Figure 3.10 shows the main sections and internal structure for a typical modern helicopter. The main body (or airframe) of the helicopter is most heavily loaded at two points: the connection to the tail boom and the connection to the main rotor drive shaft or turbine engine. The tail boom applies torsion and bending loads to the body during flight whereas high tension and shear forces occur around the drive shaft connection. To carry these loads with a weight-efficient design, the main body is constructed with a truss frame network covered with a thin skin. Most of the load is carried by the frame which consists of longitudinal, transverse and inclined beams. The frame and skin of modern helicopters are constructed of aluminium alloy or fibre–polymer composite or some combination of the two. The aluminium alloys used in helicopters airframes are usually the 2000 (Al–Cu) and 7000 (Al–Cu–Zn) alloys whereas the composite is usually carbon fibre–epoxy. Composite material is also used in the helicopter body in preference to aluminium alloy when a high strength-to-weight ratio is required. Glass-fibre composite may be used in the more lightly loaded body components and aramid composites are used in structures where vibration damping is required (such as around the drive shaft) or high-energy absorption (such as the underfloor). Titanium alloy or stainless steel can be used in regions of high stress or heat.
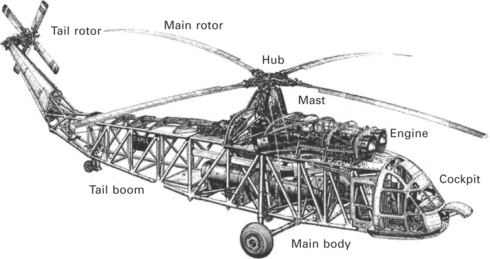
3.10 Structural design of a typical helicopter. (from Flight International)
The main rotor consists of a mast, hub and blades. Main rotor systems are classified according to how the blades are attached and move relative to the hub. There are three basic classifications: rigid, semirigid and fully articulated. Some modern rotor systems use a combination of these types. When the main rotor turns it generates both the aerodynamic lift force that supports the weight of the helicopter and the thrust that counteracts drag in forward flight. The main rotor also generates torque that tends to make the helicopter spin, and the tail rotor is used to counteract this effect. On twin-rotor helicopters the rotors spin in opposite directions, and this cancels the torque reaction.
The mast is a cylindrical shaft that extends upwards from, and is driven by, the transmission. The material properties for the mast include high elastic modulus, strength and fatigue resistance, and, therefore, it is usually made of high-strength steel or titanium alloy. At the top of the mast is an attachment point for the rotor blades called the hub, which can be made using a variety of high-strength materials such steel, titanium or composite. The blades are long, narrow airfoils with a high aspect ratio, and this design minimises the drag resistance from the tip vortices. Helicopters have between two and six blades attached to the hub, and each blade produces an equal share of the lifting force. Rotor blades are made from various metals, including aluminium, steel, titanium, and composites such as carbon-epoxy laminate or sandwich materials with a lightweight honeycomb core. Figure 3.11 shows the materials used in the blades of a Sea King helicopter. Carbon–epoxy composite is used extensively in blades because of their light weight, high strength, potential for multi-functional design, and, most critically, fatigue resistance. Rotor blades experience many tens of millions of load cycles over the average life of a helicopter, and composites can extend the service life by a factor of up to 200 compared with aluminium blades. The leading edge of the blade is covered with an erosion shield made of stainless steel or titanium to resist damage from impacting dirt particles kicked-up from the ground during take-off and landing.
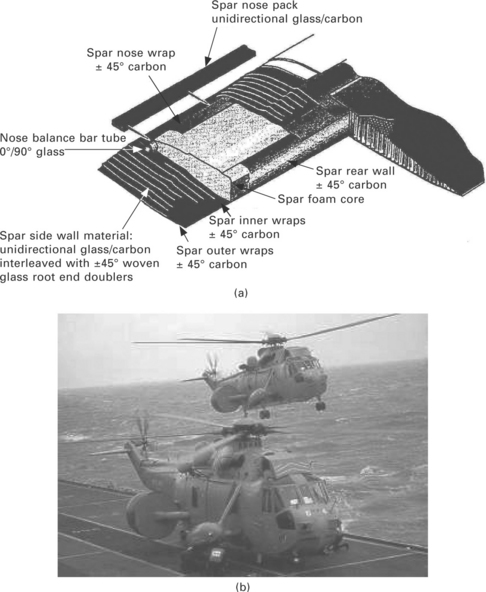
3.11 Material structure of the main rotor blade for the Sea King helicopter. ((a) from M. R. Edwards, Materials for military helicopters, Proceedings of the Institution of Mechanical Engineers, Part G: Journal of Aerospace Engineering, 216 (2002), 77–88)
The tail boom is constructed of hollow aluminium or carbon-fibre composite tubes and frames extending from the rear of the main body. On the other end is the tail rotor assembly. The boom houses the drive mechanism for the tail rotor. The tail rotor is a smaller, vertically mounted rotor whose role is to control yaw, including acting counter to the torque reaction of the main rotor. The tail rotor blades are similar in construction to the main blades, and are often made using a combination of metals and composites. The tail rotor can be enclosed within a metal or composite casing to protect the blades from erosion and bird strike.
Leave a Reply