There are many commercial processes to produce castings for processing into aircraft components. Casting processes are usually classified into two broad groups distinguished by the mould type: reuseable casting moulds and single-use casting moulds. This section briefly describes the processes commonly used for casting metals for aircraft structures and engines. The processes are permanent mould casting, pressure-die casting and single-crystal casting, which are reusable moulding methods; and sand casting and investment casting, which are single-use moulding methods. These processes account for the majority of castings for aircraft structural components.
Permanent mould casting
Permanent mould casting is a process for producing a large number of castings using a single reusable mould. The casting process simply involves pouring molten metal into a mould where it cools and solidifies. The mould is then opened, the casting removed, and the mould is reused. The mould is made from a high-temperature metallic material, such as cast iron or hot work die steel, which can withstand the repeated heating and cooling involved with large volume production.
Permanent mould casting produces metal with better dimensional tolerance, superior surface finish, and higher and more uniform mechanical properties when compared with metal solidified using sand casting (which is described in section 6.4.3), which is another popular casting process. Permanent mould castings have relatively high strength, toughness and ductility owing to the mould walls rapidly removing heat from the liquid metal. This generates a fast solidification rate which produces a fine grain structure in the cast metal. Disadvantages of permanent mould casting is the high cost of the reusable mould, and that the casting process is usually viable only when high-volume production can offset the cost or it is critical that high-quality castings are produced. The most common application of permanent mould casting in the aerospace industry is the casting of aluminium, titanium and steel ingots, which are then processed by working operations (e.g. forging, rolling) into aerospace structural components.
Pressure die casting
Pressure die casting involves squeezing molten metal into a mould cavity under high pressure and then holding the metal under pressure during solidification, as shown in Fig. 6.7. Pressure is applied by the action of a hydraulic piston ram that injects molten metal through a steel die and into the mould. The metal casting is removed from the mould following solidification, and the process repeated using the same permanent mould. The process is suitable for very high rate production because of the fast solidification rate of the casting. Many aluminium and magnesium alloys are cast using this method.
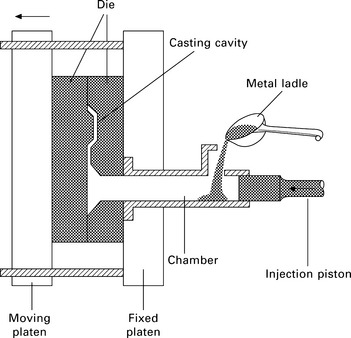
6.7 Pressure die casting (image from The Open University).
Sand casting
Sand casting involves the pouring of molten metal into a cavity-shaped sand mould where it solidifies (Fig. 6.8). The mould is made of sand particles held together with an inorganic binding agent. After the metal has cooled to room temperature, the sand mould is broken open to remove the casting. The main advantage of sand casting is the low cost of the mould, which is a large expense with permanent mould casting methods. The process is suitable for low-volume production of castings with intricate shapes, although it does not permit close tolerances and the mechanical properties of the casting are relatively low owing to the coarse grain structure as a result of slow cooling rate.
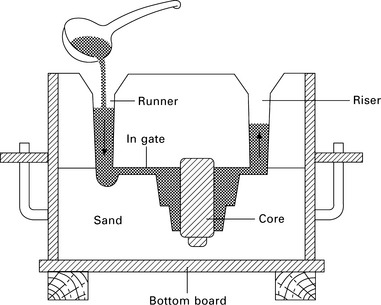
6.8 Sand mould casting (image from The Open University).
Sand casting is the process of choice for the aerospace industry for the economical production of small lot sizes. The industry uses sand casting for producing magnesium alloy and certain types of aluminium alloy components with complex shapes. Figure 6.9 shows the housing of an aircraft engine made using sand cast magnesium alloy. The housing is a thin wall component containing small diameter cooling holes, which demonstrates the capability of sand casting to produce complex shapes.
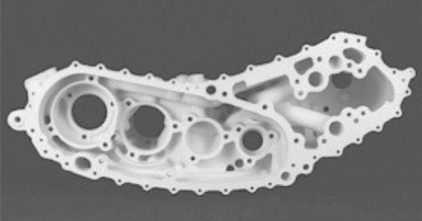
6.9 Sand cast magnesium gearbox housing.
Investment casting
Investment casting is generally used for making complex-shaped components that require tighter tolerances, thinner walls and better surface finish than can be obtained with sand casting. The distinguishing feature of investment casting is the way the mould is made. A pattern of the part is made with wax, which is then dipped into fine ceramic slurry that contains colloidal silica and alumina. The mould is dried and heated inside an oven to melt out the wax leaving behind a ceramic shell mould for casting. The investment casting method, also called the lost wax process, is used for precision casting of aerospace components such as gas turbine blades. The investment casting of aluminium alloys results in lower strength than sand castings, but offers tighter tolerances, better surface finish and the capability to produce thin-walled sections.
Directional solidification and single-crystal casting
Many mechanical properties are improved by reducing the grain size. A metal with a fine grain structure has higher strength, ductility, toughness and fatigue resistance than the same metal containing coarse grains. An important mechanical property which opposes this trend is creep, which is the plastic deformation of a material when sustaining an applied elastic load for a long period of time. The resistance of metals against creep deformation increases with their grain size. This occurs because an important process driving creep is sliding of the grain boundaries at high temperature. Increasing the grain size reduces the number of grain boundaries per unit volume of material, and this reduces grain boundary sliding and thereby. Therefore, materials that require high creep strength, such as the nickel superalloys used in the hottest sections of jet engines, must have a coarse grain structure. Specialist casting methods are used to produce very large grains during the solidification of superalloys and other metals for high-temperature applications. Two methods used to improve the creep properties of high-temperature metal alloys are directional solidification and single-crystal casting (Fig. 6.10).
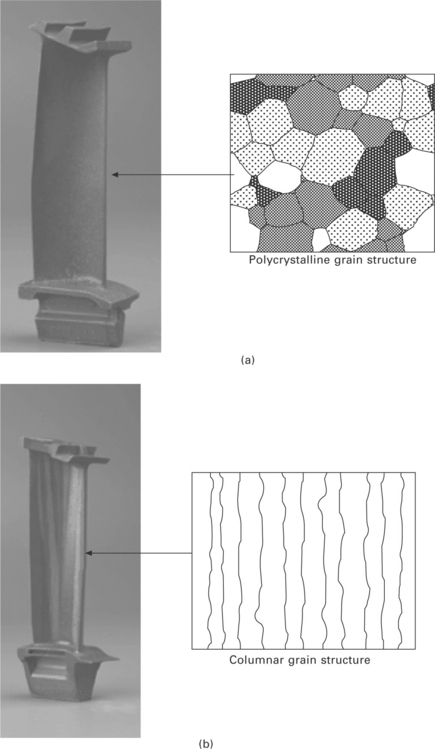
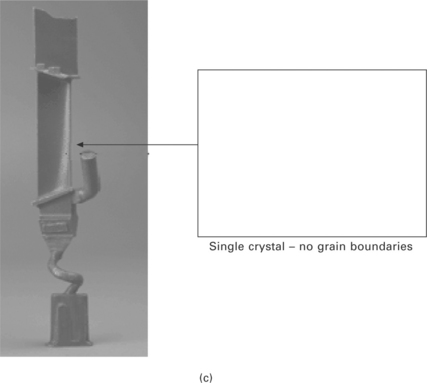
6.10 Turbine blade made with nickel-based superalloy using: (a) investment casting resulting in a polycrystalline grain structure, (b) directional solidification resulting in a columnar grain structure and (c) single crystal solidification resulting in no grain boundaries.
Directional solidification involves slowly withdrawing the cast metal from the furnace to produce a coarse, columnar grain structure. Molten metal is rapidly cooled directly onto a chill plate immediately upon leaving the furnace. The chill plate generates a steep temperature gradient along the casting, with the temperature dropping several hundred degrees within a short distance from the exit of the furnace. The chill plate moves away from the furnace at a speed of only a few inches per hour. The sharp temperature gradient and slow solidification rate generate the conditions that allow the solid/liquid interface to advance slowly in the heat flow direction, thus forcing the grains to grow as very long columns. Directionally solidified metal consists of long, thin grains in the solidification direction with very few or no transverse grain boundaries. When the cast metal is externally loaded in the grain direction it is the transverse grain boundaries which cause creep deformation, and minimising their presence by directional solidification improves the creep resistance.
An advance on the directional solidification process is single-crystal casting, which is used to produce metals with exceptional creep resistance. The development of single-crystal casting has led to a 100 °C improvement in temperature capability over conventionally cast alloys with a polycrystalline grain structure. More than 1.5 million high-pressure gas turbine blades made by single-crystal casting are currently in service on civil and military aircraft. Single-crystal casting is increasingly being used for producing nozzle guide vanes. Single-crystal metals are produced by allowing just one grain to grow into the main body of the casting. The mould end has a constriction in the shape of a corkscrew through which only one crystal can pass. A single crystal grows through the constriction and into the main section of the casting without the formation of grain boundaries. The solidified casting consists of a single-crystal metal that has exceptional resistance to creep softening and thermal shock owing to the absence of grain boundaries.
Leave a Reply