Limestones may be burnt in clamps or kilns. For kiln burning, an intermittent kiln or a continuous kiln may be used.
1. Clamp Burning
When the burnt lime required is small, this method may work out to be more economical. Further, this method can be adoptable in places where limestone and the fuel are available.
The clamp comprises of alternate layers of limestone and fuel. The fuel to be adopted in this case is wood. If the fuel is other than wood, viz., coal or charcoal, the fuel is mixed with the limestone and the clamp is formed. The clamp is of 3.6 m max height with sloped sides. The clamp is covered with mud plaster to prevent the escape of heat (Fig. 5.1).
Clamp burning has several disadvantages, viz., wastage of fuel, is uneconomical, is not a continuous process, can not be produced during the rainy season, etc.
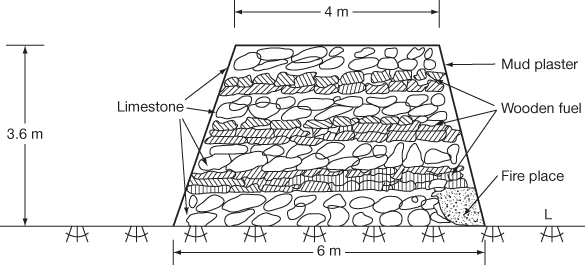
Figure 5.1 Clamp burning
2. Intermittent Kiln Burning
Various kinds of intermittent kilns are in practice, the most prevalent among them being the intermittent flame kiln and the intermittent flare kiln.
The intermittent flame kiln is similar to the clamp kiln. Here the limestone and fuel are arranged in alternate layers between two vertical walls. In some cases vertical flue is also provided. The top of the kiln is covered with unburnt material. The kiln is operated for three days. Then the kiln is cooled and unloaded and the process is repeated.
The intermittent flare kiln is one in which fuel is not allowed to come into contact with limestone. Big pieces of limestone are chosen, and a rough arch is formed over which small pieces of limestone are packed (Fig. 5.2).
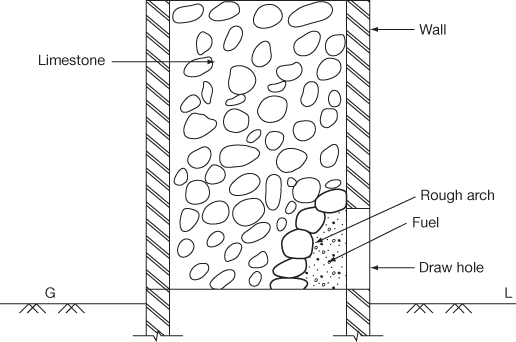
Figure 5.2 Intermittent flare kiln
The fuel is placed below the arch. When it is ignited, only the flame comes into contact with the limestone. After the limestone is adequately burnt, the kiln is cooled and unloaded. This process is then repeated.
This type of kiln is used only for the manufacture of lime on a moderate scale. The main drawback is the wastage of time for every operation.
3. Continuous Kiln Burning
This type of kiln is used when large quantities of lime is needed. In the conventional type, alternate layers of limestone and coal or wood are used. Feeding is done from the top, ignition is done from below, and the lime is collected at the bottom. Such a kiln does not produce high-purity lime as it gets mixed with ash of fuel (Fig. 5.3).
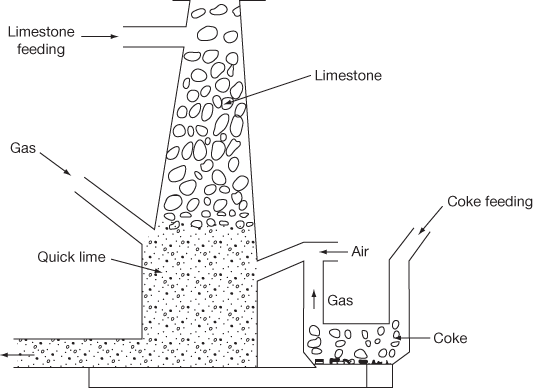
Figure 5.3 Continuous lime kiln
High-purity lime is prepared by using continuous separate feed kilns. The arrangement is shown in Fig. 5.3. Here the limestone is fed from the top and two or four fireplaces are provided by the side of the kiln near the bottom. Coal or wood is used as the fuel, and hot gases of combustion move up the shaft of the kiln. The use of wood as a fuel has an added advantage in that long flames are produced, and the temperature of limestone is not raised too much.
Leave a Reply