The 2000, 6000, 7000 and many 8000 alloys can be strengthened by age-hardening. It is only by age-hardening that aluminium alloys obtain the strength needed for use in highly loaded structures and, therefore, this process is critical in the construction of aircraft. We first examine the composition and uses of the age-hardenable alloys used in aircraft, and then examine the age-hardening process.
2000 series aluminium alloys (Al–Cu)
The 2000 alloys are used in many structural and semistructural components in aircraft. The main alloying element is copper, which readily forms high-strength precipitates when aluminium is age-hardened by heat treatment. 2000 alloys are characterised by high strength, fatigue resistance and toughness. These properties make the alloys well suited for fuselage skins, lower wing panels and control surfaces.
There are many types of 2000 alloys, but only a few are used in aircraft structures. One of the most common is 2024 Al (Al–4.4Cu–1.5Mg), which has been used for many years in aircraft structures such as stringers, longerons, spars, bulkheads, carry-throughs, stressed skins and trusses. 2000 alloys are used in damage-tolerant applications, such as lower wing skins and the fuselage structure of commercial aircraft which require high fatigue resistance. The alloy is also used in nonstructural parts such as fairings, cowlings, wheel pants and wing tips. Newer alloys are being introduced with superior properties to 2024 Al. For instance, 2054 Al is 15–20% higher in fracture toughness and twice the fatigue resistance of 2024 Al. Other 2000 series used in aircraft include 2018 Al, 2025 Al, 2048 Al, 2117 Al and 2124 Al. Reducing impurities, in particular iron and silicon, has resulted in higher fracture toughness and better resistance to fatigue crack initiation and crack growth. The composition and mechanical properties of 2000 alloys used in aircraft are given in Tables 8.3 and 8.4.
Table 8.4
Tensile properties of 2000 alloys used in aircraft
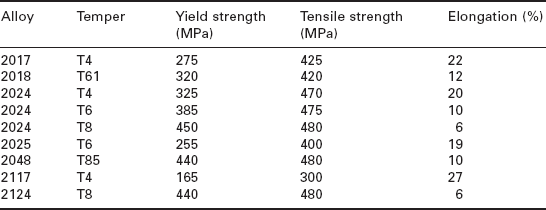
The alloying elements provide important properties that aid in the processing or strengthening of aluminium. Cu, Mg and Zn provide high strength through solid solution strengthening and precipitation hardening. These elements react with aluminium during heat treatment to create intermetallic precipitates (e.g. CuAl2, Al2CuMg, ZnAl) that increase the strength and fatigue resistance. Mn and Cr are present in small amounts to produce dispersoid particles (e.g. Al20Cu2Mn3, Al18Mg3Cr2) that restrict grain growth and thereby increase the yield strength by grain boundary hardening. The addition of trace amounts (0.1–0.2%) of Ti also reduces the grain size. Si is added to reduce the viscosity of molten aluminium, thus making it easier to cast into thick and complex shapes that are free of voids. Fe is used to reduce hot cracking in the casting. However, Si and Fe form coarse intermetallic particles (Al7Cu2Fe, Mg2Si) which lower the fracture toughness, and, therefore, the amount of these elements is kept to a low concentration.
6000 series aluminium alloys (Al–Mg–Si)
The principal alloying elements in the 6000 series are magnesium and silicon. 6000 alloys can be age-hardened with the formation of Mg2Al3 and Mg2Si precipitates. 6000 alloys are used in a wide range of non-aerospace components, such as buildings, rail cars, boat hulls, ship superstructures and, increasingly, in automotive components. However, these alloys are rarely used in aircraft because of their low fracture toughness. 6061 Al (Al–1%Mg–0.6Si) is used occasionally in wing ribs, ducting, tanks, fairing and framework, although this alloy is one of very few used in aircraft.
7000 series aluminium alloys (Al–Cu–Zn)
The 7000 alloys together with the 2000 alloys represent by far the most common aluminium alloys used in aircraft. The main alloying elements in 7000 alloys are copper and zinc, with the zinc content being three to four times higher than the copper. Magnesium is also an important alloying element. These elements form high-strength precipitates [CuAl2, Mg2Al3, Al32(Mg, Zn)49] when aluminium is age-hardened.
7000 alloys generally have higher strength than 2000 alloys. The yield strength of the 7000 alloys used in aircraft is typically in the range 470 to 600 MPa as opposed to the 2000 alloys, which are between about 300 and 450 MPa. 7000 alloys are therefore used in aircraft structures required to carry higher stresses than 2000 alloy components, such as upper wing surfaces, spars, stringers, framework, pressure bulkheads and carry-throughs. The 7000 alloy most often used in aircraft is 7075 Al. Other 7000 alloys used in aircraft structures include 7049 Al, 7050 Al, 7079 Al, 7090 Al, 7091 Al, 7178 Al and 7475 Al. The composition and properties of these aluminium alloys are given in Tables 8.5 and 8.6. Figure 8.4 shows the new types of aluminium alloys and tempers used in the fuselage and wings of the Boeing 777. New high-toughness aluminium alloys for fuselage skins have enabled significant weight reductions through removal of some circumferential frames. The B777 is typical of most modern aircraft in that it uses both conventional and new aluminium alloys. The new alloy is usually superior in one or two properties over the conventional alloy. For example, the fuselage skin material is an alclad 2XXX-T3 alloy which has higher toughness and resistance to fatigue crack growth than 2024-T3.
Table 8.5
Composition of 7000 alloys used in aircraft
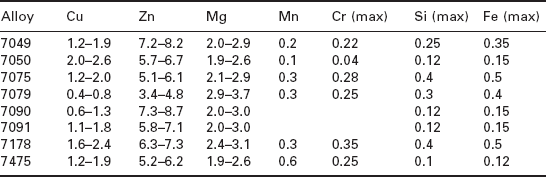
Table 8.6
Tensile properties of 7000 alloys used in aircraft
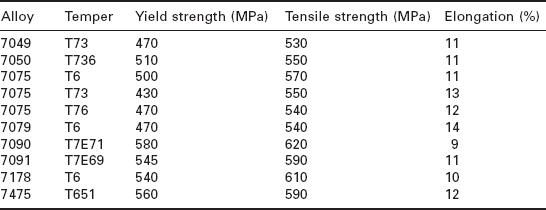
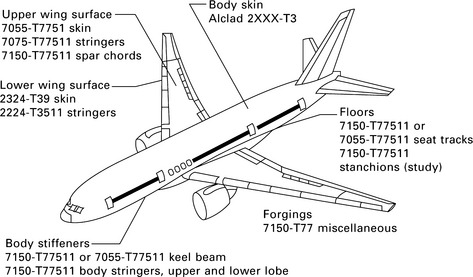
8.4 New aluminium alloys and tempers used on the Boeing 777 (adapted from E. A. Starke and J. T. Staley, Application of modern aluminium alloys to aircraft, Progress in Aerospace Science, Vol 32, pp. 131–172, 1996).
8000 series aluminium alloys (Al–Li)
Aluminium alloys that cannot be classified according to their chemical composition into any one of the 1000 to 7000 series are allocated to the 8000 series. Several 8000 alloys contain lithium, which is unique amongst the alloying elements used in aluminium because it reduces density while simultaneously increasing elastic modulus and tensile strength. (Lithium is also an important, but not the principal, alloying element in a number of 2000 alloys, such as 2020 Al, 2090 Al and 2091 Al, which are used in some aircraft). Figure 8.5 shows the effect of lithium content on the density and Young’s modulus of aluminium. The density decreases by 3% whereas the modulus increases by 5% for every 1% addition of lithium. This shows that lithium in low concentrations can provide significant weight savings to large aluminium structures. In addition, Al–Li alloys generally have better fatigue properties than 2000 and 7000 alloys.
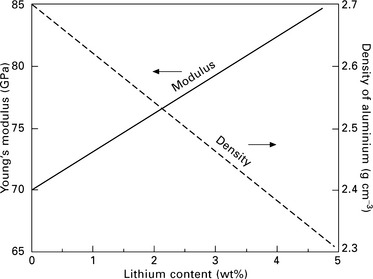
8.5 Effect of lithium content on the Young’s modulus and density of aluminium.
The three Al–Li alloys most often used in aircraft structures are 8090 Al (2.4%Li–1.3%Cu–0.9Mg), 8091 Al (2.6%Li–1.9%Cu–0.9%Mg), and 8092 Al (2.4%Li–0.65%Cu–1.2%Mg). Despite the higher specific stiffness and strength gained by increasing the Li content, the alloys used in aircraft have a relatively low content (less than 3%Li). This is because Al–Li alloys can only be processed using conventional casting technology when the Li content is under 3%. Alloys containing higher amounts of Li must be processed using rapid solidification technology, whereby the molten alloy is solidified rapidly as tiny drops. The solid droplets are then compressed with a binding agent into a metal block using powder metallurgy methods. Rapid solidification processing of alloys for aircraft structures is very expensive, and therefore Li contents below 3% are used to avoid this processing route.
The aerospace industry has invested heavily in the development of Al–Li alloys since the 1980s to produce lighter, stiffer and stronger aircraft structures. However, these alloys have not lived up to their initial promise of widespread use in airframes, and have largely failed to replace conventional aluminium alloys (e.g. 2024 Al, 7075 Al) in most aerospace applications. The limited use of Al–Li alloys is the result of several problems, including the high cost of lithium metal and the high processing cost of Al–Li alloys making them prohibitively expensive for many aircraft structures. Al–Li alloys also have low ductility and toughness in the short transverse direction, which can lead to cracking.
Al–Li alloys are mainly used in military fighter aircraft where cost is secondary to structural performance. For example, Al–Li–Cu alloys are used in the fuselage frames of the F16 (Flying Falcon) as a replacement for 2024 Al, resulting in a three-fold increase in fatigue life, a 5% reduction in weight and higher stiffness. 8090 Al is used in the fuselage and lift frame of the EH 101 helicopter, again for improved fatigue performance and lower weight (by 180 kg), as shown in Fig. 8.6.
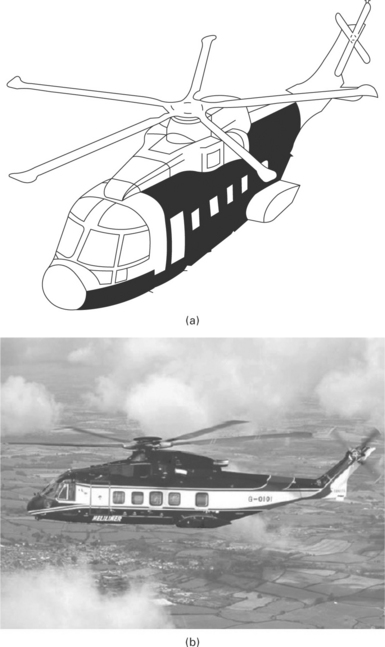
8.6 Al–Li alloy used in the EH101 helicopter. The shaded region in the illustration shows the external structures made using Al–Li alloys.
Al–Li alloys are also used in the super lightweight tanks for the space shuttle, which provided a weight saving of over 3 tonne, which translates directly into a similar increase in shuttle payload. The improved hydrogen tank is 5% lighter and 30% stronger than the original tank made using an Al–Cu (2119) alloy.
Leave a Reply