1.3.1. The Objectives of Production Engineering
Many of the components of the petroleum production system can be considered together by graphing the inflow performance relationship (IPR) and the vertical flow performance (VFP). Both the IPR and the VFP relate the wellbore flowing pressure to the surface production rate. The IPR represents what the reservoir can deliver, and the VFP represents what the well can deliver. Combined, as in Figure 1-7, the intersection of the IPR with the VFP yields the well deliverability, an expression of what a well will actually produce for a given operating condition. The role of a petroleum production engineer is to maximize the well deliverability in a cost-effective manner. Understanding and measuring the variables that control these relationships (well diagnosis) becomes imperative.
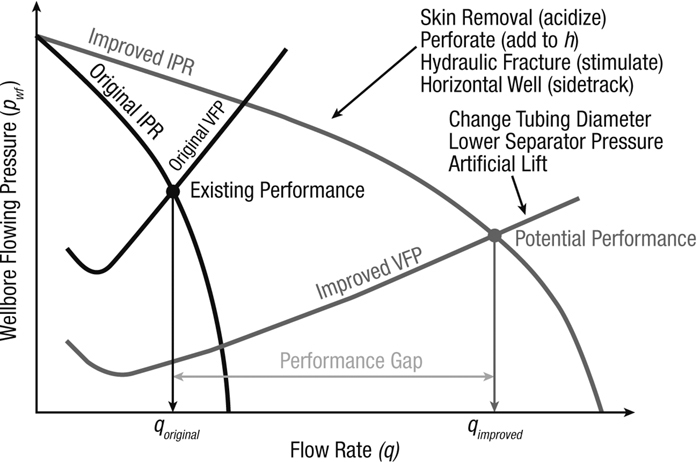
Figure 1-7. Well deliverability gap between the original well performance and optimized well performance.
While these concepts will be dealt with extensively in subsequent. it is useful here to present the productivity index, J, of an oil well (analogous expressions can be written for gas and two-phase wells):

Equation (1-6) succinctly describes what is possible for a petroleum production engineer. First, the dimensioned productivity index with units of flow rate divided by pressure is proportional to the dimensionless (normalized) productivity index JD. The latter, in turn, has very well-known representations. For steady-state flow to a vertical well,

For pseudosteady state flow,
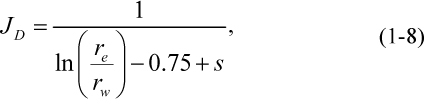
and for transient flow,

where pD is the dimensionless pressure. The terms steady state, pseudosteady state, and transient will be explained. The concept of the dimensionless productivity index combines flow geometry and skin effects, and can be calculated for any well by measuring flow rate and pressure (reservoir and flowing bottomhole) and some other basic but important reservoir and fluid data.
For a specific reservoir with permeability k, thickness h, and with fluid formation volume factor B and viscosity μ, the only variable on the right-hand side of Equation (1-6) that can be engineered is the dimensionless productivity index. For example, the skin effect can be reduced or eliminated through matrix stimulation if it is caused by damage or can be otherwise remedied if it is caused by mechanical means. A negative skin effect can be imposed if a successful hydraulic fracture is created. Thus, stimulation can improve the productivity index. Finally, more favorable well geometry such as horizontal or complex wells can result in much higher values of JD.
In reservoirs with pressure drawdown-related problems (fines production, water or gas coning), increasing the productivity can allow lower drawdown with economically attractive production rates, as can be easily surmised by Equation (1-6).
Increasing the drawdown (p – pwf) by lowering pwf is the other option available to the production engineer to increase well deliverability. While the IPR remains the same, reduction of the flowing bottomhole pressure would increase the pressure gradient (p – pwf) and the flow rate, q, must increase accordingly. The VFP change in Figure 1-7 shows that the flowing bottomhole pressure may be lowered by minimizing the pressure losses between the bottomhole and the separation facility (by, for example, removing unnecessary restrictions, optimizing tubing size, etc.), or by implementing or improving artificial lift procedures. Improving well deliverability by optimizing the flow system from the bottomhole location to the surface production facility is a major role of the production engineer.
In summary, well performance evaluation and enhancement are the primary charges of the production engineer. The production engineer has three major tools for well performance evaluation: (1) the measurement of (or sometimes, simply the understanding of) the rate-versus-pressure drop relationships for the flow paths from the reservoir to the separator; (2) well testing, which evaluates the reservoir potential for flow and, through measurement of the skin effect, provides information about flow restrictions in the near-wellbore environmental; and (3) production logging measurements or measurements of pressure, temperature, or other properties by permanently installed downhole instruments, which can describe the distribution of flow into the wellbore, as well as diagnose other completion-related problems.
With diagnostic information in hand, the production engineer can then focus on the part or parts of the flow system that may be optimized to enhance productivity. Remedial steps can range from well stimulation procedures such as hydraulic fracturing that enhance flow in the reservoir to the resizing of surface flow lines to increase productivity. This textbook is aimed at providing the information a production engineer needs to perform these tasks of well performance evaluation and enhancement.
Leave a Reply