Industrial air pollution prevention (P2) efforts have focused on both source and waste reduction, and on reuse and recycling. A key approach is preventing air pollution within a company’s manufacturing processes, particularly in chemical process industries. Frequently, we fail to consider that control systems themselves are industrial processes that consume energy and can emit significant pollutants into the atmosphere. There has been a tendency to pursue the control of each target pollutant independently while ignoring secondary pollutants. Opportunities to reduce energy consumption and secondary pollutants simply by selecting sustainable pollution control technologies are increasing.
Air pollution arises from a number of sources: stationary such as factories and other manufacturing processes; mobiles such as automobiles, recreational vehicles, snowmobiles and watercraft; and area sources which are all other emissions associated with human activities. Air quality problems are closely associated with combustion processes occurring in the industrial and transportation sectors of the economy.
Air pollution control is an area where P2 and sustainability concepts are relatively new and just beginning to be applied, and the promise of significant environmental and economic benefits is strong. However, the regulatory development processes and framework have not fully embraced them.
Since large industries could reasonably assimilate the cost of controls into their cost of doing business, the United States’ air quality regulatory approach began with these sources having the most potential for immediate environmental improvement. The regulatory requirements have progressively tightened standards and applied limits to smaller sources too. The regulations began targeting priority pollutants as separate and distinct entities to be controlled. These tendencies are part of the problem Congress was addressing through the Pollution Prevention Act of 1990, as stated in finding number 3:
The opportunities for source reduction are often not realized because existing regulations, and the industrial resources they require for compliance, focus upon treatment and disposal, rather than source reduction; existing regulations do not emphasize multi‐media management of pollution; and businesses need information and technical assistance to overcome institutional barriers to the adoption of source reduction practices.
(Pollution Prevention 1997; State of California January 2001; United State Congress, Pollution Prevention Act of 1990; CFR 2019)
However, some P2 concepts and the lack of cost‐effective treatment technologies for smaller sources have also guided the regulatory approach. For example, many paint and coatings industry regulations have set limits on VOCs in the product formulations as the primary compliance mode, with end‐of‐pipe treatment as an alternative compliance option (State of California 2001). On the other hand, current regulations also have requirements such as BACT, requiring large sources to achieve a high level of treatment for each target pollutant with only limited consideration of the cost, in either money or secondary environmental impacts.
An area of particular opportunity is the control of VOCs and odors. Traditional control technologies, such as thermal and catalytic oxidation, are effective in reducing VOC emissions by more than 95%. They have become the standard by which other VOC control technologies are measured for acceptability through regulatory concepts such as BACT. However, these technologies frequently demand significant energy and produce secondary wastes such as NOx, SOx, and greenhouse gases. It is not uncommon for a facility to have challenges meeting NOx emission standards due to the secondary emissions from their VOC removal systems. VOC control technologies frequently combust large quantities of natural gas to maintain the required temperature for destruction of the VOCs, resulting in significant emissions of greenhouse gases.
EXAMPLE 7.3 SOLVENT EMISSION FROM A DRY CLEANING SHOP
A dry cleaning shop in Los Angeles is trying to estimate if it will need to apply Reasonably Available Control Technology (RACT) to its operations. The Clean Air Act threshold for a major source in Los Angeles is 10 T (1 T = 2000 lb) of VOC emissions per year. The shop operates its cleaning facilities 8 h/day, 6 days/week, and 51 weeks/year. The shop’s new vapor recovery equipment has a 250 gal reservoir and loses an average of 0.70 gal of solvent/hour during operations. The solvent is perchloethylene, which has a liquid density of 1483 kg/m3 (12.17 lb/gal).
- Does this shop need to apply RACT?
- If, instead of Los Angeles, this shop were to be located in New York City, would it need to apply RACT? The VOC emission threshold for New York City is 25 T/Y.
SOLUTION
To calculate the shop’s hourly mass emissions, the following expression is used:

The mass emission rate in lb/day is then:

The mass emission rate is then converted to annual emissions in lb/year as

The emission rate is then converted to T/Y as

The actual annual emission rate is then compared to the major source threshold for Los Angeles of 10 T/Y, i.e. 10.6 T/Y actual >10 T/Y. Since the result marginally exceeds the 10 T/Y threshold, the shop must therefore apply RACT.
The major source threshold for New York City is 25 T/Y. Since this shop emits 10.6 T/Y, it is below the 25 T/Y threshold for New York City, and therefore does not need to apply RACT.
As a rule of thumb, the release of 1 gal/h of solvent with specific gravity 1.0 is equivalent to approximately 10 T/Y for a 52 week, 8‐hour work schedule, and 30 T/Y for a 24‐hour work schedule.
EXAMPLE 7.4 COST OF A CATALYTIC/THERMAL INCINERATOR
A catalytic incinerator is investigated to replace the thermal incinerator operating at a rate of 2.53 lb/min fuel gas flow rate at 750 °C. Because of the lower required temperature, the required fuel gas flow rate drops to 1.44 lb/min. At a cost of $4.00/MBtu for fuel gas, calculate the maximum justifiable cost of the catalytic system. Assume that the costs of the shells of both systems are the same, so the only additional cost is that of the catalysts itself. Assume the catalyst must be replaced every five years, and the incinerator operates 24 h/day, 300 days/year.
SOLUTION
Calculate the amount of fuel saved.

Calculate the yearly fuel saved.

Calculate the yearly fuel savings knowing when the incinerator operates.
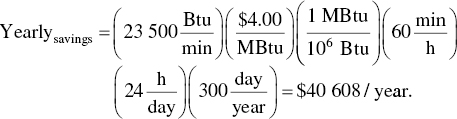
Calculate how much money could be saved in 5 years’ time.

With this considered, the maximum that can be spent is roughly $203 000 for the catalyst to make the costs of the thermal and catalytic incinerators equal.

Leave a Reply