Advanced Multi‐Pollutant Control: Intensified Regenerative Activated Coke Technology
Regenerative activated coke technology (ReACT™) is an advanced intensified multi‐pollutants technology that achieves simultaneous capture of SOx, NOx, and mercury in one vessel. The process was first developed in Germany, and it was subsequently advanced and commercialized by J‐Power EnTech in Japan where ReACT™ has been implemented at three large‐scale coal‐fired power plants and at several steel mills, petrochemicals, refineries, and waste incinerator facilities, as a high‐efficiency emission control system.
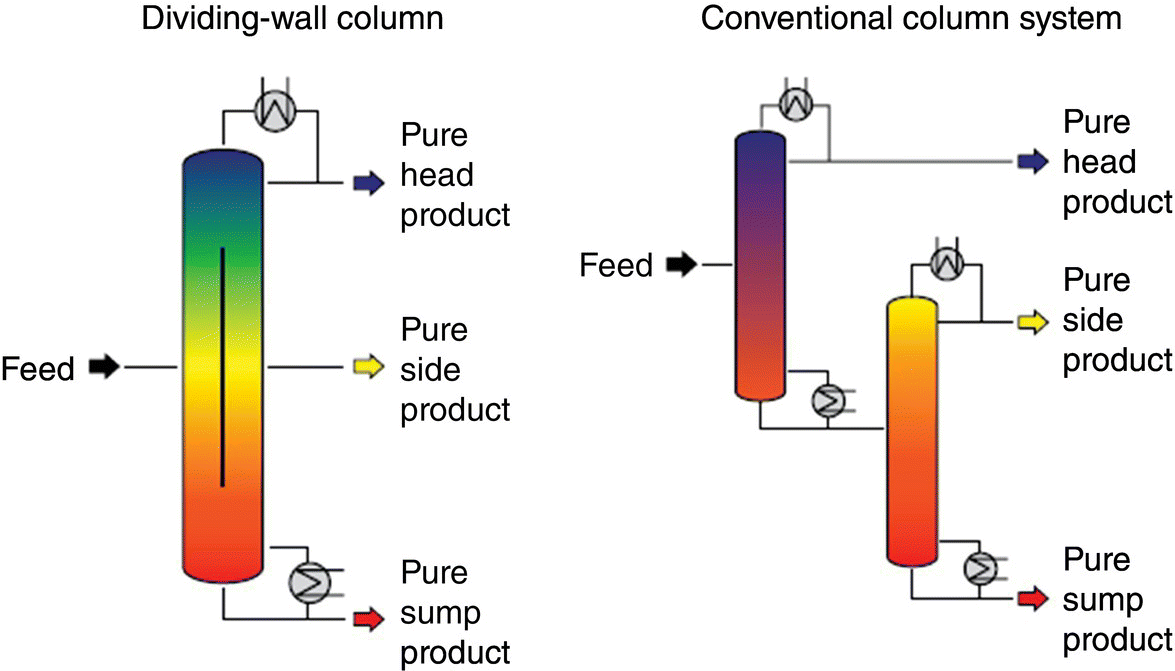
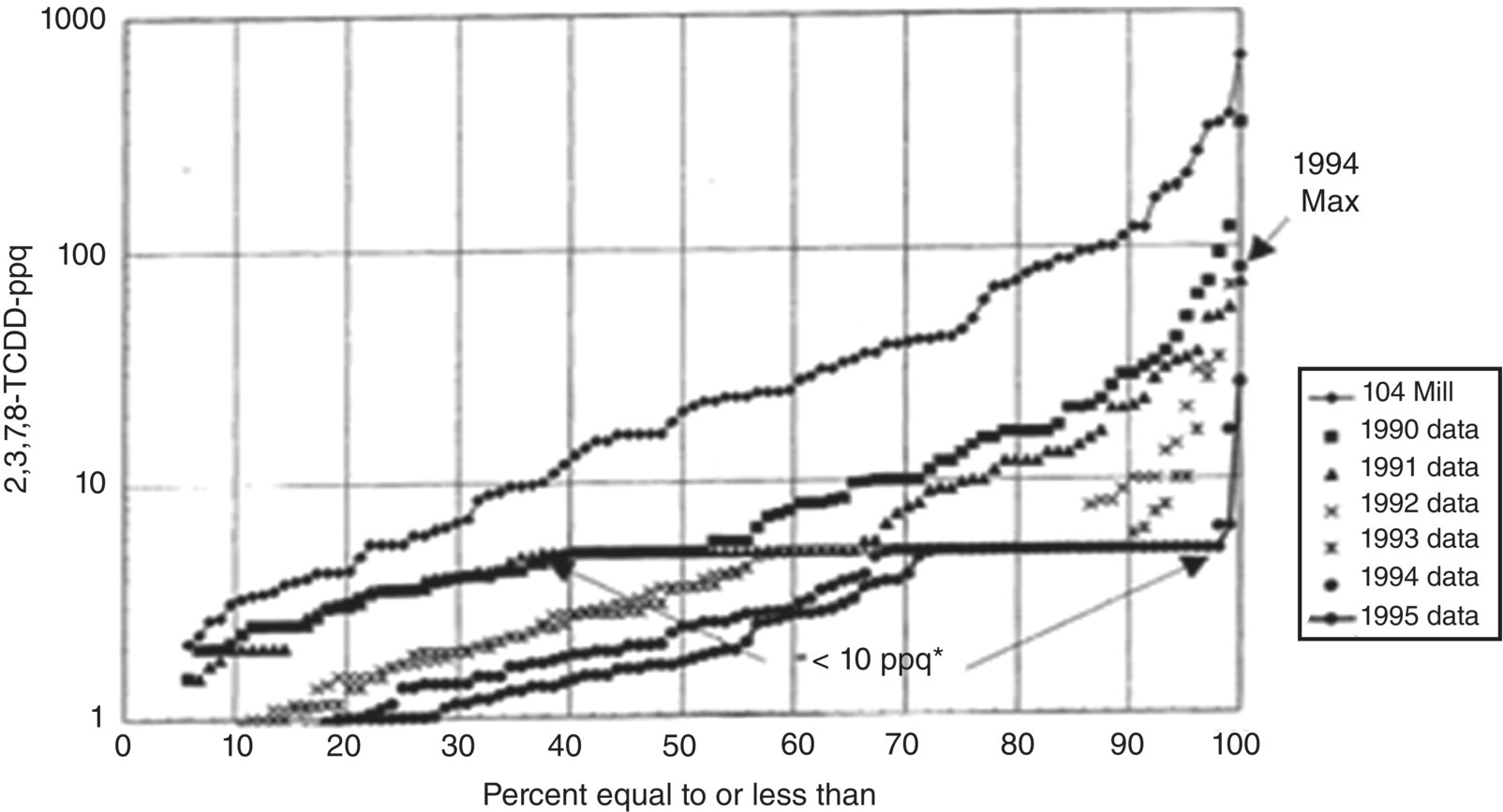
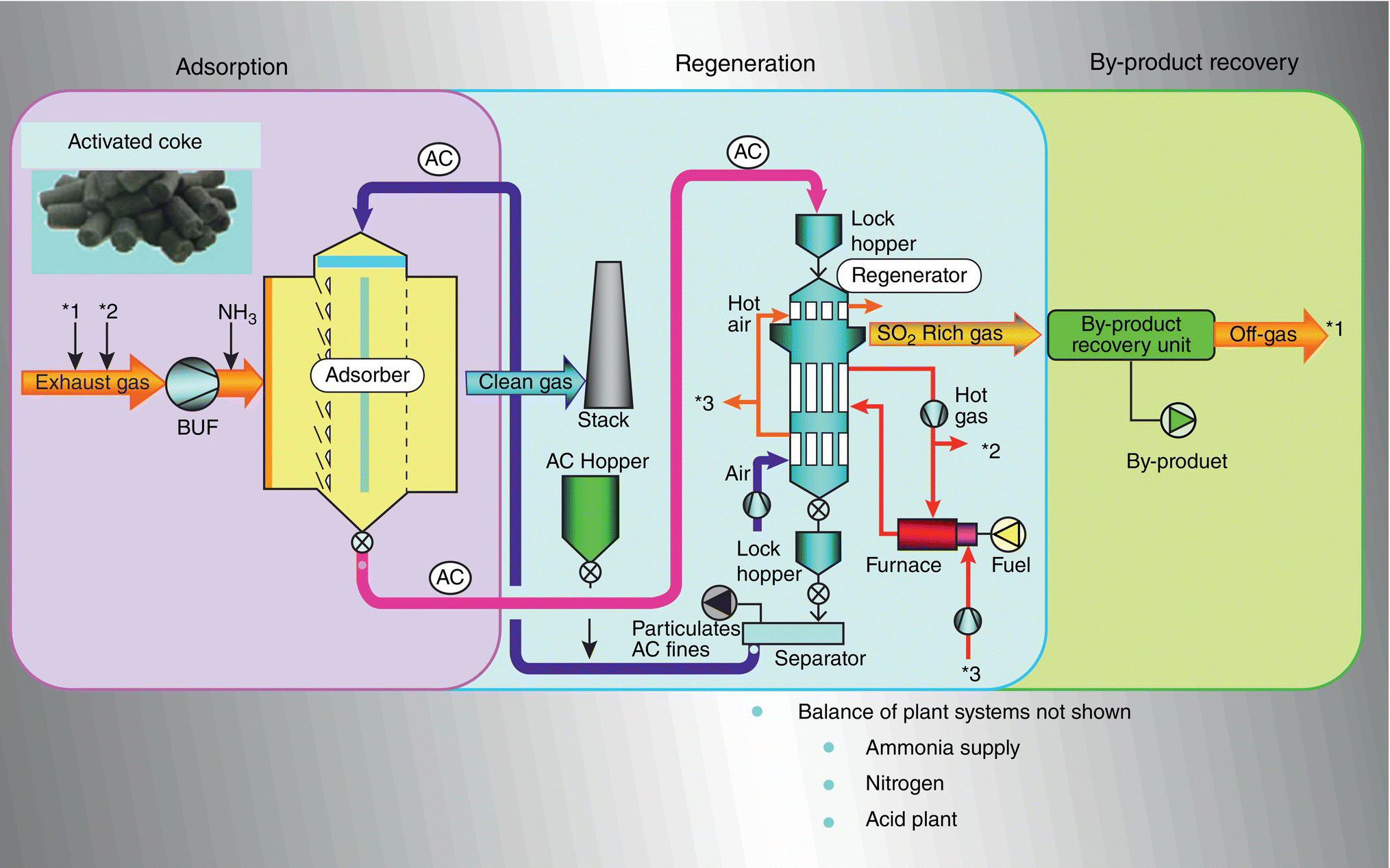
Figure 9.13 shows the three‐stage ReACT™ process, including adsorption by activated coke (AC) followed by regeneration of SOx and mercury, and then by‐product recovery of sulfur‐rich gas converting into a marketable sulfuric acid.
ReACT™ technology is based on adsorption of SO2 and NOx on AC in a moving bed, with subsequent regeneration of the coke and production of saleable by‐product sulfuric acid. This technology is a completely dry scrubbing event that does not evaporate any water into the flue‐gas stream, can produce extremely low level of SO2 emissions, and can also provide additional control for NOx, PM, and Hg as co‐benefits. The moving bed dry scrubber operates downstream of a primary particulate control device, which for many plants is traditional ESP technology. For special cases where extremely low levels of particulate are permitted, a downstream polishing ESP can also be applied.
A mix of custom and traditional material handling equipment transports the AC to and from the absorber and regenerator. Careful material handling and the robust nature of the AC allow the coke to be recycled with minimal makeup requirements.
Simultaneous capture of SO2, NOx, and Hg is accomplished in one vessel along with a further reduction in particulate emissions. High removal efficiencies include up to 99.9% SO2, 50–80% NOx, and above 90% Hg (including elemental). Particulate is also reduced by about 50%. Advantages of this technology include high‐emission reduction efficiencies, cost‐effectiveness, low power consumption, minimum installation space, minimal water requirements (dry process), no gas reheating, and low maintenance requirements. The AC process involves three steps: (i) adsorption, (ii) regeneration, and (iii) by‐product recovery (Figure 9.13).
In the absorber, the flue gas passes through a bed of AC moving slowly downward at a constant flow rate. The adsorber is a single stage, reflecting an improvement over previous designs, which had a two‐stage adsorber. Removal of SO2, NOx, Hg, and particulates is taking place in one step. As the AC is saturated with pollutants, it is conveyed through a bucket elevator to the regenerator. The regenerator operates at temperatures in the 399–499 °C range. Simultaneously, sulfuric acid or ammonium salts in the AC are decomposed to N2, SO2, SO3, and H2O. Hg is retained in the AC and removed at some period of time, depending on the Hg concentrations at the inlet of ReACT™.
After cooling, the regenerated AC passes through a separator (vibrating screen), which separates particulates and small particles of AC, from the larger AC, which is returned to the adsorber. The AC removed from the separator can be returned to the boiler for burning or sold and used in industrial applications, such as dioxin adsorption – SO2‐rich gas from the generator is converted to a saleable product, such as sulfuric acid, in the by‐product recovery facility (Figure 9.14).
- Adsorption and reaction on AC: SO2 and SO3 are adsorbed at high efficiency on the AC surfaces as sulfuric acid, ammonium sulfate, and ammonium bisulfate.
- The catalytic effect of AC also leads to reduction reactions to reduce NOx in the presence of ammonia. The NOx control activity is completed in the adsorber as follows:
(* denotes adsorbed species)
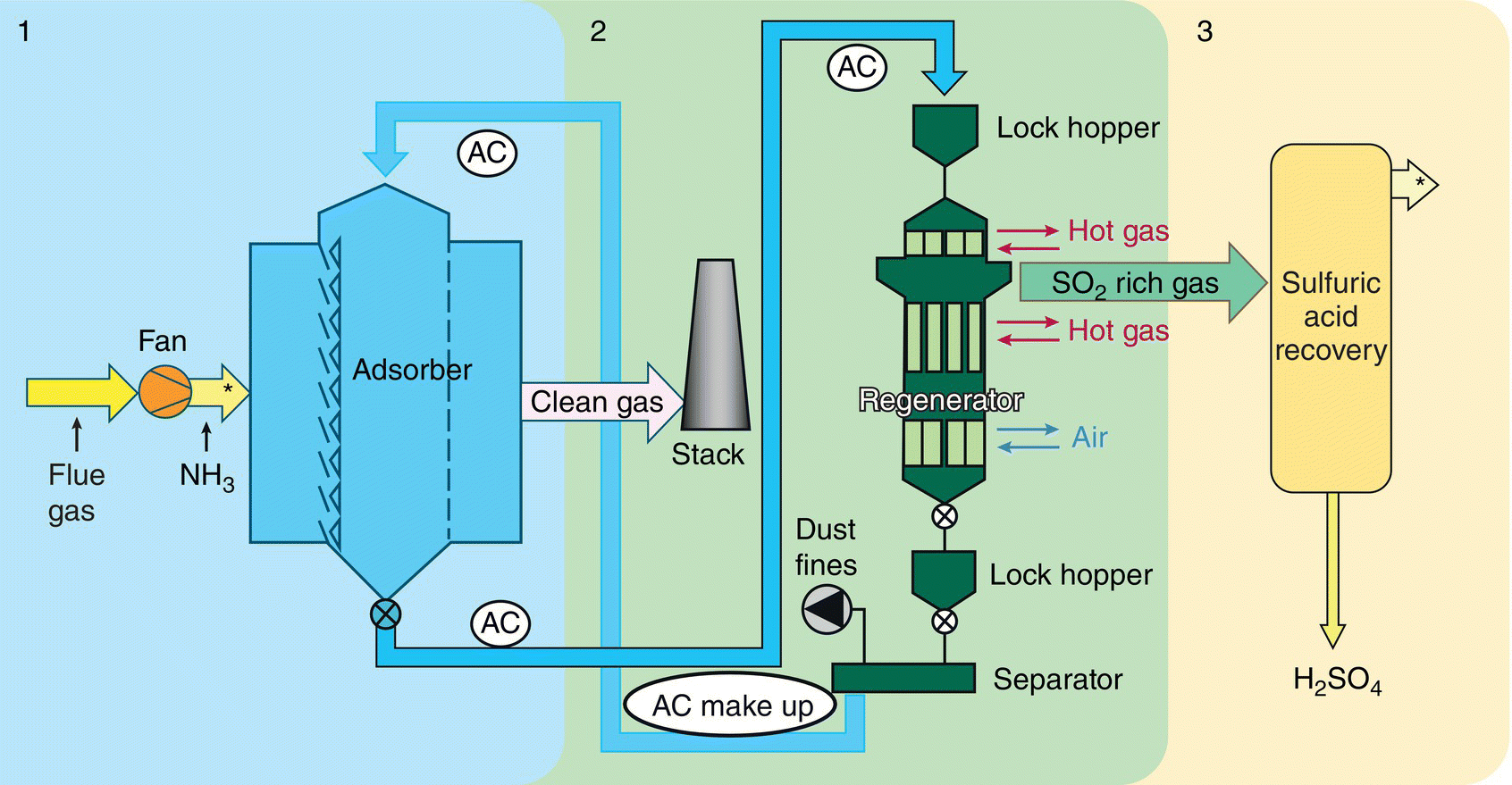
Leave a Reply