The USEPA recently completed a study of the proprietary Picklex process. Picklex® is a “‘non‐polluting’ pretreatment/conversion coat which replaces chromate conversion coating and zinc & iron phosphatizing in powder coating, paint and other organic finish applications” (Ferguson and Monzyk 2003; Ferguson et al. 2001).
Description
Metal pretreatment is crucial for cleaning and oxide removal to obtain proper performance and durability of the produced part, and it usually involves many tanks with various purposes. For example, aluminum anodizing may require eight pretreatment tanks; in conventional chromate conversion coating, there are twelve stages, while conventional zinc phosphatizing requires six. All of these baths contain heavy metals and must be dumped periodically.
The volume of hazardous/toxic waste streams produced from metal surface–finishing operations is significant (USEPA 1995a). The elimination of any of the surface‐processing steps is beneficial to the manufacturing process because it reduces processing costs, waste production, and energy consumption. Strong acids used in the pretreatment of metals pose a great health and safety risk to workers. With this in mind, a no‐waste or waste‐reducing surface‐finishing agent designed to lower processing costs for metal‐finishing operations would be of great benefit.
The Picklex process (a proprietary process) is one such alternative to conventional metal surface pretreatment that offers significant reductions in waste generation. The process was developed by International Chemical Products, Inc. with assistance from the USEPA. The Picklex process works in a completely different way than conventional processes. It incorporates the corrosion products from the metal surface into the protective coating that is applied to that same metal surface. This new P2 approach “thinks outside the box” by solving the common environmental problem of metal buildup in the processing tanks while forming a protective surface coating on the work piece. A two‐phase program was undertaken to evaluate the ability of Picklex to perform technically and economically as a pollution prevention–based replacement for conventional metal pretreatment or pretreatment/conversion coat in finishing operations. The goal was to demonstrate its potential to eliminate or significantly reduce the amount of hazardous and toxic chemicals consumed and the amount of pollution generated while maintaining equal or better product performance properties.
A broad laboratory evaluation of Picklex was undertaken in which full multistep, bench‐scale, batch operation tests using side‐by‐side test lines of seven conventional processes and of Picklex were performed. The results of the laboratory tests were quite favorable, and field tests (Ferguson and Monzyk 2003) were conducted to evaluate in‐plant performance in side‐by‐side tests with conventional preparation technologies. Only the most promising applications – the replacing of chromate conversion coating and zinc phosphatizing – were taken to field evaluation. In these focused field tests, Picklex was used to prepare aluminum and steel substrates for powder coating only. Although the testing scope was narrowed, it was more detailed. A total of 41 different combinations of substrate, degreaser, pretreatment, conversion coat, and powder coat were tested in the field evaluation. Only uncontaminated panels and components, without corrosion products, were used. The results for all test cases demonstrated that the quality of the final product was equal in all respects to conventional practice. Product quality was targeted as the single most important acceptance criterion within all the comprehensive results, because if the final product quality was not acceptable, the pollution reductions would not matter. The field test results replicated those obtained earlier, indicating that the lab testing may be used to accurately predict results achievable in practice.
Environmental Benefit
Two commercial processes, chromate conversion coating and zinc phosphatizing, were employed in the field tests as the experimental control baseline (Figures 7.3 and 7.4, respectively). Metal buildup in these conventional processes ruined the baths, and the baths had to be dumped. In the metal‐finishing sector, the discarding of such metal‐containing waste streams is a major contributor to pollution. The Picklex chemical used in the process tank is used up on the product; however, with filtering, the bath does not become contaminated. As a result, it is not necessary to dump the bath to control impurity buildup, and the chemical make‐up is simply added to the bath as needed. This process was demonstrated to have a strong potential as a leading technology for pollution prevention in surface preparation operations.
As can be seen in the comparison of the conventional practices to this emerging technology, the Picklex process eliminates up to eleven steps in metal‐finishing processes. The reductions of waste at the source were very significant. These reductions were accomplished by the elimination of the hexavalent chromium tank and subsequent rinsing operations; the elimination of the acid baths used for etching and cleaning along with subsequent rinsing operations; the elimination of the zinc phosphatizing baths and subsequent rinsing operations; and the elimination of the deoxidizing bath and subsequent rinses. All of the steps eliminated are steps that emit pollution. In addition, the Picklex process significantly reduces the pollution from the remaining steps. It does this while providing the same high‐quality finish and wear resistant capabilities as the conventional processes.
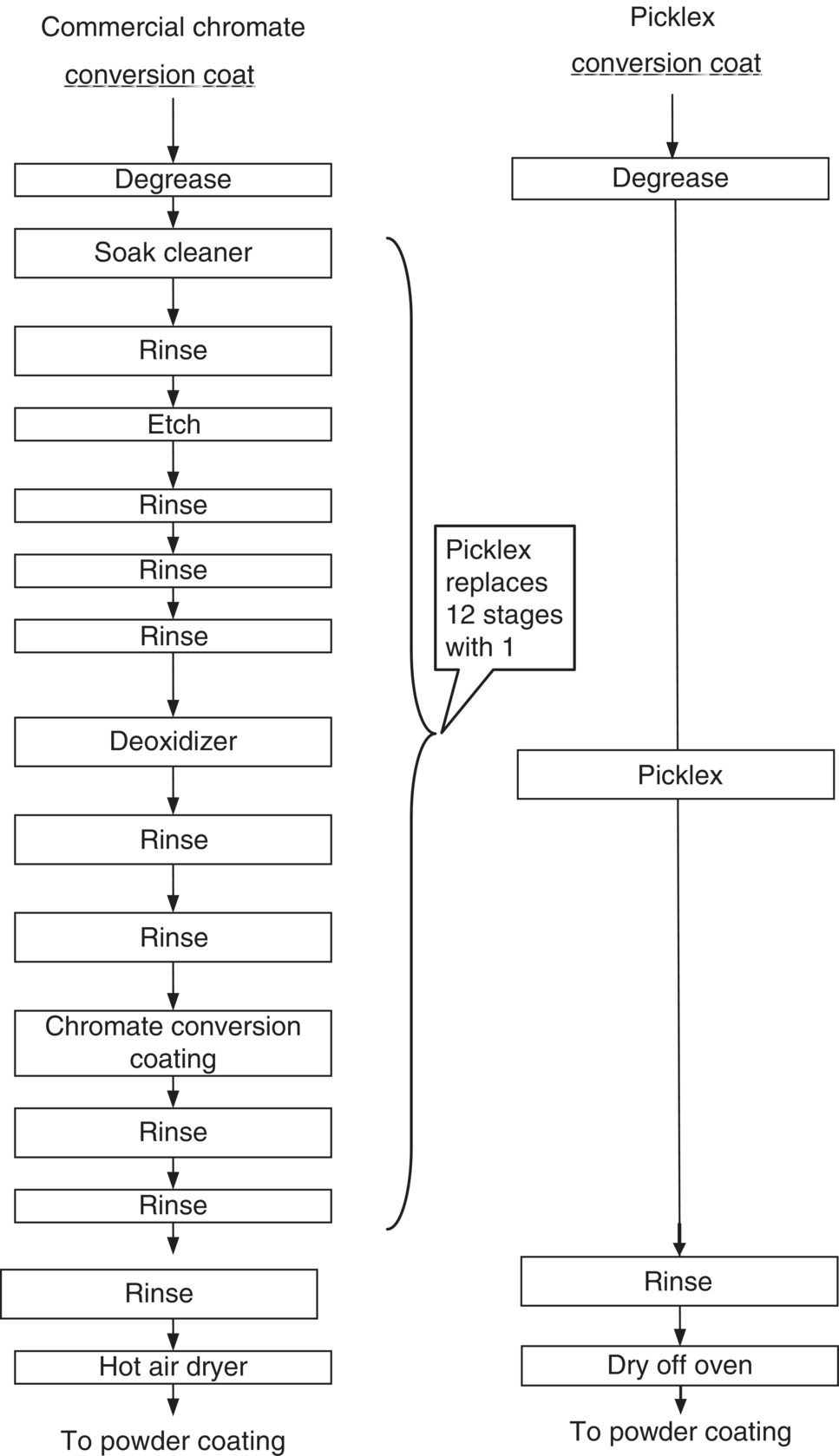
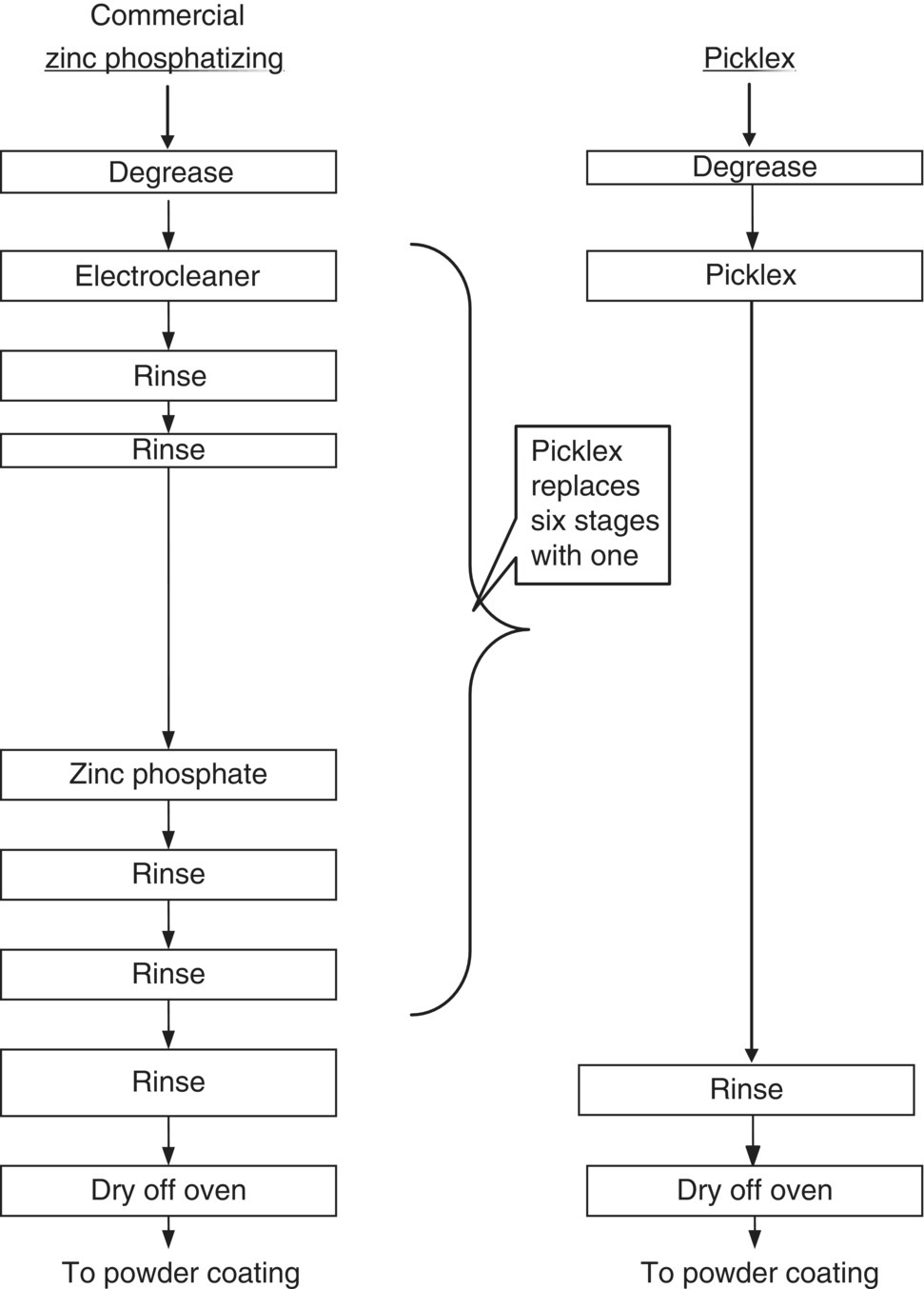
Although normally the Picklex bath does not need to be dumped, but, as part of the study, the bath was evaluated for waste treatment issues in the event of a spill or accidental contamination. Fresh, spent, and impurity‐spiked spent Picklex samples were treated using the conventional pH 9 precipitation industrial wastewater treatment method to produce samples for a waste disposal assessment for Picklex. The waste solids were assessed for toxic leachability. The treated water supernatants for discharge were also examined and found as most likely dischargeable. Waste treatment may not be frequent or necessary in many processes. Actual discharge limits from industrial waste treatment plant operations are site‐specific and are determined on a case‐by‐case basis with local, state (and federal only where necessary) regulatory agencies. Hence, no exact classification of these potential waste solutions is possible until a specific location is known. All leachates are passed with respect to the applicable federal regulations (USEPA 1995b). Therefore, Picklex does not appear to present unusual waste treatment issues.
Leave a Reply