The use of non-age-hardenable wrought alloys in aircraft is limited because they lack the strength, fatigue resistance and ductility needed for structural components such as skin panels, stiffeners, ribs and spars. The proof strength of most tempered non-age-hardenable alloys is below 225 MPa, which is inadequate for highly stressed aircraft structures. However, these alloys are used in some nonstructural aircraft parts and therefore it is worthwhile to briefly examine these materials.
The 1000, 3000, 5000 and most of the 4000 alloys cannot be age-hardened via heat-treatment processing. Solid solution strengthening, strain hardening and grain size control determine the strength of non-age-hardenable alloys. The improvement in strength achieved by solid solution strengthening is modest because most of the alloying elements have low solubility limits in aluminium at room temperature. The inability to dissolve large amounts of alloying elements into either interstitial or substitutional sites within the aluminium crystal structure means that very little strengthening can be achieved. Figure 8.2 shows the increase to the yield strength of high-purity aluminium from solid solution strengthening with several important alloying elements. Only a small improvement in strength is achieved. Strain hardening and grain size control are more effective mechanisms for strengthening non-age-hardenable alloys. For example, Fig. 8.3 shows the improvement in yield and ultimate tensile strengths of pure aluminium with percentage cold-working.
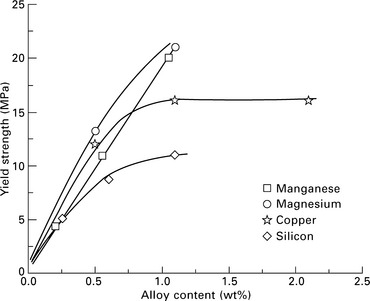
8.2 Effect of different alloying elements on the solid solution strengthening of pure aluminium in the annealed condition.
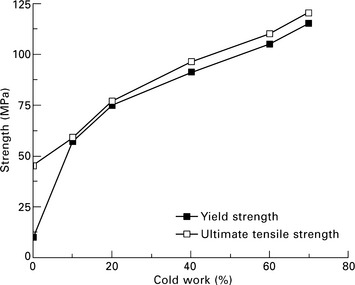
8.3 Effect of amount of cold working (strain hardening) on the yield and ultimate tensile strengths of pure aluminium.
1000 series aluminium alloys
The 1000 series is the highest purity form of aluminium alloys. An alloy is classified in the 1000 series when its aluminium content is greater than 99%. Only rarely are very small amounts of alloying elements deliberately added to 1000 metals. Instead, the trace amounts of impurity elements (e.g. Cu, Fe) are inadvertently extracted from the ore (bauxite) in the production of aluminium metal after extraction, refinement and processing. It is difficult and expensive to completely remove impurities, and so small amounts are left in the metal. Despite their low concentration, impurities can have a marked effect on the mechanical properties. For example, impurities such as copper, silicon and iron in amounts of less than 1% can increase the yield strength and ultimate tensile strength by as much as 300 and 40%, respectively. These improvements in strength are caused by solid solution strengthening and refinement of the grain structure.
The 1000 series alloys are characterised by low yield strength, poor fatigue resistance and high ductility. The yield strength of most annealed 1000 series alloys is below 40 MPa. The low strength of 1000 alloys makes them unsuitable as structural materials on aircraft. However, occasionally these alloys are used in nonstructural aircraft parts where high strength is not required but weight and cost are important. Examples of the use of 1000 alloys include cowl bumps and scoops on small civil aircraft. Alloy 1100 is sometimes used for aircraft fuel tanks, fairings, oil tanks, and in the repair of wing tips and tanks.
3000 series aluminium alloys (Al–Mn)
The main alloying element in this series is manganese, which provides some improvement in strength by solid solution hardening. It is not possible to age-harden 3000 alloys because manganese does not form precipitates in aluminium upon heat treatment. The yield strength of most 3000 alloys is below 200 MPa and, for this reason, they are rarely used in aircraft. The alloy 3003 Al, which contains 1.2% Mn, is used as a nonstructural material in fairing, fillets, tanks, wheel pants, nose bowls and cowlings in some aircraft. 3000 alloys are mostly used in non-aerospace components, such as automotive components (e.g. radiators, interior panels and trim).
4000 series aluminium alloys (Al–Si)
The 4000 alloys contain significant amounts of silicon. These alloys cannot be strengthened by heat treatment, unless magnesium is present to form high-strength precipitates (Mg2Si). The use of 4000 alloys in aircraft is limited because a brittle silicon phase can form in the aluminium matrix which reduces the ductility and fracture toughness. 4000 alloys are used in non-aerospace applications, in particular as brazing and welding filler materials.
5000 series aluminium alloys (Al–Mg)
The main alloying element in these alloys is magnesium, which is usually present in concentrations of a few percent. Magnesium forms hard intermetallic precipitates in aluminium (Mg2Al3) that increase the strength of the alloy. However, the formation and growth of these precipitates cannot be controlled by heat treatment, and therefore the 5000 series alloys are not age-hardenable. As with the other non-age-hardenable alloys, 5000 alloys are used occasionally in nonstructural aircraft parts. For example, the alloy 5052 Al, which contains 2.5% Mg and 0.25% Cr, is one of the highest strength non-age-hardenable alloys that is available, and is used in wing ribs, wing tips, stiffeners, tanks, ducting and framework.
Leave a Reply