Forging
Forging is a forming process used to strengthen and shape thick sections of cast metal. The process involves plastically deforming the metal under high compressive forces inside a die cavity, as shown in Fig. 7.2. Deformation usually occurs by repeated strokes or blows applied using hammers, mechanical presses or hydraulic presses. The metal is plastically deformed into the shape of the cavity, and is then removed for machining into the finished part. Forging is performed at room temperature, called cold working, or at elevated temperature to make the metal soft and ductile, called hot working. Most aerospace metals are hot forged; for example the 2000 aluminium alloys are forged at 425–460 °C whereas the 7000 alloys are forged at 400–440 °C.
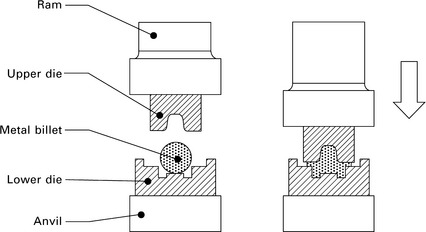
Forging improves the strength, ductility, fatigue endurance and impact toughness by strain hardening and grain refinement that occurs when the metal is plastically deformed. Forging is also used to break up segregation of the alloying elements and heal porosity in the cast metal. Pores within the metal are squashed and welded closed under the high forging pressure.
The aluminium, magnesium, titanium and steel used in aircraft structures are in almost every case used in the forged (rather than the as-cast) condition. Forged metal alloy is preferred for aircraft bulkheads and other highly loaded parts because the forging process allows for thinner cross-sectional product forms before heat treatment and quenching, enabling superior properties. Forging can also create a favourable grain flow pattern that increases both fatigue life and fracture toughness of the various metal alloys used in aircraft. The only metal type that is not always forged are the nickel-based superalloys used in jet engines because brittle intermetallic inclusions in the metal fracture under the high forming loads and these fractures act as failure initiation sites so that alternative forming processes must be used.
Extrusion
The forming process of extrusion involves pushing metal through a die under high compressive force, as shown in Fig. 7.3. Extrusion is somewhat analogous to squeezing paste out of a toothpaste tube. The cast metal (called a billet), which is hot or cold, is placed inside the die cavity and then squeezed through an annular opening in the die under force applied by a hydraulic ram. The metal effectively squirts out as a continuous bar having the same cross-sectional shape as the die opening. The extrusion is then fed onto a run-out table where it is straightened by stretching and cut to length. Extrusion is used to produce components of uniform cross-section such as beams and rods. Extruded ‘T’, ‘H’ ‘J’ and ‘L’ shaped sections are used for wing stringers and fuselage frames. High strength aerospace alloys, including 2000 and 7000 aluminium alloys, are referred to as ‘hard’ alloys because they are difficult to extrude. These extrusions are often performed at high temperature to soften the metal and thereby aid plastic flow through the die opening.
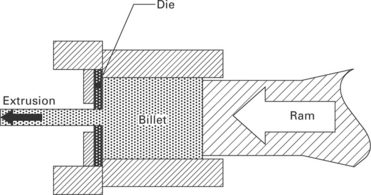
Roll forming
Rolling is a process that plastically deforms thick metal under heavy rollers into thin sheet. Rolling is used to produce high-strength sheet metal for skin panels, stringers, frames and other thin-walled structures in aircraft. Figure 7.4 shows the rolling process, which involves feeding metal stock between counter-rotating rollers which squash it into a thin, long strip. The rollers are spaced so that the distance between them is slightly less than the reduced thickness of the metal. The rolling process usually begins with hot rolling of the ingot to close any pores and break down the coarse grain structure of the casting. The thickness of the ingot is reduced progressively by a series of rolling operations. The reduction in thickness with each pass between the rollers is determined by the type of material and other factors. A large reduction in thickness with one pass is possible with soft metals whereas multiple passes are required for high-strength materials to achieve the same decrease in thickness. Rolled products are classified as either sheet (with a thickness between 0.15 and 6.3 mm) or plate (thickness greater than 6.3 mm). Widths can range up to about 2500 mm. Rolled aluminium sheet and plate in the range of about 1 to 10 mm is used in the fuselage skin and stringers. Thicker plate (25 to 50 mm) is used for wing skins, and the thickest plate, up to 200 mm, is used for bulkheads, wing spars and supporting structures.
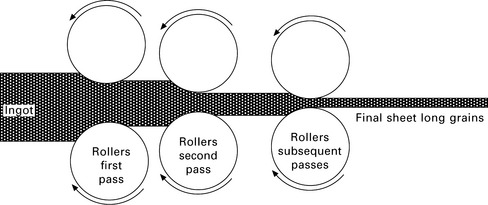
Sheet forming
Sheet forming is used to produce curved panels for large structures such as the fuselage. The process involves clamping the ends of rolled metal sheet (usually thinner than 6 mm) and then stretching over a forming block to the desired shape. The pressure used to stretch the sheet is applied through male or female dies or both. Figure 7.5 shows a sheet forming process that combines a punch (or metal male die) and a rubber female pad to produce curved plate. The sheet is pressed into the rubber pad under force applied through the punch. The flat sheet is plastically deformed into the punch shape without any major change in the sheet thickness.
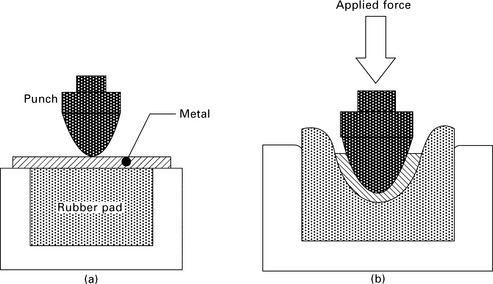
7.5 Sheet forming: (a) before forming; (b) after forming.
Superplastic forming
Superplastic forming is a specialist process used for deforming metal sheet to extremely large plastic strains to produce thin-walled components to the near-net shape. Stretching of the sheet during superplastic forming is much higher than with rolling and sheet forming. Superplastic forming involves stretching the material at least 200% beyond its original size, although the deformation can exceed 1000% with some metals. Figure 7.6 shows the basic steps involved in superplastic forming of metal sheet. The sheet is placed within a die cavity and then heated while high gas pressure is evenly applied to plastically deform the metal at very large strains into a complex shaped, single-piece component. Figure 7.6 illustrates the simplest type of superplastic forming; however, there are many variations to the process depending on the shape and thickness of the part. During superplastic deformation the metal becomes uniformly thinner over the entire part, and does not experience necking (or local thinning) which often leads to tensile fracture. Also, during the forming process, the material does not develop internal cavities, which is another common cause of tensile failure.
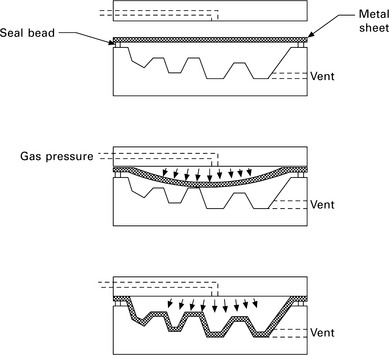
7.6 Superplastic forming process.
Metals must have very high plasticity to be processed by superplastic forming. Metals with superplastic properties have a fine and equiaxed grain structure, typically less than 10–20 μm. The grain structure must be stable at the high temperatures used in the superplastic forming process, and this is often achieved using a dispersion of thermally stable particles in the metal. These particles pin the grain boundaries and thereby retain the fine grain structure at high temperature while also providing high resistance to cavitation (void formation). Metals with these properties become superplastic at high temperature, typically one-half of their absolute melting temperature. For example, titanium is superplastic at about 900 °C and aluminium at 450–520 °C. The superplastic metal is soft and ductile at a temperature high enough to allow it to plastically stretch over large strains without tearing or breaking. The mechanism of superplasticity relies on the sliding of grains past each other in a creep-type deformation process together with atomic diffusion processes within the crystal structure that aid plastic flow.
Superplastic forming is used by the aerospace industry as an economical process to fabricate complex components to the near-net shape as a single piece. This reduces the number of individual parts and the assembly cost often associated with making complicated components. For example, a single sheet can be formed into a complex arrangement of ribs, stiffeners and skin as a single-piece part. Superplastic forming is credited with weight and cost savings on virtually every modern aircraft. Figure 7.7 shows an inner door skin for an aircraft made by superplastic forming of aluminium alloy. This component replaced the conventional door component that was built up from 15 to 25 parts. A weight reduction of 20% and cost saving of 40% was achieved using superplastic forming rather than conventional manufacturing of the door panel. However, superplastic forming is not always the most economical process. The superplastic forming process is slow and material costs are higher than for conventional alloys. Superplastic forming usually offers an economic advantage when a small to medium number of complex parts, which are normally manufactured with expensive materials having low formability, are required.
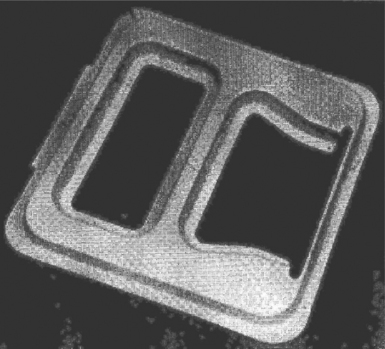
7.7 Superplastic formed access-door panel for an aircraft reproduced with permission from F. C. Campbell, Manufacturing technology for aerospace structural materials, Elsevier, 2006.
Leave a Reply