If we look at consumption of resources (any resource) or the impact of that consumption over time we can identify a trend, generally increasing over time. The sustainable rate of that consumption, or impact, is often much less. Here we can discuss sustainability in the context of a well cited of the Bruntland Commission, formally the World Commission on Environment and Development, as part of a study to look at conditions for fostering sustainable development in the world (Our Common Future 1987). They defined sustainable development is “development that meets the needs of the present without compromising the ability of future generation to meet their own needs.”
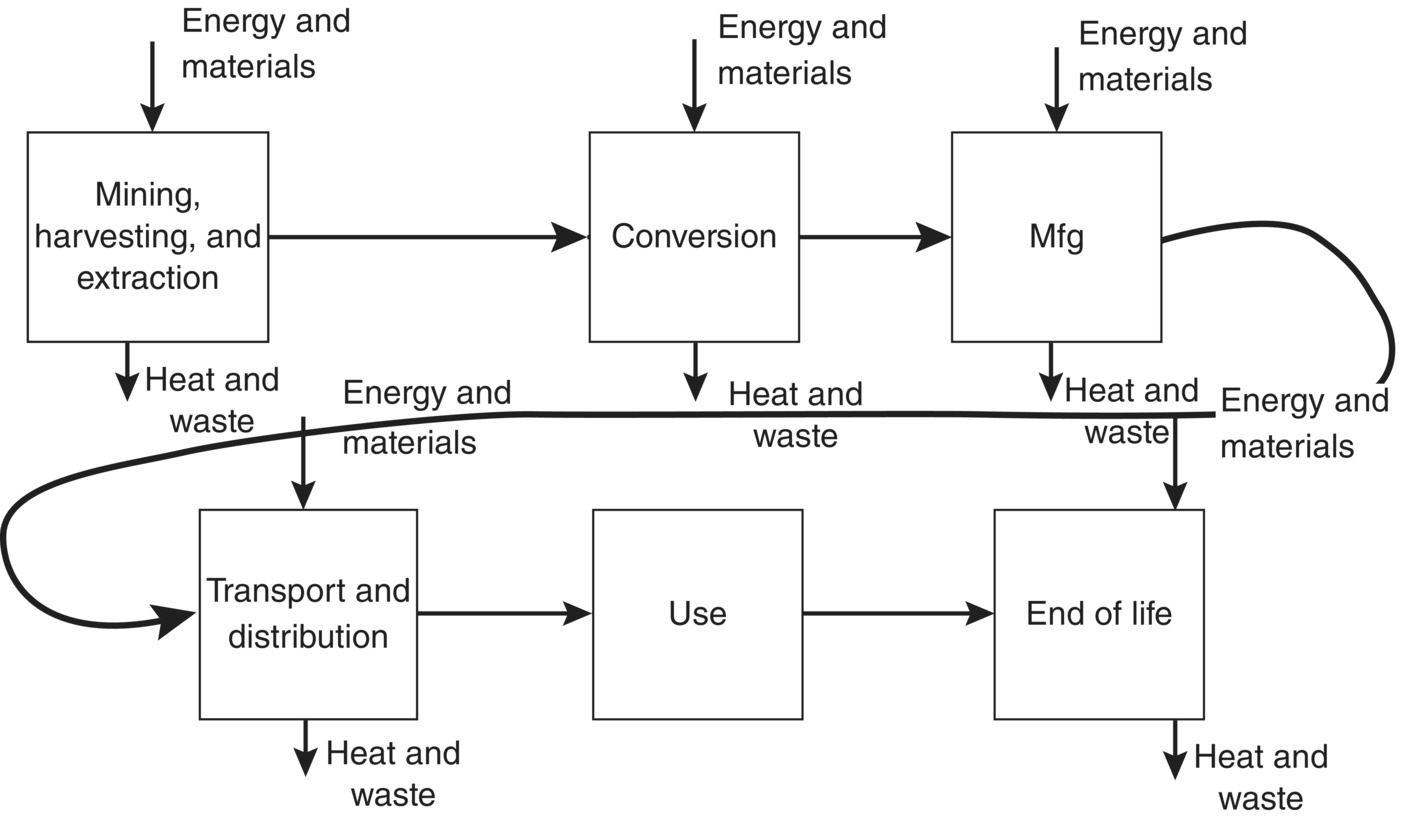
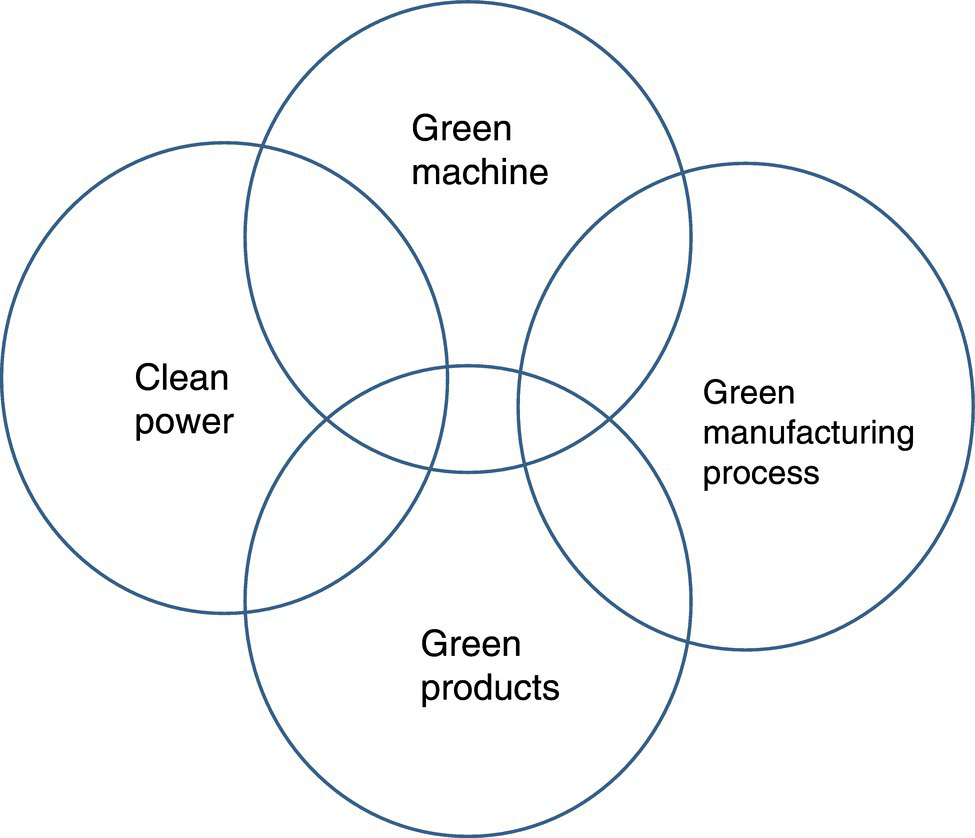
This is a lofty goal to meet when designing products and systems of production. If we define a level of sustainability so that we don’t “compromise the…future,” paraphrasing here from Brundtland, it means our factories and processes are at or below the level of sustainable impact or consumption. Figure 8.17 illustrates the challenge. The “wedge” between our rate of consumption or its impact and the sustainable rate of consumption or impact is often large and growing. In order to return to a sustainable level of consumption, especially from the perspective of manufacturing, we will need to reduce the consumption, or impact, at a rate larger than its natural growth (think population increase times per capita consumption or impact). Just reducing consumption or impact, although preferable than not, is insufficient. That is a challenge! One way to look at this is from the standpoint of “technology wedges.”
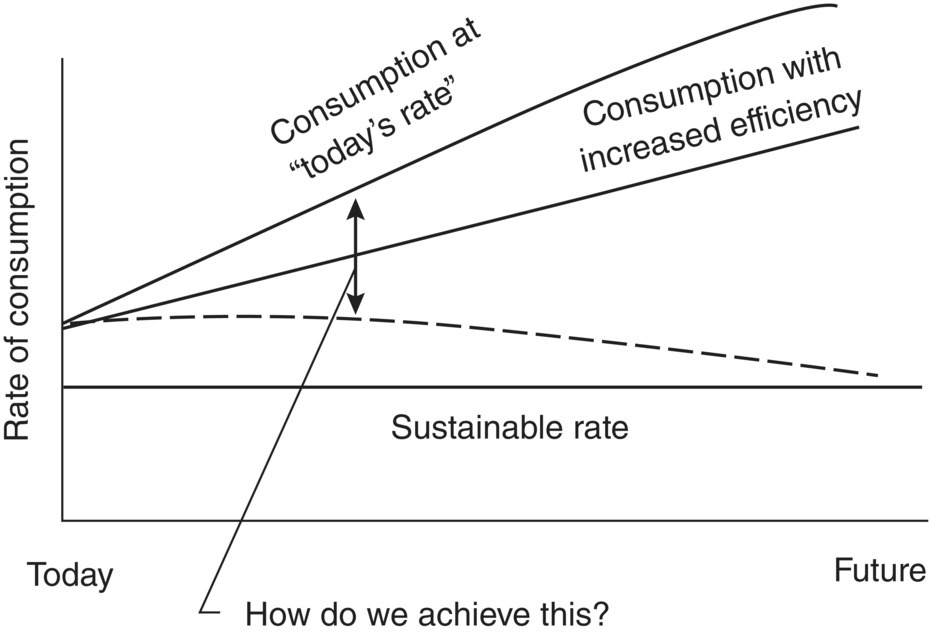
Manufacturing Technology Wedges
Pacala and Socolow (2004) describe the concept of “stabilization wedges” with respect to technology that could solve the climate problem (with respect to fossil fuels) for the next 50 years using current technology. The idea is to close the gap between current rate of impact and the sustainable level with “wedges” of technology – each making a small but measureable improvement. They introduce the idea that focuses on the “gap” between the current trends in fossil fuel emissions (the impact or consumption) relative to the atmosphere’s capability to accommodate emissions (the sustainable level). This is a similar gap to that (normal consumption vs. sustainable consumption) in Figure 8.17. Each individual wedge represents the ability of some existing current technology to reduce, on its own, some portion of fossil emission. Then, summed together, these wedges provide the necessary reduction in emissions to achieve an overall “sustainable” situation. Their goal was to achieve CO2 stabilization at 500 ppm by 2025, a sustainable level.
The question is whether or not this strategy could be employed in manufacturing to accomplish environmentally benign manufacturing processes. There is a renewed interest in developing process enhancements that contribute to reducing an environmental impact. As yet, there is no strategy to coordinate a set of enhancements and new capabilities that will, combined, render a process “sustainable” as in the case of the fossil fuel emission example (Dornfeld and Lee 2008).
There are some interesting possibilities. With the development of new manufacturing technologies for microscale and nanoscale manufacturing, as well as the various alternative energy sources being pursued (from fuel cell to photovoltaics), attention will need to be paid to ensure that any new processes will have some damaging effects on environment and health (see more details in Section 9.2.6). That is, wedges must be designed to be “net‐positive.” An improvement in one element of a process or system of manufacture cannot be at the expense of another segment of the cycle (Hawken 1993). This is specially complicated with the complex supply chains employed today. Continuous improvement is as valid here as in other areas of manufacturing. We strive to remove “wasted time and effort.” Why not also try to do this for energy/consumables/waste? Here it is proposed that “technology wedges” – analogous to “stabilization wedges” – offer a framework and potential metric for addressing these energy challenges.
There are a number of fundamental rules which govern how wedge technology can be employed in manufacturing. In no particular order, they are as follows (Dornfeld and Wright 2007):
- Rule 1. The cost of materials and manufacturing [in terms of energy consumption and Green House Gas (GHG) emissions, etc.] associated with the wedge cannot exceed the savings generated by the implementation of the wedges over the life of the process or system or product in which it is employed (see Section 8.11.4).
- Rule 2. The technology must be applied at the lowest level in the process chain.
- Rule 3. The cost and impact of the technology must be calculated in terms of the basic metrics of the manufacturing system and the environment. That is, cost and impact must be expressible in units of dollars (or euros, yen, etc.), carbon equivalent, global warming gas creation or reduction, joules, cycle time and production rate, quality measures, lead time, working capital, and so on relative to present levels of consumption, use, time, etc.
- Rule 4. The technology must take into consideration societal concerns along with business and economy (Hawken 1993).
- Rule 5. There must an accompanying analytical means or design tool so that it can be evaluated at the design stage of the process or system. It must be an integrated approach.
These rules, when applied, will insure a balanced and accurate appraisal of the impact of the technology from an environmental perspective and also insure the rules are feasible from a business perspective. This will avoid creation of anomalies in the supply chain caused by a gain which yields a global net loss. Many examples of a net loss currently exist in society, such as with so‐called “high tech/low cost” products, some of which operate efficiently, but which have short useful lives. The consumer “learns” to expect this and, thus, expects to replace the product in a short time. This trend destroys a tremendous amount of product value and resources and, worse, it encourages increased environmental damage. The life cycle of such “through‐away” products is often not considered in the design, fabrication, use, or reuse.
Leave a Reply