It is not possible to fully understand the topic of aerospace materials without also understanding the aerospace structures in which they are used. The choice of aerospace materials is governed by the design, function, loads and environmental service conditions of the structure. Understanding aircraft structures allows aerospace engineers to select the most appropriate material. The materials used in safety-critical structures, which are structures that can result in loss of the aircraft when they fail, require high mechanical properties and excellent durability in the aviation environment. Examples of safety-critical structures are the fuselage, wings, landing gear and empennage. The main components in gas turbine engines are also safety-critical, such as the turbine blades and discs.
The materials used in aircraft structures require a combination of high stiffness, strength, fracture toughness, fatigue endurance and corrosion resistance. Aerospace materials must carry the structural and aerodynamic loads while being inexpensive and easy to fabricate. The materials must also be damage tolerant and provide durability over the aircraft design life, which for military fighter aircraft is typically in the range of 8000–14 000 flight hours (over a period of 15 to 40 years) and for large commercial airliners is 30 000–60 000 flight hours (25–30 years). During this period, the aircraft structures should not crack, corrode, oxidise or suffer other forms of damage while operating under adverse conditions that involve high loads, freezing and high temperatures, lightning strikes and hail impact, and exposure to potentially corrosive fluids such as jet fuel, lubricants and paint strippers.
In addition to high mechanical properties and long-term durability, it is essential that the materials are light. The airframe accounts for a large percentage (typically between 20 and 40%) of the all-up weight of most aircraft, and any savings in weight by using light materials which are structurally efficient result in less fuel burn, greater range and speed, and smaller engine requirements. Table 3.1 presents a breakdown in the mass of the main structures of several aircraft types as a percentage of the total weight. The other mass of the aircraft is comprised of the power plant, fuel, instruments, equipment, cabin fittings and payload, as shown in Fig. 3.1.
Table 3.1
Breakdown of structural weight for various aircraft types as a percentage of total weight
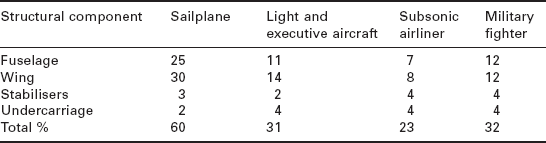
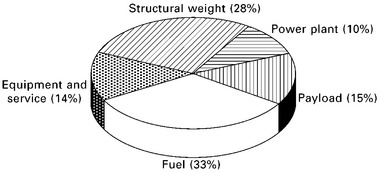
3.1 Approximate breakdown of take-off weight of large passenger aircraft.
The presents an overview of the safety-critical structures for aircraft, helicopters and spacecraft. The main structures in fixed-wing aircraft, which are the fuselage, wings, empennage, control surfaces, undercarriage, and gas turbine engines are examined. The loads and environmental service conditions for these structures are briefly explained. The key mechanical and durability properties required by the materials used in the different structures are discussed, and the types of materials that are used are identified. The also presents a short overview of the main structures in helicopters, and describes the types of materials which are used in the main body, tail boom and rotor blades. The main structures in re-entry spacecraft such as the space shuttle are explained, and again the materials which are used are identified.
Leave a Reply