Black liquor is a biomass feedstock with unique properties suitable for gasification (Ǻdahl et al. 2004; Andersson and Harvey 2004; Bajpai, 2008, 2013; Berglin et al. 2002; Dahlquist et al. 2009; Grigoray 2009; Marklund 2006; Salomonsson, 2013; Sricharoenchaikul 2009, 2001; Waldner and Vogel 2005; Wikipedia 2016). First of all, it is available at existing industrial sites in large quantities. Second it is liquid. This makes it possibly to easily feed it by pumping into the pressurized gasifier. The liquid state also makes the black liquor easy to atomize into a fine mist that reacts very fast in the gasifier. Third, the gasification of black liquor char is more rapid than for any other feedstock as the inherently high sodium and potassium content of black liquor acts as a catalyst. These properties make it possible to apply the high temperature, entrained flow gasification principle to black liquor. This type of gasification process provides many advantages over alternative gasification technologies. It is very rapid, single‐stage gasification process with low reactor volume, and low emissions (including particulate matters and odorous TRS gases) and low power consumption.
Black Liquor Properties
The black liquor is an aqueous solution of lignin residues, hemicellulose, and the inorganic chemicals used in the process. The black liquor is sent through a series of evaporators to increase the solid content in order to make it suitable for combustion. In the evaporators, the BLS content is increased from about 15 wt% to about 70–75 wt%. The concentrated black liquor that goes into the recovery boiler consists of about 30% water, 30% valuable inorganic cooking chemicals, and 40% lignin and other organic matter separated from the wood. The higher heating value is about 14 000 kJ/kg solids. Typically, a large pulp‐mill will produce about 200 T/day of black liquor corresponding to about 300 MWh (Bajpai 2014).
The organic matter in the black liquor is made up of water/alkali soluble degradation components from the wood. Lignin is degraded to shorter fragments with sulfur content at 1–2% and sodium content at about 6% of the dry solids. Cellulose and hemicellulose is degraded to aliphatic carboxylic acid soaps and hemicellulose fragments. The extractives gives tall oil soap and crude turpentine. The soaps contain about 20% sodium. Table 9.4 presents some properties of black liquor.
BLG Technologies
BLG may be performed either at low temperatures or at high temperature based on whether the process is conducted above or below the melting temperature range (650–850 °C) of the spent pulping chemicals (Sricharoenchaikul 2001).
- Low‐temperature gasification – Low‐temperature gasifier operates at 600–850 °C, below the melting point of inorganics, thus avoiding smelt–water explosions.
- High‐temperature gasification – High‐temperature gasification units generally operate in the 900–1000 °C range and produce a molten smelt.
In low‐temperature gasification, the alkali salts in the condensed phase remain as solid products, while molten salts are produced in high‐temperature gasification. Low‐temperature gasification is advantageous over high‐temperature gasification because gasification at low temperature yields improved sodium and sulfur separation. Additionally, low‐temperature gasification requires fewer constraints for materials of construction because of the solid product. However, syngas of low‐temperature gasification may contain larger amounts of tars, which can contaminate gas cleanup operations in addition to contaminating gas turbines upstream of the gasifier. These contamination problems can result in a loss of fuel product from the gasifier (Patrick and Siedel 2003; Sricharoenchaikul 2001).
Several companies have performed trials to develop a commercially feasible process for BLG. History of BLG development is very well described by Whitty and Baxter (2001) and Whitty and Verrill (2004). In the search for alternative ways to recovering the cooking chemicals, gasification techniques have been thoroughly examined several times. In total, more than 20 different technologies have been investigated over the years (Swedish Energy Agency 2008). The most interesting attempts of accomplishing low‐temperature black liquor gasification (LTBLG) and high‐temperature black liquor gasification (HTBLG) processes are presented in Table 9.5. Only two technologies are currently being commercially pursued: the MTCI (Manufacturing and Technology Conversion International Company, low temperature) and Chemrec (high temperature) technologies. A pressurized, oxygen‐blown, HTBLG technology, shown in Figure 9.18, is being developed by Chemrec, a Swedish company (Chemrec 2006; Whitty 2006; Whitty and Nilsson 2001). Table 9.6 gives the difference between these two technologies.
Table 9.4 Properties of black liquor.
Density (50% solids) at 93 °C | 1.26 g/cm3 |
Viscosity (50% solids at 121 °C) Viscosity (70% solids at 125 °C) | 5.0 and 100.0 cP |
Specific heat (40% solids) | 2.0 KJ/(kg·K) |
Heating value (35% lignin and 70% solids) | ~14 000 kJ/kg |
Table 9.5 Black liquor gasification processes.
Source: From Whitty and Verrill (2004), Grigoray (2009), Naqvi et al. (2010), and Swedish Energy Agency (2008).
SCA‐Billerud process |
Copeland process |
Weyerhaeuser’s “dry pyrolysis” process |
St. Regis hydropyrolysis process |
The Texaco coking process |
VIT circulating fluidized gasification process |
Babcock & Wilcox’s bubbling fluidized bed gasification process |
NSP or Ny Sodahus process |
DARS process (Direct Alkali Recovery System) |
ABB circulating fluidized bed gasification process |
MTCI/TRI’s fluidized bed steam reforming process |
Kellogg, Brown, and Root’s spouting and transport fluidized bed gasifiers |
Paprican’s AST process |
University of California’s “pyrolysis, gasification, combustion” process |
The Champion–Rockwell molten salt gasification process |
The SKF plasma black liquor gasifier |
Ahlstrom’s suspension gasifier |
Tampella’s entrained flow gasifier |
Noell’s entrained flow gasifier |
Champion–Rockwell molten salt gasification process |
Chemrec entrained flow gasification process |
Catalytic hydrothermal gasification of black liquor |
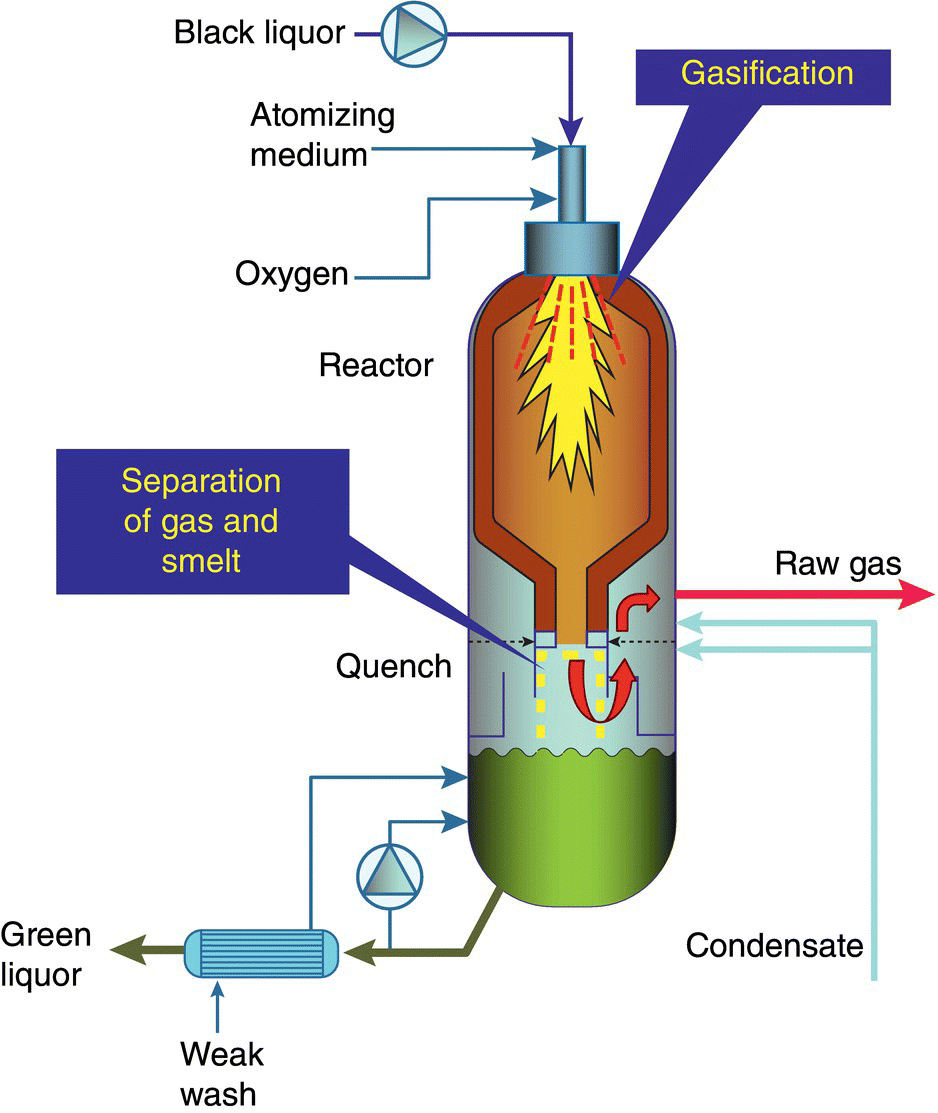
Table 9.6 Difference between LTBLG and HTBLG.
Source: From Swedish Energy Agency (2008).
Property | LT (TRI) | HT (Chemrec) |
Heating | Indirectly (syngas) | Directly (black liquor) |
Chemical recovered | Solid phase | Smelt |
Sulfur split (gas/smelt) | 90/10 | 50/50 |
Syngas composition | High H2 concentration | Moderate H2 concentration |
Syngas energy content | High | Low |
Leave a Reply