The US pulp and paper industry is the largest producer and user of biomass energy in the United States today, nearly all derived from sustainably grown trees. Renewable resources used at pulp mills include bark, wood wastes, and black liquor, the lignin‐rich by‐product of cellulose‐fiber extraction.
With substantial renewable energy resources at its immediate disposal and with potentially much more extensive resources available in the long term, the US pulp and paper industry has the potential to contribute significantly to addressing climate change and US energy security concerns, while also improving its global competitiveness. A key requirement for achieving these goals is the commercialization of breakthrough technologies, especially gasification, to enable the clean and efficient conversion of biomass to useful energy forms, including electricity and transportation fuels.
Gasification technology enables low‐quality solid fuels like biomass to be converted with low pollution into a fuel gas (synthesis gas or “syngas”) consisting largely of hydrogen (H2) and carbon monoxide (CO). Syngas can be burned cleanly and efficiently in a gas turbine to generate electricity. It can be passed over appropriate catalysts to synthesize clean liquid transportation fuels or chemicals. It can also be converted efficiently into pure H2 fuel.
While most pulp and paper manufacturing facilities in the United States today do not export electricity and none export transportation fuels, their established infrastructure for collecting and processing biomass resources provides a strong foundation for future gasification‐based “biorefineries” that might produce a variety of renewable fuels, electricity, and chemicals in conjunction with pulp and paper products (Figure 9.17) (Perlack et al. 2005).
If the biomass resources from which energy carriers are produced at such biorefineries are sustainably grown and harvested, there would be few net lifecycle emissions of CO2 associated with biorefineries and their products. To the extent that the biorefinery products replace fuels or chemicals that would otherwise have come from fossil fuels, there would be net reductions in CO2 emissions from the energy system as a whole. The reductions would be even more significant if by‐product CO2 generated at biorefineries were to be captured and sent for long‐term underground storage (Larson et al. 2006b). Carbon capture and storage with fossil fuels is of wide interest today. Several large‐scale CO2 storage projects (storing >1 million T/Y of CO2) are operating and more are under development worldwide to demonstrate feasibility (USDOE 2006).
Coupled with the potential to address national energy security and global warming concerns is the looming need in the US pulp and paper industry for major capital investments to replace the aging fleet of Tomlinson recovery boilers used today to recover energy and pulping chemicals from black liquor. The majority of Tomlinson boilers operating in the United States were built beginning in the late 1960s through the 1970s. With serviceable lifetimes of 30–40 years, the Tomlinson fleet began undergoing a wave of life‐extension rebuilds in the mid‐1980s. Within the next 10–20 years, rebuilt boilers will be approaching the age at which they will need to be replaced, the capital investment for which at a typical mill will be between $100 and $200 million. A similar situation exists in the European pulp industry. This situation provides an unusual window of economic opportunity for introducing black liquor gasifiers as replacements for Tomlinson boilers. Concerted efforts are ongoing in the United States and Sweden to develop commercial black liquor gasification technologies (Ekbom et al. 2005; Larson et al. 2006a; Swedish Forest Agency 2008).
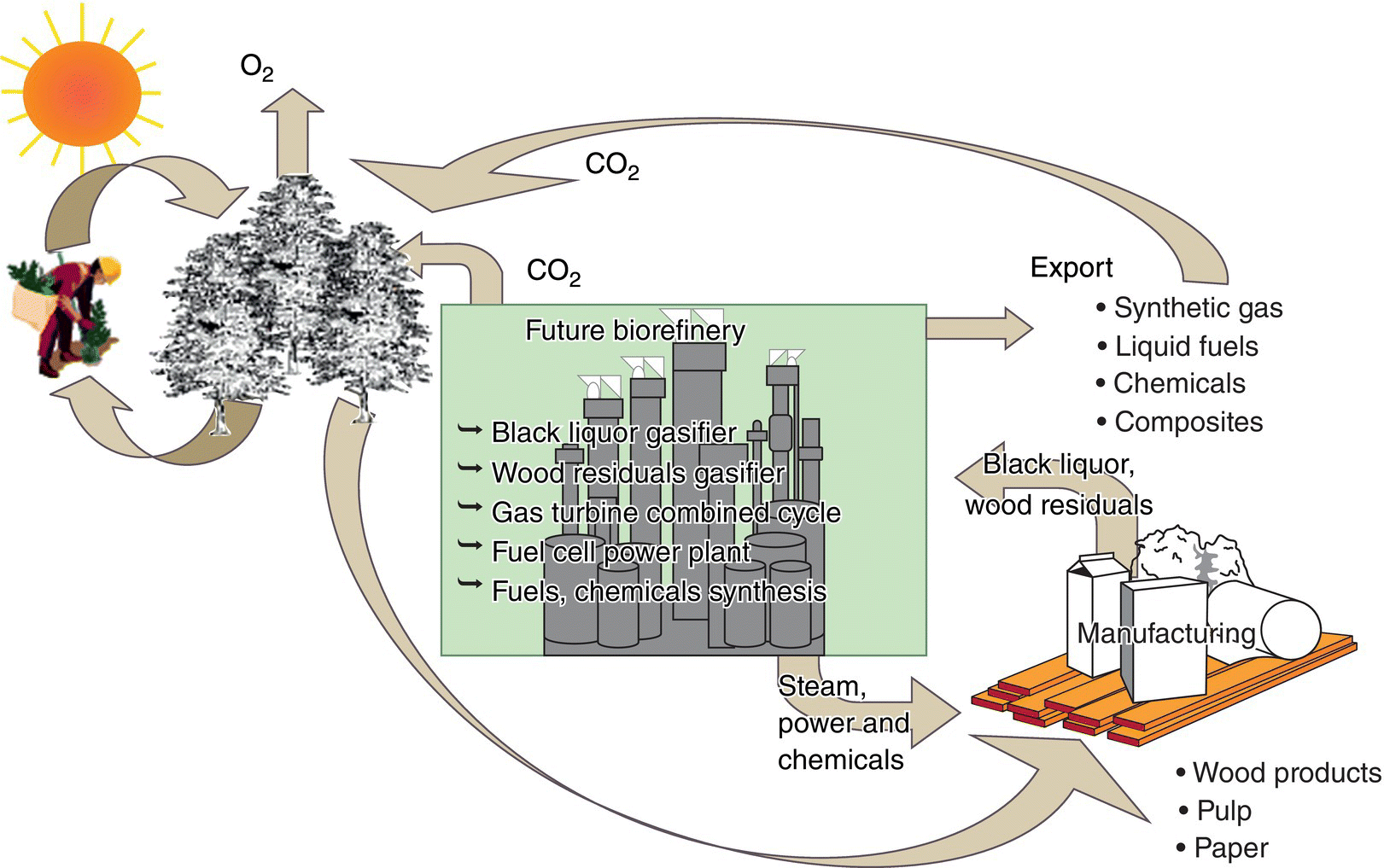
Leave a Reply