Life cycle cost analysis (LCCA) is a tool to determine the most cost‐effective option among different competing alternatives to manufacturing process, purchase, own, operate, maintain and, finally, dispose of an object or process, when each is equally appropriate to be implemented on technical grounds. For example, for a highway pavement, in addition to the initial construction cost, LCCA takes into account all the user costs (e.g. reduced capacity at work zones) and agency costs related to future activities, including future periodic maintenance and rehabilitation. All the costs are usually discounted and total to a present‐day value known as net present value. This example can be generalized on any type of material, product, or system.
In order to perform a LCCA, scoping is critical – what aspects are to be included and what not? If the scope becomes too large, the tool may become impractical to use and of limited ability to help in decision‐making and consideration of alternatives; if the scope is too small then the results may be skewed by the choice of factors considered such that the output becomes unreliable or partisan. Usually, the LCCA term implies that environmental costs are not included, whereas the similar whole‐life costing, or just LCA, generally has a broader scope, including environmental costs
Cost of Quality: Poor vs. Good Quality
When calculating the business case for a Six Sigma project, the cost of poor quality (COPQ), which is the cost caused through producing defects, is a commonly used concept. Within the total amount of quality cost, however, COPQ represents only a certain proportion. Costs do not result from only producing and fixing failures; a high amount of costs comes from ensuring that good products are produced. This section explains the cost of quality as a more comprehensive concept covering the COPQ and the cost of good quality. In short, any cost that would not have been expended if quality were perfect contributes to the cost of quality.
Cost of Quality: Not Only Failure Cost
The cost of quality has two main components: the cost of good quality (or the cost of conformance) and the COPQ (or the cost of nonconformance). Figure 8.22 shows the following.
- The COPQ affects:
- Internal and external costs resulting from failing to meet requirements.
- The cost of good quality affects:
- Costs for investing in the prevention of nonconformance to requirements.
- Costs for appraising a product or service for conformance to requirements.
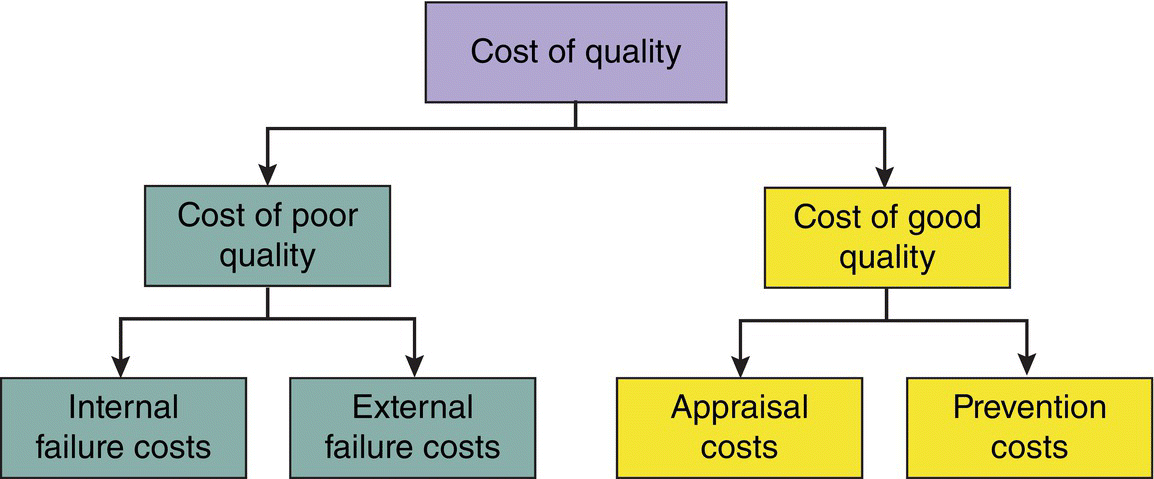
Leave a Reply