreign particles such as sand and slag in the casting.
Wash: It is a low projection on drag surface of a casting starting near the gate. This results due to displacement of sand by the high velocity metal in the bottom part of gating.
Rat Tails: These defects appear as streaks or slight ridges on large flat surfaces. They occur due to the expansion of sand by the heat of the molten metal.
Mis-run: A mis-run is the incomplete filling of the mould that results when the metal lacks fluidity or temperature.
Fins: Fins usually occur at the parting line of the mould or core sections due to improper clamping of flask. The remedy is to give sufficient weight on the top for proper assembly of the flasks and moulds.
Cold Shut: This type of mis-run occurs in the centre of a casting having gates at its two sides. Imperfect fusion is a result of low temperature of two streams of metal.
Hot Tears: They are internal and external cracks having a ragged edge occurring immediately after the metal has solidified. Hot tears may be produced if the casting is poorly designed and abrupt change in sections takes place, no proper fillets and corner radii are provided, chills are wrongly placed. Incorrect pouring temperature and improper placement of gates and risers are used.
Shrinkage Cavity: Shrinkage cavity is a void or depression in the casting caused mainly by uncontrolled solidification of the metal. They may also be produced if pouring temperature is high.
Leave a Reply