While there are several practical definitions of zero effect or zero discharge (ZD) manufacturing, a ZD system is most commonly understood to be one that discharges no waste from a processing and manufacturing site. In such a manufacturing facility (see Figure 1.2) an absolute minimum amount of waste, “ideally zero,” is generated and leaves the plant. The only inputs to the facility are the raw materials needed to make salable products and energy. The only outputs are salable products and any by‐products as feedstocks to another plant. The wastes (in air, water, or as solid) or by‐products generated during manufacturing process are recovered using various technologies (Das 2005).
The materials and energy recovered from waste streams either are reused in the plant or are sold to another plant as feedstock. It is in practice, as well as in theory, possible to isolate some industrial facilities almost completely from the environment by recycling all wastes into materials that can then be manufactured into consumer products. An example of such a facility is a coal‐fired power plant. An electron beam–ammonia conversion unit adds ammonia to the effluent gases, which it then irradiates electronically, producing ammonium nitrate and ammonium sulfate that are sold as feedstock to fertilizer manufacturing. The details are given in Section 9.2.3.
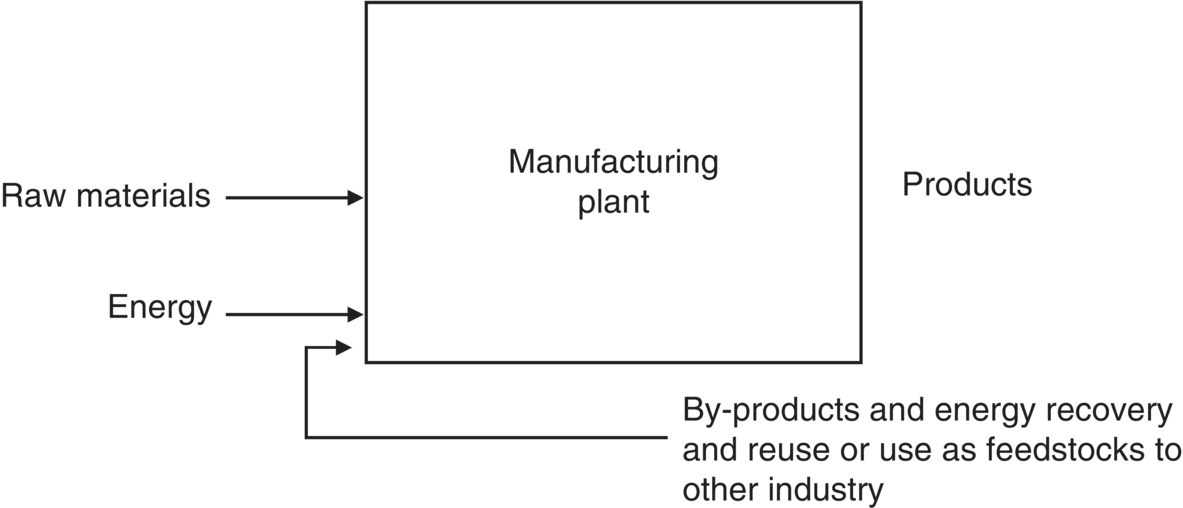
The concept of Zero Emissions was inspired by the business programs of zero defects (total quality management), zero inventory (just‐in‐time), and zero accidents (workplace safety), and while its driver is improved business performance, the environmental benefits are also significant.
The basic premise of Zero Emissions is converting wastes from one industry to the material input of another industry. The application and development of Zero Emissions systems will be the purview of industry, specifically manufacturers and consulting engineering firms. To a degree, the move toward Zero Emissions is already happening with pollution prevention, waste minimization, and design for the environment. While these systems require further improvement, industries employing them have seen the benefits already.
But it is important to understand that some manufacturing processes inherently produce wastes, even after all reasonable efforts at pollution prevention. Thus, in some cases the use of a conversion technology may be more appropriate than a program of pollution prevention: many industrial wastes can be processed to render them viable as material inputs to another industry or to part of an industrial cluster of several connected industries.
Leave a Reply