Shape and ingot castings
Casting is the operation of pouring molten metal into a mould and allowing it to solidify. The pouring temperature is usually 50–180 °C above the melting point of the metal alloy. There are two broad classes of casting operations known as shape casting and ingot casting. Shape casting involves pouring the liquid metal into a mould having a shape close to the geometry of the final component. The shape casting is removed from the mould after solidification, and then heat treated and machined into the finished component. Ingot casting, on the other hand, involves pouring the metal into a mould having a simple shape, such as a bar or rod. After cooling, the ingot is strengthened and shaped by working processes such as forging, extrusion or rolling. Both shape and ingot castings are used in the production of aerospace components. However, primary aircraft structures are most often fabricated from ingot castings.
Solidification of castings
Solidification of the metal within shape or ingot casting moulds has a strong influence on the microstructure and mechanical properties. The solidification process is complex and does not simply involve the metal changing immediately from liquid to solid when cooled to the freezing temperature. When molten metal is cooled below the equilibrium freezing temperature there is a driving force for solidification and it might be expected that the liquid would spontaneously solidify. However, this does not always occur – pure metals can be cooled well below their equilibrium freezing temperature without solidifying. This phenomenon is known as undercooling or supercooling. For example, liquid aluminium can be undercooled to 130 °C below the equilibrium freezing temperature (660 °C) and held there indefinitely without solidifying. Similarly, pure nickel can be supercooled as much as 480 °C below the freezing temperature (1453 °C) before becoming solid. The reason for this behaviour is that the transformation from liquid to solid begins with the formation of tiny solid particles or nuclei within the melt. The nuclei develop spontaneously in the liquid as nano-sized particles composed of several dozen atoms arranged in a crystalline structure. The nuclei are freely suspended in the melt and are surrounded by liquid metal. The creation of solid nuclei in this way is called homogenous nucleation. The nuclei often dissolve back into liquid before they grow to a critical size that is thermodynamically stable, and it is this instability that allows the large supercooling of pure metals. It is only when nuclei grow beyond a critical size, which requires cooling of the liquid well below the equilibrium freezing temperature, that the solidification process stabilises and the metal completely solidifies.
In practice, large undercooling does not occur with metal alloys because solidification occurs by a process called heterogeneous nucleation. Most alloys freeze within about 1 °C of their equilibrium melting temperature because the nucleation of ultra-fine solid nuclei occurs at free surfaces, such as the mould walls or solid impurity particles in the melt. The heterogeneous nucleation of solid nuclei at pre-existing surfaces gives them greater stability than the nuclei which develop by homogenous nucleation. Once the nuclei have formed by heterogeneous nucleation they grow by atoms within the liquid attaching to the solid surface. At the equilibrium freezing temperature, a metal contains an extremely large number of nuclei. Each nucleus forms the embryo to a single grain, and the grains grow until no liquid remains and the metal has completely transformed into a polycrystalline solid. The sequence of events in the solidification of a metal under the conditions of heterogeneous nucleation is presented in Fig. 6.2.
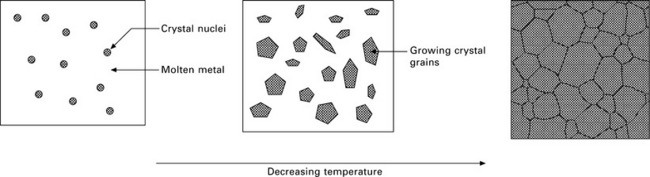
6.2 Solidification sequence for a metal.
Structure of castings
Chill, columnar and central zones
The solidification of shape and ingot castings often occurs in three separate phases, with each phase developing a characteristic arrangement of grain sizes and shapes. The grain structures through the section of an ingot from the mould wall to the centre are shown in Fig. 6.3. From the surface to core these regions are called the chill zone, columnar zone and central zone, and each has a distinctive grain structure. The solidification process that leads to these different grain structures is shown schematically in Fig. 6.4.
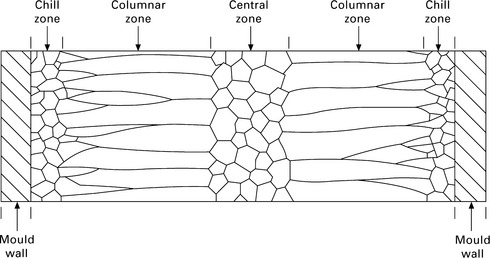
6.3 Section through a casting showing the formation of the grain structures during solidification reproduced with permission from R. E. Reed-Hill, Physical metallurgy principles (2nd edition), Van Nostrand Company, New York, 1973.
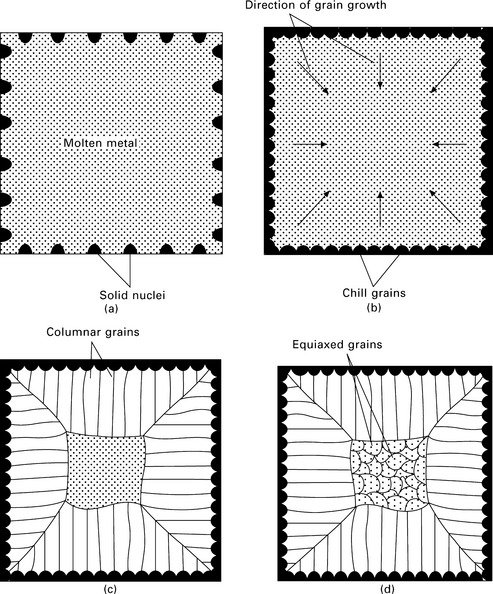
6.4 Solidification process comprising: (a) formation of solid nuclei at the mould walls by heterogeneous nucleation; (b) growth of the chill zone from the mould walls into the melt; (c) growth of columnar grains; and (d) final solidification of casting by formation of equiaxed grains in the central zone.
The chill zone is a thin band of randomly orientated grains at the surface of the casting. This is the first phase to develop during solidification because the mould surface rapidly cools the metal below the melting temperature. Many solid nuclei particles are created by heterogeneous nucleation at the mould wall and grow into the liquid to form the chill zone. Each nucleation event produces an individual crystal, or grain, in the chill zone, which then grows. The grains grow until they impinge on another grain, when the growth process stops.
When the pouring temperature of the molten metal into the mould is too low, the entire casting rapidly cools below the melting temperature. The nuclei particles that develop at the mould walls break away and are swept throughout the melt under the turbulence created by pouring. When this occurs the chill zone, which consists of equiaxed grains, extends through the entire casting and no other zones develop. However, most casting is performed with a high pouring temperature that keeps the metal at the centre above the melting temperature for a long time. Under these conditions, the columnar zone develops from the chill zone.
The columnar zone forms by the solidification of liquid metal into elongated grains. The columnar grains grow perpendicular to the mould wall by a solidification process involving dendrites. When the temperature falls in the liquid just ahead of the solid/liquid interface then it becomes unstable and crystalline stalks known as dendrites grow out from the interface. Secondary and tertiary dendrite arms grow out from the primary stalk, and the branched dendrite structure often appears like a miniature pine tree. (Dendrite comes from the Greek word dendron that means tree). Dendrites have a primary arm that extends from the solid–liquid interface, secondary arms that branch from it, and tertiary arms that branch from the secondary arms. During solidification a number of dendrites of almost equal spacing are formed and they grow parallel to each other as depicted in Fig. 6.5. The growth direction of dendrites depends on the crystal structure of the metal; fastest growth occurs along the most energetically favourable direction. Dendrites develop into columnar grains which grow in the direction opposite the heat flow, or from the coldest towards the hottest regions of the casting. Each crystal that is formed consists of a single dendrite. During solidification the turbulent motion of molten metal ahead of the solid–liquid interface may break off dendrites and carry them into the melt. These dendrites act as nuclei for more grains and multiply the number of grains that nucleate in the liquid.
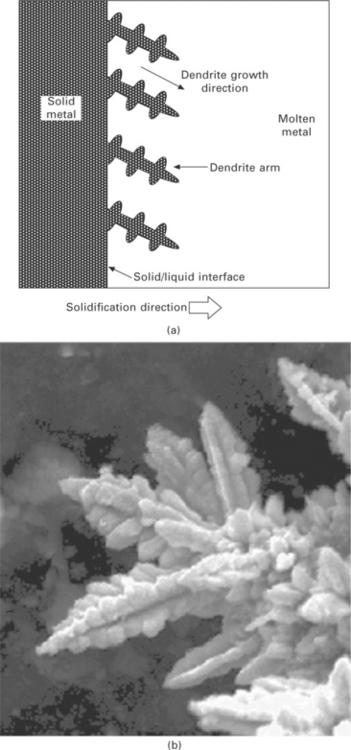
6.5 Dendritic growth into the liquid from the solid/liquid interface: (a) schematic, (b) photograph.
The metal sometimes continues to solidify in a columnar manner until all the liquid has solidified. More often, however, a central zone (also called the equiaxed zone) develops at the core of the casting. The equiaxed zone contains relatively round grains with a random orientation, and they often stop the growth of columnar grains. The amount of the final cast structure that is columnar or equiaxed depends on the cooling rate and alloy composition. A sharp thermal gradient across the solid–liquid interface owing to rapid cooling encourages columnar solidification whereas a low thermal gradient promotes equiaxed solidification.
Grain refinement of castings
The mechanical properties of metals are dependent on the grain structure. As described in the yield strength of metals increases when the grain structure becomes finer. Other properties such as ductility, fracture toughness and fatigue resistance are also improved by reducing the grain size. Therefore, it is often desirable to minimise the grain size in cast structural alloys. (The exception is the casting of metals requiring creep strength at high temperature, such as nickel superalloys used in gas turbine blades and discs, when a coarse grain structure is beneficial).
Grain size is controlled by the pouring temperature and solidification rate; lower pouring temperatures and faster solidification rates promote a finer grain structure. Mould walls are often chilled to increase the solidification rate and thereby refine the grain structure. Grain size is also controlled by the use of inoculates or grain refiners, which are chemicals added to the melt to promote many sites for heterogeneous nucleation during solidification. Inoculates act as the nuclei to which the atoms of the molten metal attach to transform from the liquid to solid states. For example, small amounts of titanium (0.03% by weight) and boron (0.01%) are added to liquid aluminium alloys to promote grain refinement. The elements react to create tiny inoculating particles of aluminium titanium (Al3Ti) and titanium diboride (TiB2) which cause a large reduction in grain size. Grain refinement is also an important strengthening process for magnesium alloys used in aerospace components. The Mg–Al and Mg–Al–Zn alloys are grain refined with carbon-containing compounds which form inoculating particles of aluminium carbide (Al4C3 or AlN.Al4C3).
Casting defects
Stringent regulations apply to the quality of metal castings used as the stock material for primary aircraft structures. Castings must not contain defects that compromise structural integrity and could cause unexpected failure of components. Casting defects that can cause structural failures include porosity, shrinkage and intermetallic inclusion particles. The nonuniform distribution of alloying elements in the casting, which is called segregation, is another problem because it leads to nonuniformity in the mechanical properties. In other words, discrete regions of soft and hard metal can exist within the same component owing to alloy segregation.
Porosity and shrinkage
Porosity occurs in the form of irregularly shaped cavities known as blowholes or long tubular cavities called wormholes (Fig. 6.6). Molten metals often contain dissolved gases such as hydrogen and nitrogen which develop into gas bubbles during cooling of the liquid and then become trapped by the solid growing around them. Blowhole porosity consists of small and irregularly shaped cavities filled with trapped gas. Blowholes can also form by the shrinkage of the metal during solidification. The amount of shrinkage experienced by aerospace alloys is given in Table 6.2. Shrinkage is a major problem with aluminium castings because the material contracts by anywhere from 3.5 to 8.5% during solidification, resulting in a significant number of blowholes and cavities. To avoid shrinkage, a reservoir of molten metal (called a feeder or riser) must be placed on the casting to feed liquid metal into the mould cavity.
Table 6.2
Average shrinkage values during solidification of aerospace metals
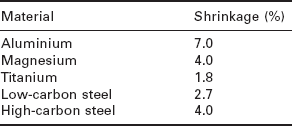
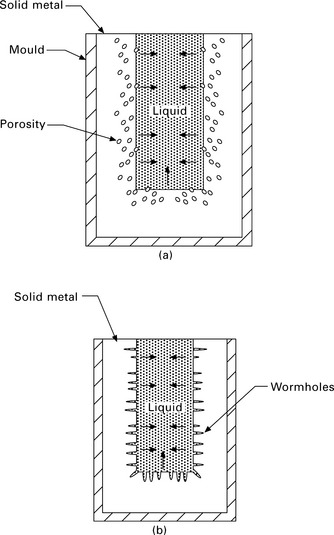
6.6 Two forms of gas porosity: (a) blowholes and (b) wormholes formed during solidification of metal castings.
Wormhole porosity occurs when gas bubbles grow in length at the same rate as the liquid–solid interface moves. The gas bubbles form worm-shaped holes that grow in the heat flow direction from the casting. Both blowholes and wormholes are detrimental to the structural integrity of the casting, but can be removed under the extreme pressure of hot working which squashes the holes and welds their sides together. When the welds are successful, the holes are eliminated and any gas inside the cavities is absorbed into the solid casting.
Inclusion particles
Large inclusion particles are another defect often found in castings. These particles may form during the casting of metals that are strengthened by precipitation hardening, which includes most of the structural aerospace alloys. During the casting and solidification process, alloying and impurity elements react with the base metal to form inclusion particles that are extremely brittle. When the particles are above a critical size (typically 1–2 mm) they easily fracture under load, which forms the site for crack growth through the cast metal. Cracks may also occur at the interface between the inclusion particle and metal. Another problem is that the inclusion and metal have different coefficients of thermal expansion, which results in thermally induced stresses in the metal surrounding the inclusion during solidification. As a result, the inclusion acts as a stress concentration point in the cast metal which may lead to cracking at low stress. It is essential that inclusion particles are removed by solution heat treatment before the metal is used in an aircraft, otherwise cracking and failure can occur.
Segregation of alloying elements
Segregation of the alloying elements is another problem with castings. There are two types of segregation, macrosegregation and microsegregation, which occur at different levels in the casting. Macrosegregation is where the average alloy composition varies over a large distance through the casting. Macrosegregation often occurs between the surface and core of the casting, with the alloy composition of the surface (which freezes first) being different from the centre owing to diffusion of alloy elements ahead of the solid/liquid interface. Alloying elements can either diffuse from the liquid into the solid, which raises the alloy content near the surface, or the elements can migrate from the solid into the liquid which enriches the central region of the casting. The mechanical properties vary from the surface to centre of the cast metal owing to the change in alloy content. The effect of macrosegregation on the properties can be minimised by hot working the cast metal; this involves plastically deforming the casting at high temperature and redistributing the alloying elements.
Microsegregation is the local variation in alloy composition on a scale smaller than the grain size. Microsegregation occurs over short distances, often between the dendrite arms which are typically spaced several micrometres apart. The dendrite core, which is the first solid to freeze, is richer in the alloying elements with higher melting temperatures.
Segregation can be removed by a heat treatment process known as homogenising anneal, which involves heating the solid metal to just below the melting temperature for an extended period of time to allow the alloying elements to disperse throughout the casting. Homogenisation treatments are generally effective in producing a levelling of micro-scale concentration differences in alloying elements, although some residual minor differences may remain.
The presents a case study of casting defects causing engine disc failure on United Airlines flight 232.
Leave a Reply