Figure 9.20 presents a schematic of the dimethyl ether (DME) biorefinery. In the DME biorefinery, the black liquor gasifier, supplied with oxygen from an air separation unit, provides all of the synthesis gas to a liquid‐phase DME reactor. Unconverted synthesis gas is separated from product DME and 97% of it is recycled to the synthesis reactor to increase DME production. The 3% purge stream taken from the recycle loop prevents excessive buildup of inert gases. The purge gas is sent to the hog fuel boiler, where it burns with an amount of wood residues selected such that the amount of steam generated is sufficient to meet all of the mill’s process steam needs. Heat recovered from the black liquor and syngas processing areas are integrated into the boiler to increase steam production and minimize the amount of woody residues needed. The steam is expanded through a back‐pressure turbine to generate some electricity which goes toward meeting the mill’s process electricity needs. To fully meet the mill’s electricity need, some electricity must be imported from the grid. Because black liquor is being converted primarily into liquid fuel and not electricity, the amount of electricity imported is larger than with a conventional Tomlinson system (ETC 2011; Larson et al. 2006a).
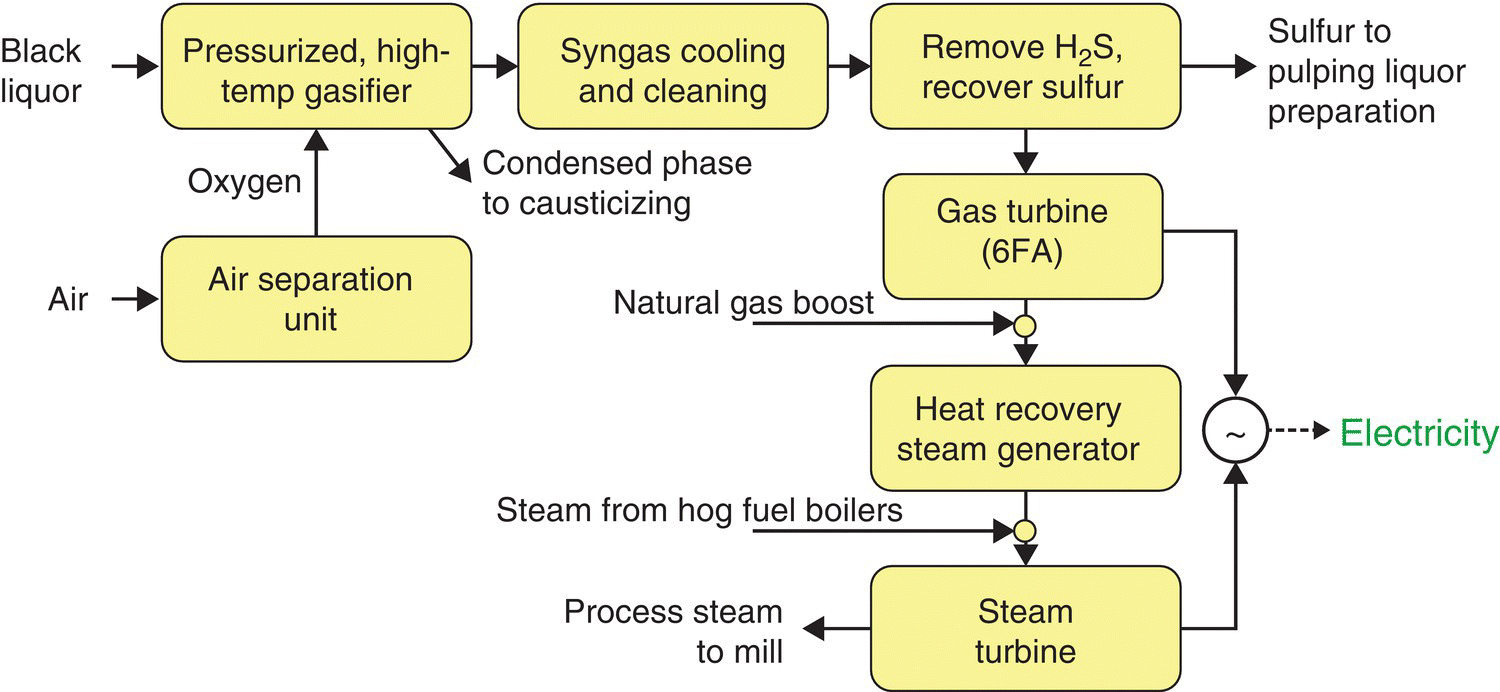
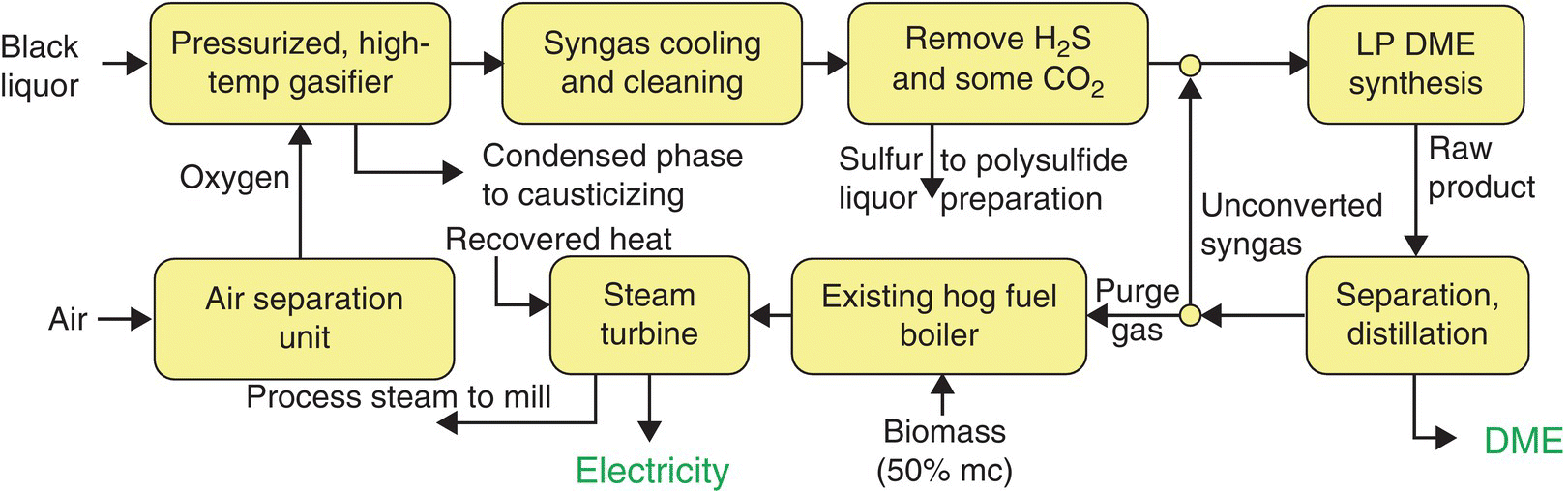
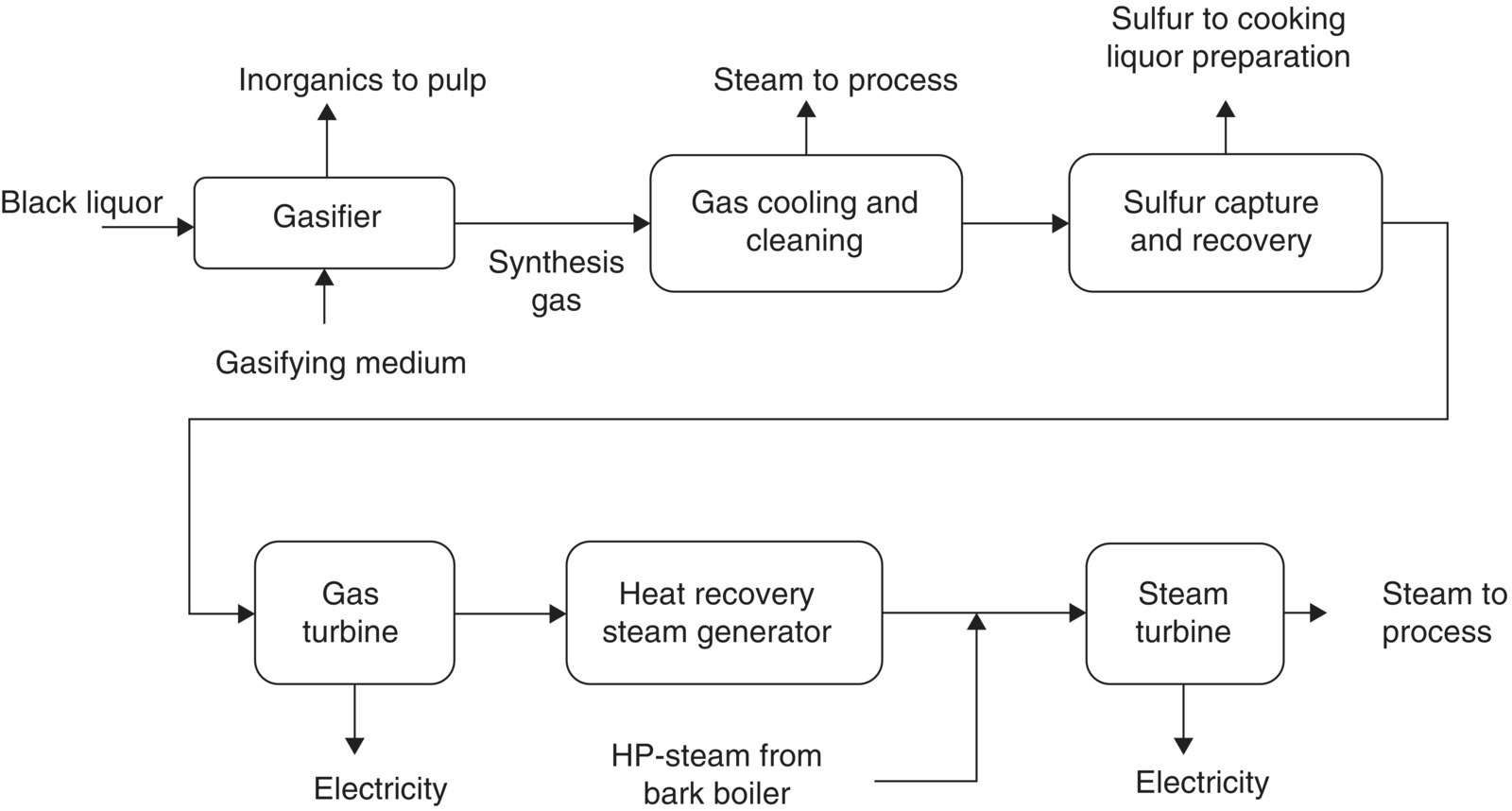
Figure 9.21 gives a simplified representation of the basic design of the BLGCC system (Naqvi et al. 2010). The electricity output will be increased especially with pressurized gasification and a gas turbine–based cogeneration system. A number of studies were performed to estimate potential electricity generation in the pulp industry by implementing a BLGCC technology (Eriksson and Harvey 2004; KAM Report 2003; Larson et al. 2003).
Hydrogen production from gasified black liquor has also been studied. Andersson and Harvey (2004) evaluated energy and net CO2 emissions consequences of integrated hydrogen production from BLG in a chemical pulp mill. The base capacity of the pulp mill was 2000 ADt/day of pulp production. Hydrogen production at the reference KAM pulp mill required import of 210 000 T of biomass for steam production and 0.43 TWh/year of electricity. If black liquor from all pulp mills in Sweden were gasified to produce hydrogen, the estimated import of biomass was 4.9 and 2.3 TWh/year of electricity. The results showed a large potential of hydrogen production, i.e. 188 T/day of hydrogen fuel which was equivalent to 261 MW [lower heating value (LHV), 120 MJ/kg] (KAM Report 2003).
Larson et al. (2006a, b) made a “well‐to‐wheels” (WTW) comparative environmental assessment of BLG for liquid fuel production with BLGCC electricity production at kraft pulp mills in the United States. The introduction of BLGCC systems in the United States had potential to displace up to 35 million T net CO2, 16 000 T net SO2, and 100 000 T net NOx within 25 years (Naqvi et al. 2010).
Leave a Reply