Wood
The era of aerospace materials arguably started with the first powered flight of Kitty Hawk by Orville and Wilbur Wright. The principal criterion used in the selection of materials for the first generation of aircraft (1903–1930) was maximum strength for minimum weight. Every other consideration in materials selection, including stiffness, toughness and durability, were secondary compared with the main consideration of high strength-to-weight. Weight had to be kept to an absolute minimum because of the low power (below 150 hp) of early aircraft engines. The airframes in the earliest aircraft were constructed almost entirely of wood because there were no other suitable materials that combined strength and lightness. The high-strength materials of the early 1900s, such as steel and cast iron, were about 10 times denser than wood and, therefore, too heavy for the airframe.
Wood was the material of choice in early aircraft because of its light weight, stiffness and strength (Fig. 2.3). Wood was also used because it was plentiful, inexpensive, and its properties were well understood through use in other structural applications such as buildings and bridges. Another important reason for using wood was the craftsmen who handbuilt the earliest aircraft were able to easily shape and carve timber into lightweight frames, beams and other structural components. However, wood is not the ideal material and has many inherent problems. The mechanical properties are variable and anisotropic which meant aircraft had to be over-designed to avoid structural damage. Many early aircraft experienced structural failures owing to inconsistent strength properties as the result of ‘soft’ or ‘weak’ spots in the wood. Furthermore, wood absorbs moisture, warps and decays over time, which meant that aircraft required continuous maintenance and on-going repairs.
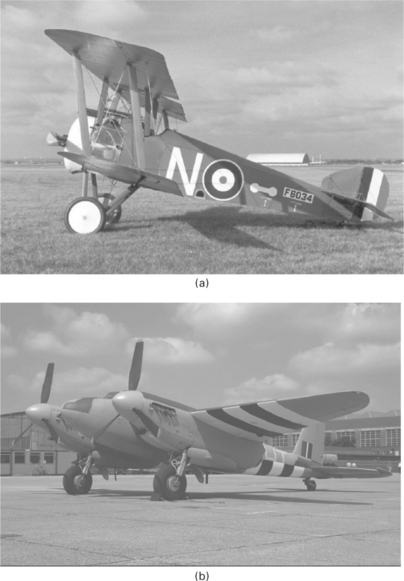
2.3 Wooden aircraft. (a) Sopwith Camel. Photograph supplied courtesy of the National Museum of the US Air Force. (b) de Havilland Mosquito. Photograph supplied courtesy of M. J. Freer.
The first generation of aircraft builders evaluated many types of timber, and found that fir, spruce and several other softwoods were best suited for making structural components with a high ratio of strength-to-weight. The aircraft industry later discovered that laminated plywood construction provided greater strength and toughness than single-piece wood. Laminated plywood consists of thin bonded sheets of timber orientated with the wood grain at different angles. The use of plywood reduced the weight penalty experienced with one-piece timber construction that had to be over-designed. As a result plywood rapidly gained popularity as a structural material in the period between the two world wars. Even during the World War II some fighters and light bombers were constructed from wood and plywood. Probably the most famous wooden aircraft during the war was the de Havilland Mosquito, which, for its time, was a highly advanced fighter/bomber capable of flying at 650 km h− 1.
The large-scale production of fighters, bombers and heavy load transport aircraft during World War II led to the demise of wood as an important structural material. Abundant supplies of high quality timber were not available to many countries during the war, which forced the greater use of alternative materials such as aluminium. Also, wood lacks the stiffness and strength required for many military aircraft, particularly bombers, cargo transporters and other heavy lift aircraft that have high loading on their wings and airframe. The use of wood continued to decline in the post-war era with the development of pressurised cabins for high-altitude flying. Today, few aircraft are constructed using wood, except for some gliders, ultra-lights and piston-driven aircraft, because cheaper, lighter and more structurally efficient materials are available.
Aluminium
The development of aircraft with greater engine power during the 1920s placed increased demands on wood construction that it struggled to meet. The loads on the wings and airframe increased as aircraft became larger and heavier. The wing loading on aircraft built during the 1910s was 30–40 kg m− 2, which could be supported using wooden frames. However, the construction of larger, heavier aircraft in the following decades increased pressure loading on the wings to 500–1000 kg m− 2. Figure 2.4 shows the general trend towards higher wing loads for military aircraft and passenger airliners over the past century. Loads on other parts of the aircraft, particularly the fuselage and tailplane, have also increased. Wood lacks the stiffness, strength and toughness to withstand high loads, and aircraft builders sought other lightweight materials with better structural properties.
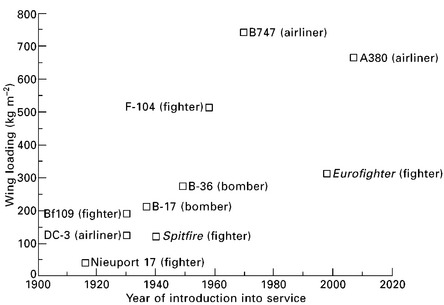
2.4 Plot of wing pressure load against year of introduction for several fighters, bombers and airliners.
With steel being too heavy, the aircraft industry in the 1920s turned to aluminium alloys as a replacement for wood. Aluminium is one of the lightest metals; being about 2.5 times lighter than steel. It is stiffer, stronger, tougher and more durable than timber. Also, aluminium can be easily fabricated into thin skin panels and readily machined into spars, stiffeners and beams for the fuselage and wings.
Aluminium had been available in commercial quantities to aircraft manufacturers since the early 1900s, but it was too soft. Aluminium was first used in the airframe of Zeppelin airships during World War I, but it lacked the strength to be used in fixed-wing aircraft that are more heavily loaded. Metallurgists during the early decades of the twentieth century improved the strength properties of aluminium by the addition of alloying elements and development of heat-treatment processes. Various types and amounts of alloying elements were added to aluminium using a trial and error approach to assess the effect on strength. The metals industry experimented with many alloying elements to increase strength and hardness. The industry also tested different heat treatments and metal-forming processes to improve the mechanical properties. A major breakthrough occurred when the addition of a few percent of copper and other alloying elements was found to increase the strength by several hundred percent. The development of the aluminium alloy ‘Duralumin’ in 1906 was largely responsible for the uptake of aluminium by the aircraft industry from the 1920s. Duralumin is an aluminium alloy containing copper (4.4%), magnesium (1.5%) and manganese (0.6%) which is strengthened by heat treatment. Duralumin sparked an explosion in the use of aluminium in highly-stressed aircraft structures, such as the skins, ribs and stiffeners in the wings and fuselage. The use of aluminium also provided the capability to increase the speed, range and size (payload) of aircraft over that possible with wood.
Following the initial success of Duralumin, the mechanical properties of aluminium alloys improved dramatically in the era between the two world wars owing to on-going research and development. From the 1950s, there was a much better understanding of the effects of alloy composition, impurity control, processing conditions and heat treatment on the properties of aluminium. Figure 2.5 shows the sustained improvement in the strength of aluminium alloys since the 1920s. Similar improvements have been achieved with other important properties, including longer fatigue life, greater fracture toughness and damage tolerance, and better corrosion resistance. These developments have been driven largely by the demands of the aerospace industry for more structurally efficient materials. Other major advances in aluminium technology occurred in the 1960s/70s when Al–Li alloys, which have higher stiffness and lower weight than conventional alloys, were developed. New heat-treatment processes developed in the 1970s/80s resulted in better toughness, damage tolerance and corrosion resistance.
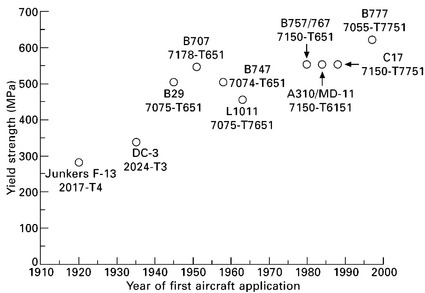
2.5 Yield strength of aluminium alloys and the year of introduction into service.
Aluminium is the material of choice for most aircraft structures, and typically accounts for 70–80% of the structural weight of most commercial airliners and over 50% of military aircraft and helicopters. In recent years, however, the percentage of airframe weight consisting of aluminium has declined owing to greater use of carbon fibre-polymer composites. Figure 2.6 shows the recent decline in the use of aluminium in airliners owing to greater usage of composite materials in the fuselage, wings and other major structures. Despite this drop, aluminium will remain an important structural material for both aircraft and helicopters.
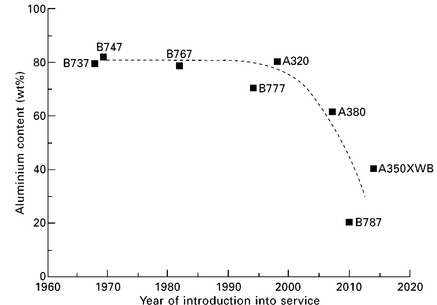
2.6 Decline in use of aluminium in passenger aircraft.
2.2.3 Magnesium
Like aluminium, magnesium has been used for many years as an airframe material because of its low weight. Magnesium is lighter (by nearly 40%) than aluminium, although it has never been a serious challenger to aluminium because of its higher cost and inferior structural properties. Magnesium alloys have lower stiffness, strength, fatigue resistance and toughness than the types of aluminium used in aircraft. The greatest problem with magnesium is poor corrosion resistance. Magnesium is highly susceptible to various forms of corrosion, and when used in aircraft requires corrosion protective coatings and regular inspections for corrosion damage.
Magnesium was first used in German military aircraft during World War I and used extensively in German and Japanese aircraft during World War II owing to limited supplies of aluminium. The use of magnesium reached its peak in the 1950s and 60s, and, since the early 1970s, usage has declined and now it is used sparingly (under 1–2% by weight) in modern aerostructures owing to corrosion problems and low mechanical properties. For example, Fig. 2.7 shows the fall in the use of magnesium in Russian-built Tupolev aircraft over the past fifty years, and this reflects the general reduction in magnesium usage in many aircraft types. Magnesium remains a useful material in aircraft and helicopters even though its usage is low, and it is unlikely to be completely eliminated from aircraft.
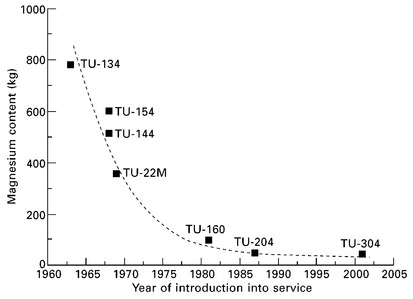
2.7 Decline in use of magnesium with successive versions of Tupolev aircraft since the 1960s, reflecting its general decline as an aerospace structural material.
Titanium
Titanium was first used in military and commercial aircraft during the 1950s. The original need for titanium arose from the development of supersonic aircraft capable of speeds in excess of Mach 2. The skins of these aircraft require heat-resistant materials that do not soften owing to frictional heating effects at supersonic speeds. Conventional aluminium alloys soften when the aircraft speed exceeds about Mach 1.5 whereas titanium remains unaffected until Mach 4–5. The USAF developed the SR-71 Blackbird with an all-titanium skin construction in the mid-1960s (Fig. 2.8). The SR-71 was a high-altitude reconnaissance aircraft with a maximum speed in excess of Mach 3, and, at the time, was one of the world’s most sophisticated and fastest aircraft. The SR-71 demonstrated the application of titanium in airframe structures. Titanium is stiffer, stronger and more fatigue resistant than aluminium, and for these reasons it has been used increasingly in heavily loaded structures such as pressure bulkheads and landing gear components.
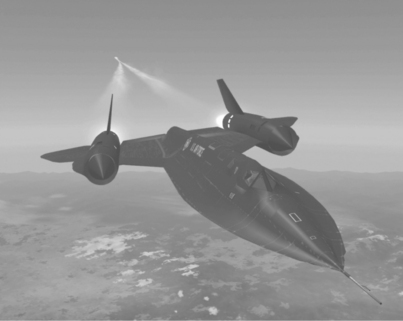
2.8 SR-71 supersonic aircraft contain large amounts of titanium in the airframe.
The use of titanium in commercial aircraft has increased over recent decades, albeit slowly owing to the high cost of titanium metal and the high costs of manufacturing and machining titanium components. Although the mechanical properties of titanium are better than those of aluminium, the material and manufacturing costs are much higher and it is uneconomical to use in structural components unless they need to be designed for high loads. For this reason, the structural weight of titanium in airliners is typically under 10%, although higher amounts are used in new aircraft types such as the Airbus 350 and Boeing 787 as shown in Fig. 2.9. Titanium usage is greater in fighter aircraft because the loads on the wings and fuselage are higher and the cost is less critical in materials selection. Titanium is also used in gas turbine engine components required to operate at temperatures of 450–500 °C. Titanium has high static, fatigue and creep strengths as well as excellent corrosion resistance at elevated temperatures, which makes it suitable for jet engines. Titanium engine components include fan blades, guide vanes, shafts and casings in the inlet region; low-pressure compressor; and plug and nozzle assemblies in the exhaust section. Titanium alloys account for 25–30% of the weight of many modern jet engines.
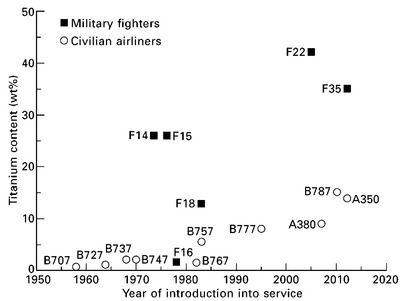
2.9 Amount of titanium used in aircraft.
Superalloys
The development of aircraft, helicopters and rockets is reliant on the development of materials for gas turbine engines or rocket motors that can operate at high temperatures for a long time without softening or degrading. Superalloys are an important group of high-temperature materials used in the hottest sections of jet and rocket engines where temperatures reach 1200–1400 °C. Superalloys are based on nickel, cobalt or iron with large additions of alloying elements to provide strength, toughness and durability at high temperature.
Since the introduction of jet engines in the post-World War II period the aerospace industry has invested heavily in alloy development, metal-casting processes, and metal-forming technologies to raise the maximum operating temperature of superalloys. The need to improve the efficiency and thrust of engines has resulted in an enormous increase in the temperature at the entry of the high-pressure turbine section. This temperature has risen over the past sixty years from 800 to 1600 °C, and future engines will probably be required to operate at about 1800 °C. These increases are only possible with the development of materials capable of operating for long periods at extremely high temperatures. Figure 2.10 shows the general trend for improvement in the operating temperature limit (creep strength) of nickel-based superalloys used in high-pressure turbine blades since the late-1960s. Advances in alloy composition, impurity control and casting technology (including the development of directional solidification and single crystal casting methods) together with the development of thermal ceramic coatings for superalloys have increased greatly the maximum operating temperature, thus resulting in increased engine performance by raising the power-to-weight ratio and fuel economy. Fuel consumption is an important metric in evaluating the operational efficiency of an airliner, and Fig. 2.11 shows the improvement in the fuel economy since the late 1950s. Over the fifty-year period, fuel consumption of engines has dropped by 50% and the aircraft fuel burn per seat has fallen over 80%. Continuous advances in the main factors that affect fuel burn rate, viz, airframe design, engine design, flight control and navigation, and advanced materials, have led to large improvements in fuel economy. Not only does this cut the operating cost of aircraft, but it also reduces greenhouse gas emissions and other pollutants owing to lower fuel consumption.
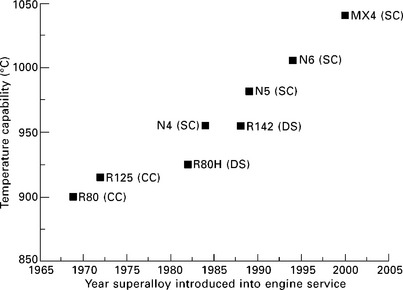
2.10 Improvement in the temperature capability (creep strength) of nickel superalloys used in jet engines since the late 1960s. The alloy type and casting methods (CC = chill casting; DS = directional solidification casting; SC = single-crystal casting) are given.
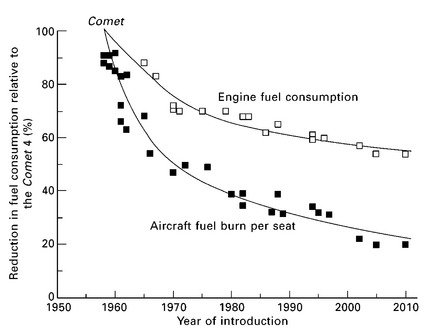
2.11 Reductions in the engine fuel consumption and aircraft fuel burn per seat based on the Comet 4 aircraft.
The durability and operating life of engine components have also improved dramatically in recent decades owing to advances in their materials. For example, when the Boeing 707 entered service in 1958, the engines were removed for maintenance after about 500 h of operation. Most of the maintenance related to deterioration of the high-pressure turbine blades that were made of early versions of superalloys. Today, a Boeing 747 class engine can operate for 20 000 h without major maintenance. This remarkable improvement is in part the result of advances in the metallurgy of nickel-based superalloys and other high-temperature materials, including ceramic coatings.
2.2.6 Composite materials
Fibre-reinforced polymer composites are another important group of aerospace materials that have a long history of usage. Composites were first used in the 1940s for their high strength-to-weight ratio and corrosion resistance. The first generation of composite material consisted of glass fibres in a low-strength polymer matrix. The potential application of this material was demonstrated during the late 1940s and 1950s in various prototype aircraft components and filament-wound rocket motor cases. However, the aerospace industry was initially reluctant to use composites in large quantities because the original fibreglass materials were expensive to produce; difficult to manufacture with a high degree of quality control; their mechanical properties were inconsistent and variable owing to inadequate processing methods; and they were prone to delamination cracking when subjected to impact events such as bird strike. Furthermore, the elastic modulus of fibreglass composite is low and therefore it is not suitable in structural applications that require high stiffness. Composites were gradually introduced into semistructural aircraft components during the 1950s and 1960s, such as engine cowlings and undercarriage landing gear doors, to reduce weight and avoid corrosion.
The evolution of primary aircraft structures from aluminium to composite has been slow owing to the commercial risk involved with making the change. The aerospace industry, particularly those companies producing civil aircraft, is conservative owing to the financial and safety risk of changing structural materials. The industry recognised that the changeover from aluminium to composite may possibly provide benefits such as increased airframe life and reduced production costs and weight, but none of these were guaranteed. Furthermore, the transition from metals to composites requires a complete change of production facilities, which comes at huge expense. Aluminium remains a satisfactory material, despite problems with fatigue and corrosion, and the strong incentive to replace this material with composite was lacking for many years. Furthermore, the large weight savings attributed to composites are not always achieved, and often the reduction in mass achieved by replacing aluminium with composite has been modest.
A major change in the use of composite material occurred in the 1960s with the commercial production of carbon fibres. Carbon-fibre composites are lightweight, stiff, strong, fatigue resistant and corrosion resistant, and for these reasons their potential application in both airframes and engines was immediately recognised by the aerospace industry. However, the high cost of carbon fibres, poor understanding of the design rules, structural properties and durability together with technical challenges in certification meant that the initial use of carbon-fibre composites was small. Until the 1970s, the use of carbon-fibre composites was limited to semistructural components which accounted for less than 5% of the airframe weight. Corrosion problems with aluminium and the OPEC energy crisis in the 1970s were incentives for the aerospace industry to expand the use of carbon-fibre composites in both fighter aircraft and commercial airliners. As design methods and manufacturing processes improved and the cost of carbon fibre dropped the amount of composite material used in aircraft increased during the 1980s and 1990s, as shown in Fig. 2.12.
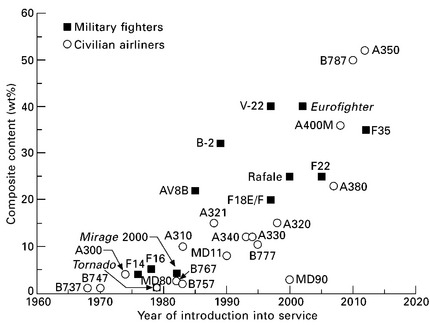
2.12 Amount of composite materials used in aircraft.
Major milestones in the use of carbon-fibre composites were applications in primary structures of fighter aircraft such as the Harrier (AV-8B) and Hornet (F-18) and in the tail section of the Boeing 777 in the 1990s. The use of composites in the fuselage and wings of modern airliners such as the A380, A350 and B787 are recent major events. The use of carbon-fibre composites in helicopter components, such as the body, tail boom and rotor blades, has also increased dramatically since the 1990s. Composites are the first material since the 1930s to seriously challenge the long-held dominant position of aluminium in airframe construction, and the competition between these two materials is likely to be intense in coming years.
Composite materials are increasingly being used in low-temperature components in jet engines because of their light weight. Carbon-fibre composites were first used in gas turbine engines in the 1960s for their light weight and high mechanical properties. Because of their low softening temperature, however, composites can only be used in low-temperature engine components such as the air inlet fan where the temperature remains below 180–200 °C. An early engine application for carbon-fibre composites was in fan blades in the Rolls-Royce RB-211 high-bypass turbofan, which was designed in the late 1960s for aircraft such as the Lockheed L-1011 (TriStar). Unfortunately, Rolls-Royce pushed the state-of-the-art with carbon-fibre composites too far because the blades were vulnerable to damage from bird impact and there were manufacturing problems. This combined with other technical problems and major cost blow-outs in the development of the RB-211 caused Rolls-Royce to become insolvent in 1971 and the company was nationalised by the UK Government. This incident demonstrates the serious problems that can occur when new materials are introduced into critical aircraft components before their capabilities are fully characterised and certified. Despite this initial set-back, major aircraft engine manufacturers continued to develop composite components during the 1970s/1980s, and in recent years carbon-fibre materials have been used reliably in fan blades and inlet casings. The use of composites is expected to increase further in coming years with the development of higher-temperature polymers and improvements in impact damage tolerance.
Other types of composites have been developed for airframe and engine applications, although their usage is much less than that of polymer matrix materials. Metal matrix composites (MMC) were first developed in the 1950s/60s to improve the structural efficiency of monolithic metals such as aluminium. MMCs are composed of a hard reinforcing phase dispersed in a continuous metal matrix phase. The reinforcement is often a ceramic or man-made fibre (boron, carbon) in the form of small particles, whiskers or continuous filaments. The development of MMCs resulted in materials that are stiffer, harder, stronger and, in some cases, lighter and more fatigue resistant than the base metal. Early applications of MMCs included fuselage struts in the space shuttle orbiter, ventral fins and fuel access doors in the F-16 Fighting Falcon, and main rotor blade sleeves in some helicopters. The use of MMCs in jet engines has been evaluated, but, to date, the applications are limited to components such as fan exit guide vanes in specific engine types and they are not widely used in large-scale commercial production of engine parts. MMCs have largely failed to make a major impact in structural or engine applications. During the development of MMCs it became obvious that these materials are expensive to produce; difficult to forge, machine and join; and have low ductility and toughness; and for these reasons they are not often used.
Ceramic matrix composites (CMCs) are another class of composite material introduced into aircraft and spacecraft in the 1970s. CMCs consist of ceramic reinforcement embedded in a ceramic matrix. CMCs were developed for high-temperature applications which require materials with higher strength and toughness than conventional monolithic ceramics. The most famous CMC is reinforced carbon–carbon which gained fame through its use in heat shields on the space shuttle, brake discs for aircraft, and engine nozzle liners for rockets and missiles.
Fibre-metal laminates (FML) were developed as damage-tolerant composite materials for aircraft structures during the 1980s. The original FML was called ARALL, which consists of thin layers of aramid fibre composite sandwiched between layers of aluminium alloy. Difficulties with manufacturing and problems with moisture absorption lead to the development of an alternative FML known as GLARE, which comprises alternating layers of fibreglass composite and aluminium. GLARE has higher strength, fatigue resistance, damage tolerance and corrosion durability than monolithic aluminium, and was first used widely in the upper fuselage of the Airbus 380 and later in cargo doors for the C-17 Globemaster III heavy-lift transporter. The future of FMLs in other large aircraft is uncertain owing to high production and manufacturing costs.
Leave a Reply