An important consideration when using aluminium alloys (and other materials) in aircraft structures is softening that occurs at elevated temperature. Care must be taken when selecting materials for supersonic aircraft to ensure structural weakening does not occur owing to excessive heating. Material properties such as stiffness, strength, fatigue resistance and toughness are degraded at high temperature. The loss in stiffness and strength of an aluminium alloy with increasing temperature is shown in Fig. 8.14. The sensitivity of the engineering properties to temperature differs between alloy types, but they all experience a large reduction in their mechanical properties when heated above 100–150 °C.
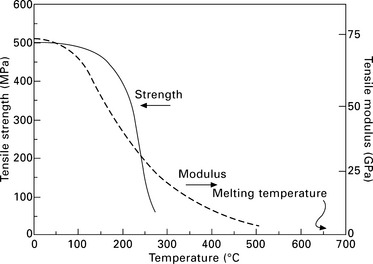
8.14 Effect of temperature on the tensile properties of an aluminium alloy.
Thermal softening is a key factor in the selection of aluminium alloys for aircraft structures that experience a large temperature rise as a result of frictional skin heating. The nose section, leading edges and skins of aircraft are heated owing to friction caused by molecules in the atmosphere moving across the aircraft surfaces at high speed. Frictional heating is generally not a problem when flying at subsonic speeds because the surface temperature does not rise much above 80–90 °C, which is below the temperature at which aircraft materials experience significant softening. However, higher temperatures are generated when flying at supersonic speeds. The hottest parts of the aircraft are the nose cone and leading edges of the wings and tail sections, with temperatures in excess of 150 °C being reached at Mach 2. As Fig. 8.14 shows, at 150 °C the modulus and strength is 10–20% below room temperature. Temperatures exceeding 1000 °C are experienced during re-entry of spacecraft such as the space shuttle and temperatures above 500 °C can occur in ultra-high speed aircraft. At these temperatures, the aluminium must be thermally protected by a heat shield, such as ceramic tiles.
Leave a Reply