A complete financial analysis requires the inclusion of CF. On a year‐by‐year basis, the CF from a manufacturing investment is determined through calculations of cash costs, total costs, and cost‐effectiveness.
Cash costs, those associated with operating and overhead, include raw materials (chemicals, catalysts, solvent, etc.) utilities (steam, electricity, natural gas, water, etc.), maintenance materials and labor, operations labor, technical support, startup costs, taxes and insurance, and administrative costs.
Total costs include the sum of cash costs as just defined and depreciated. Note that depreciation is not a cash cost and is used only to calculate income taxes. If the investment generates revenues or savings from which the total costs may be subtracted, the resulting amount is known as the “pretax earnings.” Income taxes (calculated on pretax earnings) are next subtracted to yield the after‐tax earnings. A year‐by‐year CF can then be determined by summing the four real CFs: investment, cash costs, revenues, and income taxes.
NPV is the sum of the PVs of a series of CFs:
(7.3)
where, CF0, CF1, CF2 represent CF in year 0, 1, 2, and so on, and the D terms are discount factor for the respective years.
In the context of pollution control, cost‐effectiveness is defined as the annualized cost of the control option divided by the annual emission reductions resulting from the control option. The following information is required to calculate the cost‐effectiveness of a proposed control option: (i) the capital cost of purchasing and installing the control equipment or making a process modification, (ii) the annual operating costs of the control option, and (iii) an estimate of the emissions before and after application of the control option.
The capital costs of purchasing the control option should be determined from actual vendor price quotes for each proposed control option. Installation costs should also be based on vendor price quotes. If vendor price quotes are unavailable, elements of the installation cost may be estimated (Vatavuk 2002). To illustrate cost‐effectiveness calculations, let us consider a facility that is a major source of NOx emissions.
EXAMPLE 7.1 TOTAL CAPITAL COST
As part of a company’s ongoing pollution prevention program, an existing appliance coating operation is to be replaced by a minibell automatic electrostatic spray system. The company estimates that the coating operation is presently operating at a 50% transfer efficiency, and it has received a guarantee of 90% transfer efficiency with a new unit. The company operates 250 days/year and processes 200 appliance units per day. An average of 2 gal of paint are presently required to coat each unit. The coating material has a volatile organic compound (VOC) content of 5.0 lb VOC/gal solids. Information on the minibell system is given below. If the paint worth $5/gal shows that an annual profit will be realized by replacing the existing spray system with the more efficient minibell unit. Cost information on the proposed minibell system is given below.
- Installed cost = $1 125 000
- Operation and maintenance cost = $70 000/year
- Lifetime guarantee = 15 years
- Interest rate per purchase cost = 8%
SOLUTION
- Obtain the annual operating and maintenance cost. From the data given,
- Calculate the annualized capital cost, ACC.
- Calculate the TAC, if the minibell system is installed
- Calculate the total annual operating savings, TAS, if the minibell system is installed. Since the sprat system operates more efficiently, a savings will be realized because of the reduced paint usage. At 50% transfer efficiency only 1 gal of the 2 gal of paint used per unit is actually applied. The paint usage for the minibell system, operating at 90% transfer efficiency, is (1.0/0.9) or 1.11 gal. Thus, the gallons saved per unit is 2.0 − 1.11 = 0.89 gal. The total annual savings, TAS, becomes
- Calculate the annual savings.The savings, S, can be calculated by subtracting the result of step (3) from that of step (4).
Once a particular process scheme has been selected, it is common practice to optimize the process from a capital cost and O&M standpoint. There are many optimization procedures available, most of them too detailed for meaningful application to simple pollution prevention projects. These sophisticated optimization techniques, some of which are routinely used in the design of conventional chemical and petrochemical plants, invariably involve computer calculations.
EXAMPLE 7.2 COST‐EFFECTIVENESS CALCULATION
For a boiler operating at 100% of its operating capacity (50 Btu × 106), the following information was determined for the purposes of calculating the cost‐effectiveness of installing SCR as a control option. The facility is a major source of NOx emissions.
Given:
- Capital cost of control option = $1 500 000
- Capital recovery factor (CRF) = 0.1627 (assuming 10% interest for 10 years)
- Annual operating and maintenance costs = $98 000
- Uncontrolled emissions = 21 T of NOx per year
- Capture efficiency = 100%
- Control efficiency = 80%
SOLUTION
We insert the data into the following equations:



The result is
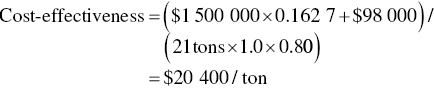
Inducing industries to adopt effective new production methods and pollution control technologies in timely fashion is a challenge for regulators everywhere. Environmental protection costs money, and the charges that will be incurred by a given enterprise depend on the nature and extent of the pollution it generates. These factors, in turn, are functions of the type and scale of production, the plant’s input, the technology used, and the size of the plant.
Generators of pollution range from private individuals and small business to municipalities, large corporations, and the government itself. Each polluting entity must decide how to invest in the socially desirable goal of a cleaner environment; influencing such decisions, inevitably, will be the benefit the entity expects to obtain from the investment.
When business owners consider how to implement the installation of modern pollution control technology, their decisions incorporate the results of comparative analyses of the costs and benefits of the investments contemplated. Later we shall present a case study focused largely on financial costs and benefits associated with biobased energy and products (Section 7.4). To provide the necessary background for this material, we turn now to some basics of cost estimation and capital investments.
Achieving a Responsible Balance
In the real worlds, taking socially desirable action for pollution prevention may not be in the best interest of an industry in the short run, since environmental protection costs money. The type of production, input used, technology employed, space used as well as plant size and the scale of production determine the nature and extent of pollution which, in turn, influence the abatement cost. Hence, the decisions of the profit maximizing private investor for implementation of pollution abatement measure are influenced by the benefit expected as a result of the investment required. On the other hand, the task of government planners and policy makers is to encourage industry to adopt modern production and pollution control technologies to provide a better environment for the society. In upgrading their facilities to meet the near antipollution regulations, industries turn for guidance to the principles of best available control technology (BACT).
Leave a Reply