The final stage in the fabrication of aircraft metal structures involves the machining operations of milling, routing, trimming and drilling. Metal components are rarely in their final shape at the end of processing, and it is necessary to remove excess material using a variety of machining processes. Increasingly, these processes are being carried out automatically using numerically controlled machines to increase production rates and accuracy. Some components are fabricated to the near-net shape and require only a small amount of material (under 5–10% of the weight) to be removed. Components with intricate shapes can require a large amount of machining (up to 90%) and the milling, routing, trimming and drilling processes which are used are critical to the production rate and quality. Material removal generally becomes more difficult with increasing hardness, and the machining of hard metals such as titanium is performed using specialist methods such as laser assisted milling. Table 7.2 ranks materials in order of increasing difficulty and cost of machining.
Table 7.2
Machining energy requirements and machining costs for various metals and composites used in aircraft
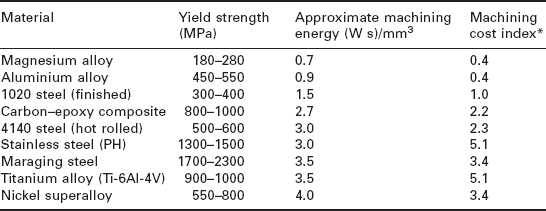
⁎Machining cost index relative to high-strength aluminium alloy. If it costs $1 to machine aluminium then it costs $3.40 to machine the maraging steel.
Milling is a common machining process that involves the use of a multi-tooth cutter to remove metal from the workpiece surface to create flat and angular surfaces and grooves. Routing refers to the shaping of apertures or edge trimming of components in flat and shaped panels, and is performed using a cylindrical, flat-nose cutting tool. Trimming involves removing excess material around the edges of a fabricated component, and is performed using various methods from simple techniques such as cutting blades and routers to precision methods such as high-powered laser cutting and water-jet cutting.
Drilling is a major operation in the pre-assembly of aircraft because of the large number of fasteners, bolts, screws and rivets required to connect the many airframe components. Drilling of panels and subsequent fastener installation is one of the more time-consuming operations in aerospace manufacture (for both metals and composites). Drilled holes are also a common source of damage in aircraft structures, particularly cracks growing from fastener holes, and therefore correct drilling and fastener installation is essential for structural integrity. A commercial airliner can have as many as 1.5 to 3 million fasteners whereas a typical fighter aircraft might have up to 300 000. Drilling is broadly classified as either hand, power feed, automated drilling or automated riveting. The majority of fastener holes in aircraft structures are produced using automated drilling equipment, which ensures high accuracy in hole tolerance and rapid production. Automated drilling units are custom designed and built for specific aircraft structures. The drilling is automatically controlled with the capability to change speed and feed rates when boring through different materials.
Hole drilling of most metals is performed using standard twist drill bits. High hardness steel bits are used for drilling aluminium and magnesium components. Hard-coated or cobalt grades of high-strength steel are used in drills for hard metals such as titanium alloys to ensure long drill life. Drilling is performed at a carefully controlled speed to avoid overheating and other damage to the hole. As a general rule, the rotational speed of the drill bit should be reduced as the hole size gets larger, or when the metal gets thicker or harder. Typical maximum drill speeds for aluminium range from 1000 rpm for 12 mm wide holes to 5000 rpm for 4 mm holes. Titanium alloys are drilled at slower speeds because of their higher hardness: 150 rpm for 12 mm holes up to 700 rpm for 4 mm holes.
Automated riveting machines are widely used throughout the aerospace industry, and have the capability to drill the hole, inspect the hole for quality and tolerance, grip the rivet, apply sealant over the rivet (if required), and then install the rivet by squeezing. Drilling and fastener installation can be achieved in just a few seconds for each hole using automated processes involving high-speed robotic machines.
After the hole is drilled it is deburred (if necessary) then cleaned of any swarf and other contamination before the fastener is installed. Many different fasteners are used in aircraft assembly, with the most prevalent being solid rivets, pins with collars, bolts with nuts, and blind fasteners. The selection of the fastener type depends on its ability to transfer load across the joint connection, compatibility with the metal structure (to avoid corrosion damage), and ease of installation. Aluminium rivets are by far the most widely used fasteners for joining metal structures. Rivets should only be used in joints that are primarily loaded in shear; tension loads must be avoided to minimise the risk of rivet pull-out. The most common alloy used in rivets is 2117-T4 aluminium (called an AD rivet). Other types of aluminium rivets, such as 2024Al-T4 and 7075-T73, are used instead of the AD rivet when higher strength is required. Steel fasteners are used in undercarriage and other highly loaded components.
Fatigue cracking from fastener holes is a major problem with old aircraft. The aerospace industry uses both cold working of the fastener hole and interference fit fasteners to resist fatigue damage by forming a residual compressive stress in the metal surrounding the hole. Cold work is introduced by pulling a mandrel through the hole that expands sufficiently to plastically deform by compressing the material surrounding the hole. An interference fit fastener is then installed into the cold-worked hole. This type of fastener expands during installation and thereby exerts a compressive stress onto the material bordering the hole. The ability of cold working and interference fit fasteners to improve the fatigue life of metals is shown in Fig. 7.11 for an aircraft-grade aluminium alloy. These methods can increase the fatigue life above that of the parent metal structure (without a hole) because of the residual compressive stress resisting fatigue cracks that grow under tension loads.
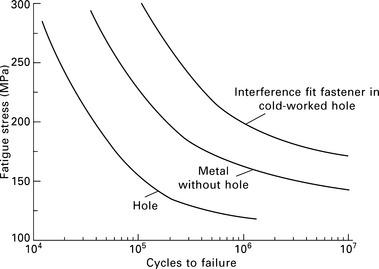
7.11 Improvement in the fatigue life of 2024-T851 aluminium owing to cold working and interference fit fasteners adapted from F. C. Campbell, Manufacturing technology for aerospace structural materials, Elsevier, 2006.
Leave a Reply